SILICA
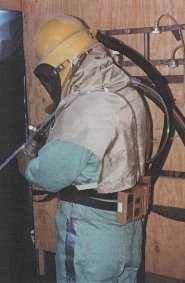
Evaluation of Substitute Materials for Silica Sand in Abrasive Blasting
Contract No. 200-95-2946
A portable containment system that was constructed on a barge at the Consolidated Coal Company Shipyard in Elizabeth, Pennsylvania. Throughout all abrasive trials, variability of the blast cleaning environment was controlled by moving the same blast containment and abrasive blast cleaning equipment to each new test area. Phase 2, Appendix E contains 20 photographs of the blast cleaning facility and the equipment utilized for this study. Click on the links below to view the photographs.
- Initial condition of coal barge
- Containment and equipment staging
- Duct work positioning for ventilation of containment to dust collector
- Monitoring station outside of containment structure
- IH technician measuring air flow inside containment
- Positioning of filter media on operator
- Properly protected operator prior to blast cleaning
- Operator inside containment blast cleaning. Note personal sampling pumps at belt.
- Blast cleaning operations
- Blast cleaned section of coal barge after movement of containment
- Verification of blast cleanliness on a flat area using SSPC VIS 1-89
- Verification of blast cleanliness on pitted area using SSPC VIS 1-89
- Post-blast surfaces cleaned using copper slag
- Post-blast surfaces cleaned using nickel slag
- Post-blast surfaces cleaned using garnet
- Post-blast surfaces cleaned using coal slag
- Post-blast surfaces cleaned using silica sand with dust suppressant
- Post-blast surfaces cleaned using flint silica sand
- Post-blast surfaces cleaned using staurolite sand
- Post-blast surfaces cleaned using steel grit
- Page last reviewed: March 22, 2012
- Page last updated: March 22, 2012
- Content source:
- National Institute for Occupational Safety and Health Respiratory Health Division (RHD)