module list
ELEMENTS OF ERGONOMICS PROGRAMS
Step 5: Evaluate Your Ergonomic Program
Follow up on your intervention
Follow up on your interventions to ensure the controls you implemented reduce or eliminate the WMSD risk factors. Ensure that no new WMSD risk factors were created. Since workers may be sore from doing their jobs differently and using new muscle groups, check with workers after one week and again after one month following an implementation. Adjusting to work is also important for new and return-to-work employees, particularly for tasks that are highly repetitive, such as paced work on a fast conveyor line or picking items with a time standard. New employees need about two weeks to condition their muscles. During the adjustment period it is not unusual for new hires or employees returning from a long absence to report muscle soreness.
Determine the effectiveness of your intervention
You can use a variety of techniques to measure the effectiveness and benefits of your ergonomic program. Compare the following data before and after the intervention:
- job analyses
- checklists
- symptom surveys
- OSHA form 300 logs
- employee absentee rates
- turnover rates
- workers’ compensation costs
- productivity indicators
- quality of products and services
- savings
Remember that workers will not experience the benefits of your ergonomic program immediately. It can take months for old MSD symptoms to disappear, and you will need to modify your intervention if new MSD symptoms appear.
Cost Analysis
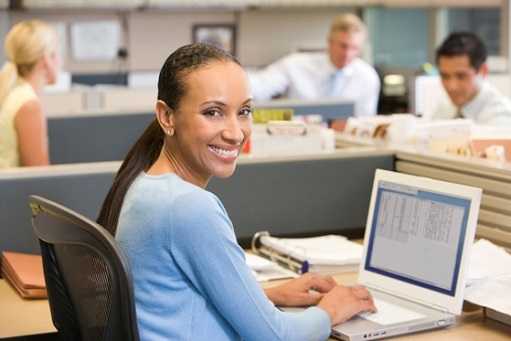
The equations and examples below will help you to see the economic value for your ergonomics program(s). You can use the benefit-cost ratio to determine whether or not your investments in the program(s) will be cost effective. By calculating the Return on Investment and conducting a cost-benefit analysis, you can better plan the implementation of your program(s).
The benefit-cost ratio measures the present or annual worth of a project or proposal’s benefit cost related to the initial cost (Badiru & Omitaomu, 2007). If the ratio is greater than the investment it shows benefits out way the cost. If the ratio is equal, then the investment is a break even. If the ratio is less than the investment it shows the cost out way the benefits.
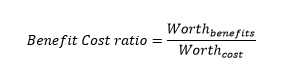
Return on Investment (ROI) can be calculated as the amount of time it takes to recover the cost of the initial investment.
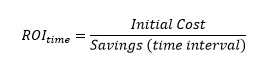
Example Problem
Metals Recycling Company wants to replace their current loading dock and fork lift system to transport scrap metal with 2 new scrap conveyor systems. The company runs production 365 days per year. The total for both scrap conveyor systems installed is $53,800. They estimated that the new system saves a total of 3 hours per day. Their employees are paid $23.00 per hour so savings per day is $69 per day.
Total Cost of Equipment | $53,800 |
---|---|
Savings on time | ![]() |
Return on Investment | ![]() |
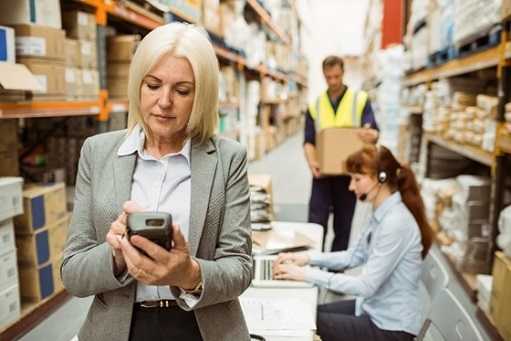
Cost-benefit analysis (pay-back period) is the amount of time it takes for the benefits to pay back on the cost of investment. It includes factors outside of investment such as savings from injuries prevented.
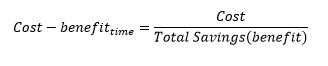
Example Problem
Reviewing other cost factors showed the old system has the potential for employees injuring themselves from manual lifting to load the fork lift. By changing to the new system a direct cost avoidance from potential sprains ($30,000) and back strain ($33,000) was $63,000 over a year. The cost-benefit is the cost of equipment divided by the estimated benefits for one year. The saving benefits are injury savings plus increased productivity over the year. In this case increased productivity is $69/day*365days/year=$25,185.00/year.
Total Cost of Equipment | $53,800 |
---|---|
Total Saving Benefits | ![]() |
Cost Benefit (payback period) Accounting for injuries prevailed |
![]() |
For more assistance with insurance policies and requirements, view the following Department of Health and Human Services’ publication Workers’ Compensation Insurance: A Primer for Public Health
Learn More on Resources for Cost Estimators & Evaluating Program:
- Cornell Return On Investment Estimator
- OSHA direct cost estimator
- Guide to Evaluating the Effectiveness of Strategies for Preventing Work Injuries
- Does it Really Work? How to Evaluate Safety and Health Changes in the Workplace
- OSHA’s Business Case for Safety & Health
- Health & Safety Ontario
- The business case for safety and health at work: Cost-benefit analyses of interventions in small and medium-sized enterprises
- Safety & Health add Value
- NSC Journey to Safety excellence
- Page last reviewed: July 18, 2017
- Page last updated: July 18, 2017
- Content source:
- National Institute for Occupational Safety and Health Division of Applied Research and Technology