Advanced Tutorial on Wireless Communication and Electronic Tracking: CT System Safety
5.0 CT System Safety
One of the main goals of the MINER Act is to increase mine safety by providing two-way communications between miners and surface personnel, especially following a significant accident. In addition, electronic tracking is required to allow surface personnel to determine the current, or at least immediately pre-accident, locations of all underground mine personnel. The CT systems being proposed must be assessed to ensure they do not introduce new hazards. Some of the areas of concern are the permissibility in a potentially explosive atmosphere; electromagnetic radiation (EMR) hazards to personnel, fuels, and blasting caps; and electromagnetic compatibility between RF-emitting systems. These concerns are individually addressed in the sections below.
5.1 Permissibility
Ventilation is required in coal mines to prevent the buildup of methane gas and reduce coal dust levels. However, following certain emergency situations there is concern that the ventilation flow may have been compromised. For example, a roof fall or water inundation may obstruct airflow resulting in a buildup of methane or other flammable gases, creating a potentially explosive or flammable atmosphere. The electrical power to the mine is then shut down for reasons of safety. Under such circumstances, CT systems can only be allowed to remain powered if they are MSHA approved as permissible, i.e., able to safely remain electrically powered in a methane-air or coal dust atmosphere.
There are two methods by which the MSHA-permissible designation can be obtained. For the first method, the equipment is installed in an explosion-proof (XP) enclosure. For the second method, it has to be shown that the equipment, even if it fails, cannot release sufficient energy to initiate an explosion or fire. In the latter case, the equipment is classified as intrinsically safe (IS). These two permissibility designations are discussed in detail below.
Methane or coal dust explosions and fires are some of the greatest hazards faced by underground coal mine workers. Methane gas is released during the mining process and accumulates in areas that are not well ventilated. Coal dust accumulations pose a fire hazard, and coal dust can form explosive dust clouds when entrained into the air. Methane-air ignitions or blasting explosives can disperse coal dust layers into the atmosphere that subsequently ignite and propagate as powerful coal dust explosions.
The term “permissible” refers to equipment that meets specifications for the construction and maintenance of such equipment, and ensures that such equipment will not cause a mine explosion or mine fire [30 CFR 75.2]. Electrical equipment that is normally exposed to methane or coal dust inby the last open crosscut [30 CFR 75.500], or within 50 m (150 ft) of pillar workings or longwall faces [30 CFR 75.1002], or in return entries [30 CFR 75.507], must be permissible. The requirements of 30 CFR 75.313 for electrical equipment apply when main mine fan stoppage occurs with persons underground. The 30 CFR 75.323 requirements for electrical equipment apply when excessive amounts of methane are present in a working place or in an intake air course, including an air course in which a belt conveyor is located.
Requirements for permissible CT equipment designs are governed by 30 CFR Part 23 (Telephones and signaling devices) and 30 CFR 18.68 (Tests for intrinsic safety). These 30 CFR requirements are supplemented by a number of MSHA policies and test procedures that may be obtained online through the MSHA webpage Title 30 CFR .
As mentioned above, the two primary methods of electrical equipment explosion protection recognized by MSHA are explosion-proof enclosures and intrinsic safety certification, described in the following sections.
5.1.1 Explosion-Proof Enclosures
Sparks, electrical arcs, and hot surfaces have the thermal potential to ignite a mixture of coal dust or methane-air mixtures. One of the ways to mitigate these hazards is to house electrical and electronic devices in explosion-proof (XP) enclosures. Figure 5-1 shows an example of an XP enclosure. XP enclosures meet specific design criteria to ensure that, should the device within the enclosure ignite a methane-air mixture, the ignition will not propagate outside of the enclosure. MSHA describes the design guidelines and testing procedures for the XP designation in 30 CFR Part 18. An example of the use of an XP enclosure might be for a backup battery which powers leaky feeder line amplifiers when the main mine electrical power is shut off.
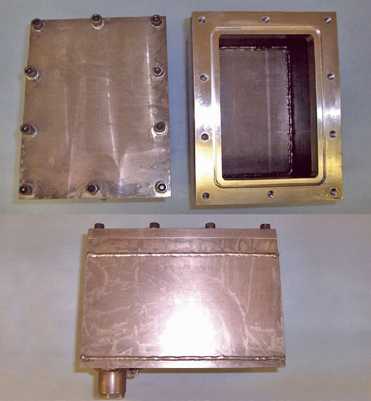
5.1.2 Intrinsic Safety Certification
An alternative or additional approach to obtaining MSHA-permissible equipment approval is through the intrinsic safety (IS) certification. Intrinsically safe equipment and wiring is designed to be incapable of releasing sufficient electrical or thermal energy under normal or abnormal conditions to cause ignition of a coal dust or a methane-air mixture, even if the mixture is at its most easily ignited concentration. In many cases, where IS circuits are powered through the mine electrical system, an energy-limiting barrier is required. Under fault conditions, the barrier prevents potentially dangerous voltage or current levels from reaching the hazardous area.
The MSHA IS test requirements are specified in 30 CFR Part 18.68. There is further clarification of IS requirements in MSHA documents ACRI2001, “Criteria for the Evaluation and Test of Intrinsically Safe Apparatus and Associated Apparatus,” and ACRI2011, “Intrinsically Safe Active Voltage/Current Power Source Criteria.” A number of other policy and standardized test procedure documents pertaining to IS can be obtained online through the MSHA Approval and Certification Center webpage.
5.2 Battery Requirements
Batteries are a necessary source of backup power for CT systems following an accident. MSHA is responsible for establishing the requirements for the operational duration of standby power. A representative requirement might be to provide at least 24 hours of standby power based on a 5% transmit time, 5% receive time, and 90% idle time duty cycle, denoted as 5/5/90. The reader should verify the latest MSHA requirements for battery duty cycles. Additional MSHA battery requirements can be found in 30 CFR Part 7 Subpart C. Ideally, CT systems and devices should be designed to support easy, safe underground battery replacement, even under extreme conditions (e.g., methane and/or coal dust environment). Miners should be trained to prevent abuse or mishandling of batteries. There are many different battery-powered CT components; mine operators should establish procedures to ensure that batteries are not lost or discarded underground.
Generally, batteries have too much stored energy to be considered intrinsically safe unless special design features, such as a current-limiting resistor, are integrated with the battery terminals to limit the energy delivery rate. High-energy storage batteries may be maintained in XP-compliant enclosures (see Section 5.1.1 and also 30 CFR Part 7). One concern is that the XP enclosure may not survive a roof collapse, and therefore a hazardous situation could occur. Damage is also a concern for IS devices with lithium-type batteries which, for example, may be susceptible to thermal runaway. Lithium battery safety is a subject of ongoing research, but these batteries appear to present potentially greater risks to safe operation than other battery chemistries.
Stationary CT equipment will be on charge and unattended for long periods of time. If possible, stationary equipment containing batteries should not be located in return air entries. Both the state of charge and health of batteries should be visible on the batteries or stationary equipment and/or displayed in the MOC.
Some areas of further investigation for batteries are listed below:
- What operational time (battery life) is needed? How does this compare to current battery technology and available CT system capabilities?
- What overall CT system designs and application strategies could help to increase available operation time?
- Battery-related issues in portable devices, such as hand-held radios, include the following: capacity (operating time), size, weight, limitations on safe locations for recharging or battery change-out, potential failure modes and consequences, use of battery types (such as various lithium chemistries) that may present an increased hazard in explosive atmospheres or near flammable material, and MSHA approval of new battery-powered equipment designs.
- Battery-related issues in fixed installations, such as radio repeaters or wireless mesh nodes, include the following: size and energy available, battery type, provisions for operation in an explosive atmosphere and near flammable material, protection afforded by an enclosure from physical/environmental damage (particularly from roof falls), charging safety, remote status/condition monitoring, meaningful condition testing, remote and/or local control of output (on/off), potential failure modes and consequences, and regular maintenance requirements.
- Development and acceptance of standard operating procedures for use of battery-powered CT systems under emergency conditions when normal underground power distribution has been disconnected.
5.3 Hazards of Electromagnetic Radiation
Electromagnetic radiation is pervasive in our environment. It allows us to receive satellite TV stations, listen to AM or FM radio stations, make and receive cell phone calls, and download emails to a Blackberry. Nevertheless, none of the radiation that allows these devices to work can penetrate the overburden of a mine. Hence, the EM environment in the mine will be determined largely by whatever radiation sources already exist within the mine, along with any new wireless devices being introduced. One required task is to ensure that the RF-emitting devices not interfere with each other; this topic is covered in Section 5.4. Another required task is to identify and address any safety issues and hazards that might arise with the introduction of the CT system. In the mine environment, the following three areas may be adversely impacted by EM radiation or what is commonly called radiation hazards (RADHAZ): personnel, explosive atmospheres, and electrically initiated devices (e.g., blasting caps).
5.3.1 Personnel
When a communications or tracking system radiates RF energy, workers in proximity to the radiating system may suffer health effects if the radiation levels are too high. These negative effects are often referred to as hazards of EM radiation to personnel (HERP). There are well-recognized standards [IEEE C95.1-2005; 47 CFR 1.1310] that describe the acceptable levels of radiation that do not pose a concern to humans. The acceptable radiation levels depend on the frequency, power levels, and distance of the radiators from the person.
All the CT systems proposed for use in mines produce only nonionizing radiation. This means that the RF radiation has insufficient energy to ionize atoms (strip off electrons), unlike x-rays, for example. However, the nonionizing radiation can cause electrostimulation (electrical shock) or thermal heating effects in humans. A HERP analysis on representative CT systems has been completed in a Joint Spectrum Center report [JSC 2008c]. A broad summary of the findings is that no hazard exists except possibly in the highest power radiating devices—those with 4- or 5-watt power ratings. For high-power devices, there may be a concern with holding the transmitter against the head for extended periods of continuous transmission (greater than 6 minutes).
5.3.2 Explosive Atmosphere
Coal mine operations generate coal dust and methane gas which is released in the mining process. Within a concentration range of 5 to 15% of methane in air, the mixture is flammable and possibly explosive. Radiated RF energy can couple to conducting objects and possibly create a spark that ignites the methane-air mixture, causing a hazardous situation. This is sometimes referred to as hazards of EM radiation to fuels (HERF).
There is an international standard [IEC 60079-0 (2007)] that assesses the risk of inadvertent ignition of flammable atmospheres by RF-transmitting devices operating over a frequency range from 9 kHz to 60 GHz. Within the standard, threshold radiated power levels are defined, below which there is no hazard, and above which a potential hazard exists. Hazards of mine CT systems in an explosive atmosphere have been evaluated in a publication by the Joint Spectrum Center [JSC 2008c]. A broad summary of the conclusions within the document is that devices with power ratings under 6 watts should present no HERF hazard (including the presence of diesel fuel).
5.3.3 Electro-explosive Devices
Electro-explosive device (EED) is a general term for devices such as electrically initiated blasting caps. A potential hazard is that radiated RF energy in the environment may couple into the leg wires (leads) of an EED and cause an unintended explosion. RF safety concerns with EEDs can be broken into transportation and deployment.
Regulations regarding transportation and packaging of EEDs from the manufacturer are specified by MSHA in 30 CRF 77 Subpart N; by the Occupational Safety and Health Administration (OSHA) in 29 CFR Subparts H and U; and by the Department of Transportation (DOT) in 49 CFR 173. What is not specifically addressed in these regulations is the underground transportation of EEDs that may have been removed from their original packaging and may be in the vicinity of RF-radiating CT systems.
EEDs are shipped from the manufacturer with their leg wires coiled and the ends shorted together to minimize the potential for RF energy coupling to the wires. EED manufacturers have decades of experience with shipping and handling of these devices, but not in the underground mine environment with new CT systems installed.
It is challenging to determine the RF environment experienced by an EED underground where RF energy can reflect off the walls, floor, and roof, then couple and be reradiated from conductors within an entry. Quantitative analysis of this RF hazard in the mine environment is an area of ongoing research. In the near future, the safest recourse may be to use highly efficient RF shielding, such as shown in Figure 5-2. These enclosures or shielding blankets provide 50 to 60 dB of attenuation of RF signals from 1 MHz to 3 GHz using only one layer of RF-absorbing material. Such RF shielding should more than adequately protect EEDs from intercepting sufficient RF energy to detonate.
![Figure 5-2. Examples of RF-shielding enclosures [TE3MI 2009].](../../../UserFiles/content/emergencymanagementandresponse/commtracking/commtrackingtutorial2/5-2.jpg)
Besides transportation, the other RF safety concern with EEDs occurs during deployment. During deployment, the leg wires of a blasting cap may be extended and the short removed from the ends of the leg wires, as shown in Figure 5-3. Thus, the leg wires can act as a conducting antenna. If the length of the leads L, is about half a wavelength or greater, the RF radiation will very effectively couple to the leads. The result is that significant RF energy can be deposited in the resistive heating element (or bridge wire) of the blasting cap causing the blasting cap to fire. The risk can be mitigated by maintaining a minimum distance of separation between RF emitters and the blasting cap leads.
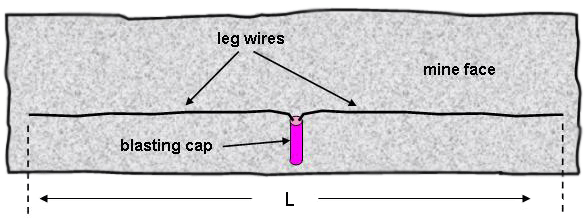
There is an IEEE standard C95.4 [IEEE 2002b] to determine the required separation distance for various RF emitters from blasting caps. Unfortunately, the IEEE and other standards do not account for additional effects that occur in the mine environment. For example, UHF waves from an emitter can reflect off the floor, ceiling, and walls of an entry to substantially increase the energy incident on the blasting cap leg wires. At MF frequencies, longitudinal conductors in an entry can enhance the incident fields on a blasting cap by a factor of five [Thompson et al. 1985]; these effects are not accounted for in the standards. This is an active area of research for NIOSH.
Based on the standards, if the RF power received by the blasting cap leads is below a threshold value of 40 mW [IEEE C95.4 2002a], there should be no inadvertent firing of the cap due to receipt of RF energy. The received RF power of the blasting cap should be validated either by direct measurements or by aid from a properly experienced consultant. Lacking either of these approaches, it is recommended that all UHF or higher frequency transmitters be kept at least 60 m (200 ft) from electric blasting caps during deployment, and all MF transmitters should be turned off.
5.4 Electromagnetic Compatibility
Two terms that are often encountered when discussing the proper operation of electronic equipment in an RF environment are electromagnetic interference (EMI) and electromagnetic compatibility (EMC). EMI occurs in a system when undesired electromagnetic energy interferes with the reception or processing of a desired RF signal. EMC is a desired condition which prevails when electric systems are performing their particular desired functions while in the presence of other systems. In effect, EMC is established when any potential EMI between systems has been eliminated or effectively managed. EMC has two aspects—a system under consideration can be a source of interference or it can be a victim of interference. More specifically, from the source of interference perspective, the system should not generate RF disturbances that cause a malfunction in another system (usually referred to as the emissions aspect). From the victim of interference perspective, the system should be able to operate in its EM environment without risk of malfunction (usually referred to as the immunity aspect or susceptibility aspect). These topics are discussed in greater detail in the following subsections.
5.4.1 Electromagnetic Interference
EMI is due to electromagnetic energy that either causes a malfunction in an electrical system or equipment, or interferes with the reception or processing of a desired signal. EMI may result from intentional RF emissions and proper operation of equipment, or it may be from unintentionally generated RF emissions. A hand-held radio is an example of an intentional RF emitter, and a computer is an example of a device that emits RF signals (though this is not the intention or purpose of the device). EMI effects may be categorized as mild, medium, or severe, depending on the reaction of the victim equipment.
EMI of electrical equipment occurs because of inadvertent susceptibilities of the equipment. EMI is usually associated with coupling paths from one antenna to another antenna, although other types of coupling paths (e.g., from an antenna directly to the circuitry on the inside of a system cabinet) are possible.
Electrical and electronic systems or equipment can interfere with one another in many ways. Every RF interaction between a source and a victim requires four things to occur before it is determined that interference has occurred. First, there must be an emission of EM energy from the source (transmitting) system. Second, the emitted EM energy propagates along some path to the victim (receiving) system. Third, the EM energy incident on the victim system finds a low-loss path to the system’s internal circuitry. This path may be through the victim’s antenna or it may be through a gap or seam in the victim’s housing. Fourth, when the undesired signal has sufficient strength to degrade the performance of the victim system, an interference situation occurs. This generally occurs when the strength of the undesired signal from the source exceeds a particular threshold level for the victim. The degradation could take the form of an undesirable or unacceptable response of the victim, an interruption in service, or a malfunction.
The major EMI concerns are as follows:
- Co-channel interactions, where other systems operating on the same frequency interfere with each other;
- Adjacent-channel interactions, where systems in the same frequency band, operating on nearby frequencies, interfere with each other;
- Adjacent-band interactions, where systems in adjacent frequency bands operating on nearby frequencies interfere with each other;
- Harmonic interactions, where systems operating on a harmonic frequency interfere with each other.
These concerns are discussed in further detail in Appendix B Section B.6.1. Additional EMI concerns are discussed in a Joint Spectrum Center report [JSC 2008b].
Methods to mitigate EMI address one or more of the four conditions required for EMI to exist. Changes can be made to the transmitting system, to the receiving system, to RF shielding, and possibly to the transmission medium to offset EMI effects. EMI mitigation techniques include frequency management, reduced transmitter power, increased antenna separation, antenna radiation control (directing the antenna radiation pattern), narrowed receiver selectivity, and filtering.
5.4.2 Standards and Regulations
Usage of the electromagnetic spectrum is regulated by two different agencies: the Federal Communications Commission (FCC) and the National Telecommunications and Information Administration (NTIA). The FCC regulates commercial use, and the NTIA regulates government use of the spectrum. Regulations stipulate what types of RF-emitting or receiving devices are permitted to operate using a certain portion of the EM spectrum, and what transmission power levels are acceptable. FCC regulations are published in the CFR. For example, 47 CFR Part 15.211 presents FCC regulations regarding tunnel radios (radios for use in tunnels and underground mines).
Traditionally, the FCC has largely focused on protecting commercial radio and TV broadcasts from interference. The FCC has very few regulations regarding the susceptibility of equipment to EMI, preferring to leave this quality feature to manufacturers to support (i.e., manufacturers making a device that is less susceptible to EMI will presumably sell more devices).
Standards, unlike regulations, are in themselves voluntary, although some regulations may require meeting a specific standard. Standards aimed at minimizing RF interference tend to address EMC rather than EMI. There are few commercial U.S. standards that address EMC. The military, on the other hand, has very detailed standards on EMC.
Military equipment often contains multiple systems for communications with soldiers on the ground, aircraft, satellites, guided munitions, and may have RF systems for emitting and receiving radar information. In many cases, these systems are expected to operate simultaneously and without conflict, often in close proximity to each other. The military has developed detailed standards that can provide guidance for EMC in underground coal mine CT systems. For example, military equipment is often required to meet military standard MIL-STD-461F [DoD 2007], which could be tailored for underground coal mine CT systems.
MIL-STD-461F establishes emissions limits that are intended to control RF signals that may be conducted through external attached wiring or radiated from a source (transmitting) system. MIL-STD-461F also establishes limits on the susceptibilities, either conducted or radiated to a victim (receiving) system. The emissions from a source generally include out-of-band products such as harmonics and spurious emissions, whereas the susceptibilities of a victim include reactions such as spurious responses to out-of-band inputs. Conducted emissions and susceptibilities are conducted in or out of a box via wires such as power cords, whereas radiated emissions and susceptibilities are radiated from the box or from the antenna. The limits of MIL-STD-461 have been established at emissions and susceptibility levels which result in a high likelihood that two systems, both meeting the limits and separated by a typical coupling path, will be compatible with each other.
MIL-STD-461F is designed for military electrical systems which can have very high-power radiating systems and many electrical systems compactly installed. The coal mine EM environment is quite different; hence, the limits on emissions and susceptibility have to be adjusted appropriately [JSC 2008b]. The intent is to achieve electromagnetic compatibility between systems at a reasonable cost.
5.4.3 Design and Construction Guidelines
One approach to mitigate EMI effects is through the use of shielding. Shielding is a design approach for keeping undesired EM noise and signals off susceptible equipment by strategic use of materials that reflect RF energy. One type of shielding is a metal barrier around electronic components, wires, or cables.
To demonstrate, twisted-pair wires are not shielded; hence signals from a nearby transmitter may be coupled onto the wires. Non-twisted wires are even more susceptible to RF coupling than twisted wires. The unintended signals could then be conducted into other equipment connected to the wires, possibly causing EMI. For this reason, coaxial cables can be important in reducing EMI. In a coaxial cable, the outer conductor is a shield that prevents most of the incident RF from reaching the internal conductors.
Electronic circuitry can also be shielded from radiated RF influence by packaging the circuits in conducting enclosures. It may be necessary to use specially designed RF seals at apertures, access points, and seams in the enclosure to reduce RF penetration into the enclosure. An example of such a consideration might be a carbon monoxide (CO) sensor that is mounted in a plastic enclosure. The sensor may give erroneous readings if a hand-held radio is too close. The sensor could be hardened by using a metal enclosure instead of plastic.
Grounding is a design approach whereby all structures and equipment are maintained at the same electrical potential, usually physically connected to the earth through a low-resistance path. When this has been accomplished, the potential difference, or relative voltage, between any two points would be zero. In this way, electrical charges on equipment are carried away from the equipment without a chance to build up to the point where there could be an electrical discharge, potentially causing a fire or explosion. In addition, radiated noise due to the electrical charges and currents is minimized.
The enclosures (i.e., chassis, cabinets, boxes, cases, etc.) of electrical and electronic equipment should be installed to ensure a continuous low-impedance path between all adjoining or contacting surfaces. All exposed metal parts of equipment should be electrically grounded. For any equipment connected to the mine’s electrical system, the power supply cable should include an extra conductor that is grounded inside a power panel, a connection box, or a receptacle. If it is not feasible to install a ground wire in the power supply cable, the enclosure may be grounded by means of a braid strap bolted to the enclosure.
See Also
- Advanced Tutorial on Wireless Communication and Electronic Tracking: Appendix B
- Advanced Tutorial on Wireless Communication and Electronic Tracking: Electronic Tracking Systems Performance
- Development of a Uniform Methodology for Evaluating Coal Mine Tracking Systems
- Medium Frequency Radio System Modifications for Refuge Chamber Situational Awareness
- Mine Communications and Tracking Glossary
- Post-Accident AMS System
- Radio System Modifications for Improved Mine Safety (Medium Frequency)
- Supplementary Technologies for Advanced Mine Communication Networks
- Technology News 544 - New Measurement Tool to Validate Wireless Communications and Tracking Radio Signal Coverage in Mines
- Through-The-Earth Wireless Real-Time Two-Way Voice Communications
- Page last reviewed: 10/25/2013
- Page last updated: 10/25/2013
- Content source: National Institute for Occupational Safety and Health, Mining Program