NIOSH Research Rounds
NIOSH Research Rounds is a monthly bulletin of selected research at the National Institute for Occupational Safety and Health.
Volume 1, Number 5 (November 2015)
Occupational Injury: Do Family Members Pay a Price?
When an occupational injury occurs, the effects can extend far beyond the worker and the workplace. Just ask family members who may have to take care of their injured relative or do additional household chores and errands. Hypothetically, this could mean a spouse or child helping to support a much larger, injured relative to move to the dinner table or a child lugging heavy laundry and groceries or moving furniture. But almost all occupational injury studies, including economic studies, focus on injured workers or their employers and the costs of healthcare and lost productivity either through or outside workers’ compensation, not on the possible repercussions for the injured worker’s family.
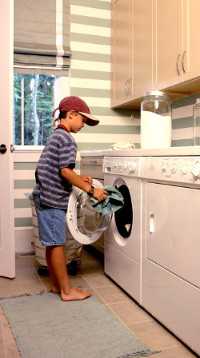
Workplace injury can affect family members, who often must do added chores. Photo by Richard Duncan, North Carolina State University, The Center for Universal Design (CUD), CDC Public Health Image Library
A pioneering study from the National Institute for Occupational Safety and Health (NIOSH) and Northern Kentucky University found that family members of severely injured workers filed more healthcare claims than family members of non-severely injured workers for fractures, sprains, joint dislocations, and other muscle and bone or “musculoskeletal” disorders. The researchers linked 17,238 workers’ compensation claims with family members’ outpatient healthcare claims for musculoskeletal disorders. They classified workers as severely injured, and therefore more likely to need physically demanding help from family members, if they received wage replacement or indemnity payments from workers’ compensation and were absent from work for at least 7 days.
Using 2005–2006 claims data from 37 large employers, the researchers found that, in the 3 months after the occupational injury, claims relating to musculoskeletal disorders among family members of severely injured workers exceeded those for family members of non-severely injured workers by 34%. The increase persisted even after the researchers accounted for other factors, such as pre-existing musculoskeletal disorders. Nationwide, the researchers estimated that these excess outpatient costs for family members of severely injured workers amounted to $29 million to $33 million per year during the study period.
Because their estimate did not include hospitalization claims or those submitted more than 3 months after injury, the actual excess costs for family members of severely injured workers could be even higher. To understand further the full toll of occupational injury on workers’ families, the researchers plan to assess additional family consequences of occupational injury. For example, what are the potential financial and emotional consequences?
To read the full article in the American Journal of Industrial Medicine, go to Musculoskeletal Disorders and Associated Healthcare Costs among Family Members of Injured Workers.
In This Issue
NIOSH Research Rounds is Brought to You By:
- John Howard, M.D., Director
- Fred Blosser, Editor in Chief
- Anne Blank, Story Editor
- Tanya Headley, Contributing Editor
- Ellen Galloway, Copy Editor
- Glenn Doyle, Technical Lead
- Tony Trucco, Technical Support
Get Email Updates
Subscribe to the NIOSH Research Rounds Newsletter:
To learn more about NIOSH research on the economic burden of worker injury and illness visit NIOSH Program Portfolio–Economics.
Slip-Resistant Shoes Reduce Food Service Workers’ Compensation Claims
Each year, food service businesses report that slips, trips, and falls are some of the most common causes of worker injury leading to time away from work. However, employers and workers can avoid slip, trips, and falls by keeping floors clean and dry, fixing flooring defects, using properly designed stairs and handrails, and, as a new study finds, by wearing slip-resistant shoes.
In this study, researchers at the National Institute for Occupational Safety and Health (NIOSH), in collaboration with industry partners, examined the effects of slip-resistant shoes on workers’ compensation claims related to slipping on liquid- or grease-contaminated surfaces among food service workers. Food service workers, who are responsible for preparing, cooking, and serving food, often encounter these slipping hazards on the job.
Participants in the study included about 15,000 food service workers employed by Aramark Education (K–12) at elementary, middle, and high schools from 227 school districts across 24 states. Researchers randomly assigned school districts either to receive or not to receive slip-resistant shoes. Workers who voluntarily chose to wear the shoes received free shoes throughout study, while workers at school districts that did not receive the shoes continued wearing their regular footwear, including their own slip-resistant shoes if they chose to.
Researchers compared data from the 2 years before participants received slip-resistant shoes with data from 2 years after they received them in both the intervention and control school districts. Preliminary findings from the 4-year study found more than an 80% reduction in workers’ compensation injury claims related to slipping on liquid- or grease-contaminated surfaces in the school districts that received slip-resistant shoes and were not using them previously.
Shoes for Crews, a manufacturer and supplier of slip-resistant footwear, supplied the shoes for the study, which ran from August 2009 to December 2013. Now, the researchers are studying whether the slip-resistant shoes will continue to prevent slips, trips, and falls, and if they are cost-effective. They plan to describe their findings in a paper to submit to a scientific journal in early 2016.
Disclaimer: Mention of company names or products does not constitute endorsement by the National Institute for Occupational Safety and Health.
National Survey of Long-Haul Truck Drivers Underscores Safety Concerns
When we go to the grocery store, we expect to find shelves stocked with the food we like, seldom reflecting on how it got there. Behind those stocked shelves, however, are the long-haul truck drivers whose jobs regularly require them to leave their families, friends, and homes to travel hundreds of miles to deliver the products that we buy. The most recent statistics available, from 2012, show that more than 1.7 million people work as heavy and tractor-trailer truck drivers in the United States. Most of these drivers operate long-haul trucks transporting goods, often across several states. In 2012, 695 heavy and tractor-trailer drivers died in work-related motor vehicle crashes.
To gather data needed by private- and public-sector partners to help keep truck drivers safe on long hauls, the National Institute for Occupational Safety and Health (NIOSH) conducted personal interviews with 1,265 long-haul truck drivers at 32 truck stops across the United States. The drivers answered questions about their experiences with crashes, injuries from crashes, non-crash injuries, and moving violations; their work environments; driving behaviors; training; and job satisfaction and frustration. NIOSH reported these findings from the drivers’ answers:
- 73% of the drivers perceived their delivery deadlines as unrealistically tight, which could increase likelihood of unsafe actions such as speeding, violating driving-hour regulations, and driving despite fatigue, bad weather, or heavy traffic.
- 35% reported at least one crash in their career.
- 38% reported receiving inadequate training at the beginning of their careers.
In other findings, a small number of drivers reported often engaging in unsafe actions, including speeding. Similarly, a small number reported receiving two or more moving violation tickets, an indication of unsafe actions. A small percentage had a non-crash work-related injury involving days away from work in the previous 12 months, but most did not report these injuries to their employer. Overall, the investigators view the survey results as highlighting the need for research and interventions to keep truckers and, as an added benefit, other drivers, on the road safe.
Conducted from October through December 2010, the survey included questions developed with input from unions, employer and operator organizations, and other partners, including the American Trucking Association, the Owner Operator Independent Drivers Association, and the Federal Motor Carrier Safety Administration.
To read the article, go to NIOSH National Survey of Long-Haul Truck Drivers: Injury and Safety. This article is part of a larger survey that also addressed truck driver health.
For additional articles, visit National Survey of U.S. Long-Haul Truck Driver Health and Injury: Health Behaviors and Obesity and Other Risk Factors: The National Survey of U.S. Long-Haul Truck Driver Health and Injury.
Respirator Disinfection and Reuse
Researchers at the National Institute for Occupational Safety and Health (NIOSH) are studying ultraviolet (UV) energy as a way to disinfect disposable respirators so that healthcare providers could reuse them during emergency situations, if they were in short supply. At certain doses, UV energy can inactivate or kill bacteria, viruses, and other germs so that they cannot cause disease. During an epidemic, respirator demand could be between 1.7 billion and 3.5 billion, according to a recent peer-reviewed article.
The researchers take coupons (large pieces punched out from actual respirators) and mount them in holders to maintain their size and shape, assuring all samples are the same. The coupons are then placed in a calm air chamber where they are exposed to an aerosolized (highly resistant) bacterial spore. The researchers then split the coupons into two groups: controls that are not UV exposed and those that will be UV exposed. The coupons that will be exposed are put in a UV exposure chamber where they receive well-controlled doses of UV energy. All coupons are then placed in individual tubes with liquid and shaken to collect the spores. The liquids are spread on a culture plate for the spores to grow, the spores are counted, and comparisons are made between the controls and the coupons exposed to UV to understand the effects of UV exposures on inactivation of the spores. Results of this process will show if respirator disinfection via the UV exposure is effective and if respirators can withstand UV exposures before noticeable effects on filtering efficiency, strength, and strap performance occur.
Applying UV Energy to Disinfecting Ambulances
In a related study, NIOSH researchers are studying UV energy’s ability to disinfect ambulances quickly. Currently, the main way to clean surfaces is to use approved disinfectants to wipe them, which can be difficult and time-consuming, particularly during the pressures of an ongoing disease outbreak.
In one ambulance studied, the researchers built a portable UV-disinfection system that can be shared in several other ambulances. In a second ambulance, they installed a permanent UV-disinfection system that workers could operate when the ambulance is empty or when driving. Germ tests showed that both systems disinfect surfaces reasonably quickly. Future research includes further testing to see how well the UV systems work and what their limitations might be. Researchers are also developing a programmable UV robot that they could more easily tailor to fit different ambulance models.
- Page last reviewed: November 24, 2015
- Page last updated: November 24, 2015
- Content source:
- National Institute for Occupational Safety and Health (NIOSH) Office of the Director