Washed Cotton in The 1978 OSHA Cotton Dust Standard
August 1995
DHHS (NIOSH) Publication Number 95-113
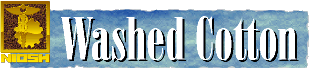
Current Intelligence Bulletin 56
Appendix
Steps in Modern Batch Kier Washing Processes
The processes common to most modern commercial batch kier washing operations are described in general terms in the following paragraphs.
Step 1. Mechanical Opening and Cleaning
Cotton in compressed form is taken from bales and is placed in opening hoppers where it is fed between lattice aprons that contain sharp, large- diameter spikes to begin the process of breaking up the batt of cotton into tufts to facilitate further processing and removal of trash. After this initial opening, the cotton typically passes through one or two additional stages of opening and cleaning in preparation for washing. The first mechanical cleaner that is almost always used is a "step" cleaner that uses air to convey the cotton through a series of rotating, spiked cylinders to remove extraneous material (mostly plant trash). The beating action of the rotating spikes loosens the heavier trash particles from the lint, and the particles then fall from the air stream to the waste chambers. Often a second stage of opening and cleaning is used to further open the cotton stock and remove small trash particles. Machines used in this second stage usually employ rotating cylinders containing saw teeth. This is a very vigorous mechanical treatment that can damage fibers and adversely affect cotton processing quality. Consequently, this second stage of cleaning is usually used only when the finished washed cotton must pass the USP ash test. Thus, mechanical processing is used to remove physical impurities from the cotton and to produce small fiber tufts (1 to 3g) to provide for effective wetting and packing in the cakemaking step. In the two effective batch kier washing trials described in the body of this report, mechanical opening and cleaning were accomplished by use of a spiked opener and a step cleaner in the first trial [Perkins and Berni 1991] and by use of a spiked opener, a step cleaner, and a fine-cylinder cleaner in the second trial [Perkins and Olenchock 1995].
Step 2. Prewetting and Cakemaking
The small cotton tufts produced in the mechanical process are conveyed by air to a cakemaking device designed to produce a doughnut-shaped cake of cotton that is thoroughly wet and packed to controlled, uniform density. This is accomplished by spraying the incoming tufts with a warm solution of water plus a wetting agent as they fall into the cylindrical container of the cakemaker. The spray is directed so that solution that does not contact the cotton tufts falls into the container. The entire container rotates slowly, and a mechanical tramper packs the wet cotton to produce the uniform cake. The amount of wetting solution used and the packing intensity are carefully controlled to produce the desired cake density. The prewetting during cakemaking is a key step to ensure that the cotton will be thoroughly wet even in the first cycle in the kier wash step.
Step 3. Kier Washing and Rinsing
Three cakes of prewet cotton are added to a kier for washing. The individual integrity of the cakes is maintained by separation of the cakes with perforated stainless steel discs. Kier capacity varies from about 1,500 to 2,300 lb of cotton (dry weight). In the washing cycle, washing solution (water plus wetting agent) at the selected temperature is pumped through the cakes from the inside to the outside. The solution passes through the cakes in the kier to an outside expansion tank and then back through the cakes. The solution is then dumped into the sewer; a new, clean washing solution is added to the kier; and the process is repeated. The number of cycles of new washing solution and the cycle times depend on preselected washing conditions. After the required number of cycles with washing solution, clean water is used in a number of rinsing cycles to complete the removal of dissolved impurities and residual wetting agent. The fact that the wash and rinse solutions in each cycle are not reused results in maximum removal of dissolved impurities.
Step 4. Centrifugation
After rinsing, the cakes are removed from the kier and are centrifuged individually to reduce moisture content to about 50% (wet basis).
Step 5. Drying and Baling
The centrifuged cakes are broken up mechanically by a series of large-diameter spiked cylinders to produce a batt of cotton that then passes through a tunnel dryer. Heated air, usually in the temperature range of 125° to 150° C, is forced through the batt to accomplish drying to a preselected moisture content range, usually about 4% to 8%. After drying, the cotton is fed through a mechanical opener-cleaner to remove residual trash and to break up the dried batt of cotton for feeding to the bale press for compression and packaging. The finished, covered bales are weighed (average weight is about 500 lb) and tagged for identification as appropriate.
Potential Markets for Mildly Washed Cotton
Most of the currently envisioned potential end uses for 100% mildly washed cotton would probably involve novelty or niche markets but could potentially result in significant expansions into other markets. Advantages of mildly washing raw cotton extend beyond the potential for achieving compliance with OSHA exposure limits and protecting worker health. Specifically, while washing generally adversely affects cotton textile processing, mild washing may actually enhance the textile processing characteristics of some cotton (e.g., "sticky" cotton). It may also enable value-added special effects (e.g., differential dyeing characteristics for novelty yarns and improved quality of rotor-spun yarns). Potential use of mildly washed cotton in cotton and cotton-synthetic yarns containing only a small proportion of washed cotton would also be possible, but (as with any potential application of washed cotton) washing-associated costs and benefits will need to be considered on a case-by-case basis and may prove limiting.
Acute and Chronic Respiratory Effects of Cotton Dust
Chronic Respiratory Effect: Relationship to Acute Effect
The progression from an initial acute and reversible pulmonary effect to an eventual chronic and irreversible effect has been implicit in clinical descriptions of byssinosis and is a key underlying assumption of the OSHA cotton dust standard [43 Fed. Reg. 27351 (1978), 50 Fed. Reg. 51120 (1985)]. Yet as recently as 1986, it was emphasized that "a clear relationship between acute and chronic respiratory disease in cotton workers has not been established, and a prospective study is necessary to investigate this relationship" [ASPH 1986]. Such a study has recently been completed, and the results of this large prospective study of 1,664 U.S. cotton textile workers indicate a significant association between acute (across-shift) decline and longitudinal decline in lung function [Glindmeyer et al. 1994]. This is an extremely important observation with respect to results of the cotton washing studies because it supports the contention that the acute respiratory response measured in washed cotton studies is a valid predictor for the chronic hazard potential of cotton dust.
Acute Respiratory Effect: Relationship to Endotoxin
The search for a measure of the acute and chronic respiratory toxicity of cotton dust more specific than airborne gravimetric dust concentration has increasingly centered on bacterial endotoxin. Several studies have documented an association between endotoxin concentration and respiratory symptoms of exposed individuals; even more clearly, they have demonstrated a relationship between endotoxin and across-shift FEV1 decrement among humans exposed to cotton dust [Rylander and Haglind 1983, 1986; Castellan et al. 1984, 1987; Rylander et al. 1985]. The most definitive findings were reported by NIOSH investigators, who observed a clear exposure- response relationship between mean FEV1 response and endotoxin concentration (P<0.00001), though dust concentrations from the same set of exposures were not correlated with FEV1 change (P=0.43) [Castellan et al. 1987]. All 51 exposures above 50 ng/m3 endotoxin resulted in statistically significant mean FEV1 responses, whereas none of the eight exposures below 10 ng/m3 endotoxin did so, and a linear regression model based on the observed data predicted a "threshold" at approximately 9 ng/m3 for the FEV1 response [Castellan et al. 1987]. (As discussed above, because of differences in endotoxin extraction and assay methods between laboratories, results of endotoxin measurements from other laboratories may not be directly comparable to this "threshold.")
Although these experimental results do not by themselves prove that endotoxin is causal, the very clear exposure-response relationship between airborne endotoxin concentration and acute decline in FEV1 is very unlikely to have been observed unless a predominant causal role is played by endotoxin or some other cotton dust component (or components) in a concentration that closely parallels that of endotoxin. On the basis of this exposure-response relationship, NIOSH concluded in a letter to OSHA that although "it is not now possible to offer a definitive opinion regarding chronic health effects, ... airborne endotoxin is a valid surrogate for the level of acute respiratory hazards of cotton dust" [Niemeier 1990].
Chronic Respiratory Effect: Relationship to Endotoxin
The demonstrated relationship between acute and chronic respiratory responses to cotton dust [Glindmeyer et al. 1994] and the demonstrated relationship of acute respiratory response and endotoxin [Rylander and Haglind 1983, 1986; Castellan et al. 1984, 1987; Rylander et al. 1985] together offer a basis for accepting the endotoxin measurements made during the washing studies as a surrogate for the chronic respiratory hazard of cotton dust, as well as for the acute respiratory hazard. Additional evidence for considering endotoxin inhalation a risk factor for chronic lung effects is provided by other studies that have demonstrated quantitative relationships between chronic respiratory effects and exposure to airborne, endotoxin-contaminated organic dust. These studies have involved textile mill workers [Kennedy et al. 1987; Sigsgaard et al. 1992], Dutch animal feed mill workers [Smid et al. 1992], and workers in the swine confinement industry [Zejda et al. 1994], an occupational setting in which an exposure-effect relationship of airborne endotoxin exposure with across-shift FEV1 decrement has been reported [Donham et al. 1988; Heederick et al. 1991].
- Page last reviewed: June 6, 2014
- Page last updated: June 6, 2014
- Content source:
- National Institute for Occupational Safety and Health Education and Information Division