Engineering Controls Program
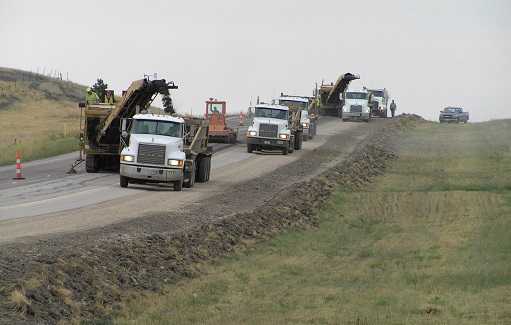
Cold-milling, which uses a toothed, rotating cutter drum to grind and remove the pavement to be recycled, is primarily used to remove surface deterioration on road surfaces. Photo credit: NIOSH
Program Impact
NIOSH is strongly committed to program evaluation as a way to maximize its contributions to improved occupational safety and health. Regular review of program activities, outputs, and outcomes is essential to demonstrating program performance. The Engineering Controls Core and Specialty Program conducts reviews and shares program impact in a variety of ways.
Program Performance One-pager
Program Performance One-Pagers (PPOPs) are a snapshot of NIOSH programs’ priorities, strategies used to make progress towards priorities, recent accomplishments, and upcoming work.
Engineering Controls Program Performance One-pager
Program Impact Highlights
These one-page fact sheets describe work by the Engineering Controls Program.
- Page last reviewed: June 20, 2017
- Page last updated: September 7, 2017
- Content source:
- National Institute for Occupational Safety and Health Division of Applied Research and Technology