NIOSH Research Rounds
NIOSH Research Rounds is a monthly bulletin of selected research conducted by researchers at NIOSH and NIOSH-funded researchers at other institutions.
Volume 3, Number 2 (August 2017)
Inside NIOSH:
3-D and Laser Printer Emissions Compared
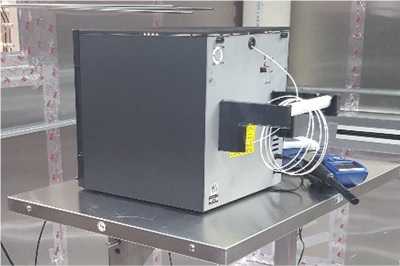
Using the test chamber, above, researchers found that 3-D printers emit 14 chemicals that laser printers do not. Photo from NIOSH
With the growing popularity of 3-D printers in the workplace, it is important to understand and address their potential effects on indoor air quality. In fact, all printers, including the older laser printers, emit chemicals into the air.
At NIOSH, researchers study emissions from various types of printers to find ways to prevent exposure to workers. A previous study by NIOSH and university researchers found that using the manufacturer-supplied cover on the 3-D printer decreased the amount of emissions containing ultrafine particles by two times, but the levels were still high.
The current study, published in the Journal of Occupational and Environmental Hygiene, measured printer emissions using a specially designed stainless steel chamber that can be set to simulate realistic office conditions in terms of temperature and humidity. Researchers tested the most commonly used type of desktop 3-D printer, called the FDM, and two models of black and white laser printers. For the 3-D printers, the researchers printed a hair comb using one of two types of plastic filaments. The printing time for each comb was about 14 minutes.
They found that certain chemicals, known as volatile organic compounds, were significantly lower with laser printers compared to 3-D printers. At the same time, the 3-D printers emitted 14 chemicals that laser printers did not emit. In addition, 3-D printer emissions likely combined to form other chemicals. Even after printing, 3-D printed objects emitted the chemical styrene, indicating that exposure beyond the actual process of printing may be a concern in the work place. Both the 3-D printer, using a certain type of plastic filament called ABS, and the laser printers emitted ultrafine particles that contained the toxic chemical chromium. The results of this research can help inform future studies aimed at measuring and controlling work-related exposure to 3-D printer emissions.
More information is available:
In This Issue
NIOSH Research Rounds is Brought to You By:
- John Howard, M.D., Director
- Christina Spring, Editor in Chief
- Anne Blank, Story Editor
- Cathy Rotunda, Copy Editor
- Glenn Doyle, Technical Lead
- Tonya White, Technical Support
Get Email Updates
Subscribe to the NIOSH Research Rounds Newsletter:
NIOSH Survey Finds Some but Not All Precautions Are Taken by Dental Practitioners to Minimize Nitrous Oxide Exposure
Nitrous oxide, or laughing gas, is the most common inhaled anesthetic used by dental practitioners. Although considered safe for occasional use in patients, studies show that long-term, work-related exposure may increase the risk of diseases of the nervous system, kidneys, and liver and of miscarriage and infertility. Fortunately, there are ways to minimize exposure of dental workers to nitrous oxide.
To examine whether recommended controls are used to minimize exposure to nitrous oxide during dental procedures, NIOSH surveyed 284 practicing dentists, dental hygienists, and dental assistants for the Health and Safety Practices Survey of Healthcare Workers. These respondents worked in private dental practices and reported administering nitrous oxide and no other anesthetic gases to their adult and pediatric patients in the 7 days prior to the survey. Findings were recently published in the Journal of Occupational and Environmental Hygiene.
The two primary controls used to minimize dental practitioners’ exposure to nitrous oxide and other anesthetic gases during procedures include (1) special masks for patients, known as nasal scavenging masks, and (2) local exhaust ventilation (i.e., a duct or hood positioned near the patient’s mouth). Both controls remove exhaled gas before it disperses into the room. Other controls include general room ventilation, regular inspections of equipment for leaks, training on the safe use of anesthetic gases, and monitoring of the air and health-related symptoms for possible exposure to nitrous oxide and other anesthetic gases.
The good news is that nearly all of the survey respondents reported using either nasal scavenging masks or local exhaust ventilation, with the former the preferred method of control. Other findings, however, showed that there is room for improvement related to administrative and work-practice controls:
- In the area of administrative controls, nearly all survey respondents reported undergoing training on handling nitrous oxide safely, but 85% of dentists and 63% of dental hygienists and assistants said that their training occurred more than a year prior to the survey. Though annual refresher training is not required, it would increase the likelihood that precautionary measures become second nature.
- Forty percent of respondents reported that they did not always check nitrous oxide equipment for leaks.
- Nearly all dentists reported safe handling procedures were available at their workplace, compared to only two-thirds of dental hygienists and assistants. Furthermore, one-third of dental hygienists and assistants said either that their workplace had no standard procedures or that they did not know if standard procedures were available.
- In the area of monitoring for exposures, less than 10% of all respondents reported that monitoring for nitrous oxide had occurred at their workplace within the past year. Similarly, survey respondents did not report consistent use of controls related to work practices. For example, nearly half said that they did not always check nitrous oxide equipment for leaks.
More information is available:
- Exposure Control Practices for Administering Nitrous Oxide: A Survey Of Dentists, Dental Hygienists and Dental Assistants
- NIOSH Health and Safety Practices Survey of Healthcare Workers
- NIOSH Division of Surveillance, Hazard Evaluations, and Field Studies
Lung Transplant Codes May Miss Work-related Disease
Diagnosis codes in the national registry for lung transplant recipients may miss cases of work-related lung disease, according to a NIOSH study published in the Journal of Heart and Lung Transplantation. These missed cases may complicate efforts to track the number of patients receiving lung transplants due to end-stage, work-related lung disease.
The United States Organ Procurement and Transplantation Network stores information for all lung-transplant patients in the country. Patients in the registry receive three diagnosis codes. They receive the first code when they become transplant candidates, the second when they join the waiting list, and the third when they receive a lung transplant. NIOSH researchers found that patients listed with diagnoses known to be work-related diseases frequently are not assigned work-related diagnosis codes for lung disease.
To find out how many lung-transplant recipients received an accurate diagnosis code for work-related lung disease, researchers evaluated registry records for U.S. adults who received a lung transplant from January 1987 to December 2014. They found that recipients with documented work-related lung disease received 10 different diagnosis codes in the registry, despite there being only two work-related codes. Even when patients first received a written diagnosis for work-related lung disease, almost half of these patients received a diagnosis code that was not work-related at the time of transplant. These findings show that studies relying solely on diagnosis codes in transplant registry records may miss a significant number of cases of work-related lung disease. Also, adding details to registry records about work histories, such as industries and occupations where transplant patients worked, would help to clarify the greatest risks for end-stage, work-related lung disease and improve efforts to protect the lung health of workers in particular jobs and industries.
More information is available:
- Misclassification of Occupational Disease in Lung Transplant Recipients
- NIOSH Respiratory Health Division
Outside NIOSH
Shut-off Guard Helps Prevent Entanglement in Winches on Fishing Vessels
Commercial fishing is one of the most dangerous occupations in the United States, with a 32 times greater risk of death compared to all other occupations, according to the most recent numbers from the U.S. Bureau of Labor Statistics. Falls overboard are a well-recognized risk, but onboard machinery can also pose a serious hazard.
A potentially dangerous piece of machinery on a fishing vessel is the winch—a powered, spool-like device used to wind up and wind out rope and nets. In some instances, often due to harsh weather or other hazardous working conditions, the winch mechanism can entangle crewmembers, sometimes with deadly results. Although an easily accessible shut-off switch can prevent winch entanglements, these switches are not always easy to reach in an emergency.
In a NIOSH-funded study at Bassett Healthcare, in collaboration with Harvard University, researchers and a private engineering company developed and tested at sea an innovative emergency winch shut-off guard for trawlers. These fishing vessels use winches to pull fishing nets, or trawls, through the water. The 4-year study began with a survey of more than 45 active sea captains in the Gloucester and New Bedford ports in Massachusetts. All survey respondents reported that they had onboard fluid-powered, or hydraulic, winches. Although most reported that they had a winch shut-off switch, more than one-third (39%) said that the switches were more than an arm’s length away from the winch operator. At this distance, the winch operator might not be able to shut off the winch immediately in the event of an emergency. Four focus groups with trawler captains in Point Judith, Rhode Island, provided general information on experiences, concerns, and advice on winches, as well as feedback on the proposed emergency shut-off guard.
After evaluating the survey and focus group results, the researchers developed a pressure-sensitive, stainless steel guard that, when pressed, triggers an electric switch to quickly shut off the winch. Subsequent tests at sea, conducted with the aid and assistance of Point Judith trawler captains, showed that the guard successfully shut down the winch in milliseconds. An added benefit is that the guard can retrofit on existing winches, eliminating the need to purchase new winches. Now, ongoing efforts focus on increasing awareness of the dangers of unguarded winches and on promoting the emergency guard to trawler captains. As part of these efforts, the researchers have published several articles in fishing industry trade papers.
While this study focused on hydraulic winches on New England trawlers, NIOSH engineers also considered how to address hazards from mechanical winches used in the Gulf of Mexico. Learn more about this related research, where NIOSH engineers developed and tested stationery guards for the most common types of winches used in the U.S. southern shrimp fleet.
More information is available:
- The Northeast Center for Occupational Health and Safety in Agriculture, Forestry and Fishing: Year in Review
- Winch Safety Project Trip (video)
- Preventing Fatal Winch Entanglements in the US Southern Shrimp Fleet: A Research to Practice Approach
- NIOSH Commercial Fishing Safety
- NIOSH Extramural Research and Training Programs
Disclaimer
Mention of any company or product does not constitute endorsement by NIOSH.
- Page last reviewed: August 10, 2017
- Page last updated: August 22, 2017
- Content source:
- National Institute for Occupational Safety and Health (NIOSH) Office of the Director