Preventing Silicosis
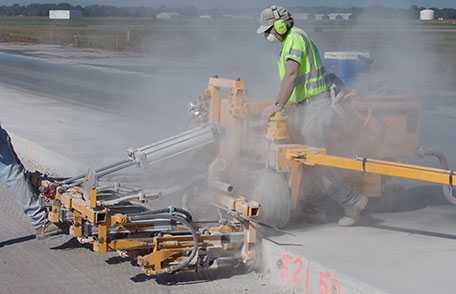
Learn more about workplace solutions for controlling exposures to Respirable Crystalline Silica in construction and hydraulic fracturing. Save lives and prevent new cases of silicosis, a severe lung disease. Understand the occupational exposure limits to keep workers safe from breathing hazardous silica dust.
Approximately 2.3 million workers are exposed to respirable crystalline silica (RCS) in the workplace, including 2 million workers in construction and 300,000 workers in general industry, maritime and hydraulic fracturing. As early as 1974, NIOSH researchers had proposed a recommended exposure limit (REL) of 50 micrograms per cubic meter (50 µg/m3) for inhalation of dust containing RCS, as a time-weighted average for up to a 10-hour workday as part of a 40-hour workweek. NIOSH research into engineering control methods to reduce RCS exposures in the workplace are ongoing, helping employers to safeguard the health of their employees.
What is Silica and Silicosis?
Silica, or silicon dioxide (SiO2) is a mineral that occurs naturally in crystalline or non-crystalline form. The most abundant crystalline form is α-quartz, which is the most common mineral on earth’s continents. It is found in sand, sandstone, shale and granite. Drilling, crushing, cutting, chipping, breaking, sawing or polishing materials containing crystalline silica can create a large amount of respirable dust. These dust particles, mostly 10 microns in size and smaller, are too small to see, but can penetrate to the deepest part of the human lung when inhaled. Chronic inhalation of such respirable crystalline silica (RCS) dust can lead to severe lung disease, such as silicosis or lung cancer. Having silicosis can, in turn, increase the risk of developing tuberculosis. RCS exposure has also been linked to kidney and auto-immune diseases.
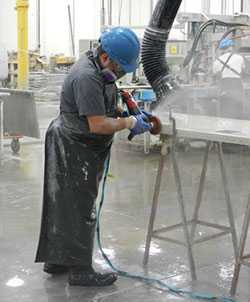
A worker wet-grinds a stone countertop using local exhaust ventilation by means of a drop-down arm from a ceiling-mounted dust collector.
What Jobs are at Risk for Increased Exposure to RCS dust?
There are risks for inhalation of RCS in many jobs in many different industries. Some examples are:
- Construction
- Sandblasting
- Jack hammering
- Rock drilling, cutting, chipping or polishing
- Brick or tile cutting and sawing
- Concrete drilling, sawing, grinding and polishing
- Tunneling
- Demolition
- Asphalt milling
- Tuckpointing
- Stone countertop fabrication
- Diatomaceous earth processing
- Pottery production
- Foundries
- Work on linings of rotary kilns and cupola furnaces
- Mining
- Hydraulic fracturing
What is the New Occupational Exposure Limit?
The OSHA Final Rule for Occupational Exposure to Respirable Crystalline Silica, including the standard for construction, 29 CFR 1926.1153, and for general industry and maritime, 29 CFR 1910.1053, took effect on June 23, 2016. The OSHA final rule reduces the permissible exposure limit (PEL) for respirable crystalline silica (RCS) to 50 micrograms per cubic meter of air, matching the NIOSH REL. Engineering controls are now also a part of the new rule helping to reduce worker exposure. Depending on the industry, implementation dates for the new rule range from 2017 to 2021. The new occupational exposure limit is expected to save over 600 lives and prevent more than 900 new cases of silicosis annually.
How Can Employers Control Exposures to RCS dust?
Controlling exposures to occupational hazards is the fundamental method of protecting workers. Traditionally, a hierarchy of controls has been used as a means of determining how best to implement feasible and effective controls.
One application of the hierarchy of controls to RCS exposure can be summarized as follows:
- Elimination – eliminate job tasks with risk of exposure
- Substitution – substitute non-crystalline-silica materials for crystalline silica materials
- Engineering Controls – use a control such as local exhaust ventilation or water spray to reduce concentrations of RCS in the air
- Administrative Controls – limit time spent working with RCS, and/or limit worker access to areas of high RCS concentration
- Personal Protective Equipment – wear respirators when working with RCS
The idea behind this hierarchy is that the control methods at the top of the list are potentially more effective, protective, and economical (in the long run) than those at the bottom. Following the hierarchy normally leads to the implementation of inherently safer systems, ones where the risk of illness or injury has been substantially reduced.
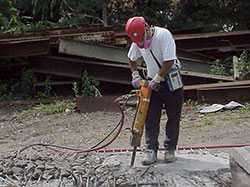
Jackhammering with a water spray control that reduces dust.
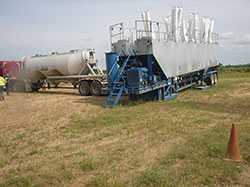
Filter bags of the NIOSH mini-baghouse retrofit assembly (NMBRA) have been installed on the thief hatches on top of this sand mover, used for hydraulic fracturing.
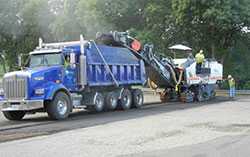
Exposures of asphalt milling machine operators to RCS have been reduced by implementation of local exhaust ventilation.
RCS Exposure Control Research
CDC’s National Institute for Occupational Safety and Health (NIOSH) has been studying ways to protect workers from occupational exposure to RCS for over 40 years. Laboratory research has tested the effectiveness of local exhaust ventilation in controlling RCS exposure during cutting and sawing of construction materials. In field studies, engineering controls have been tested under real-world conditions to determine their effectiveness in protecting worker health.
Engineering controls for RCS dust are becoming increasingly available for a range of tools and equipment. Engineering controls are often based on the use of a collector such as a shroud, combined with an industrial vacuum for local exhaust ventilation. Such arrangements are commercially available for jackhammers, drills, chisels, concrete breakers, saws, sanders, concrete floor polishers, hand grinders and asphalt milling machines
Local exhaust ventilation systems using baghouse controls are available for RCS released from sand mover equipment during hydraulic fracturing. Wet methods to control RCS are commercially available for drills, saws, grinders and polishers. Wet RCS controls are not commercially available for jackhammers, but instructions for making your own water spray engineering control can be found on the website for CPWR, The Center for Construction Research and Training.
Continued Investigation on the Best Engineering Controls
NIOSH researchers continue to develop and investigate the best engineering controls for RCS. Recent research includes RCS control during concrete floor polishing, stone countertop fabrication, hydraulic fracturing (or “fracking”), asphalt milling, cutting of fiber cement siding, tuckpointing and concrete dowel drilling.
- Most walk-behind concrete floor polishers[1.26 MB] come equipped with local exhaust ventilation or water suppression systems. NIOSH research has revealed that some equipment is more efficient than others at RCS control, and has helped to point the way to better worker protection.
- RCS exposure during stone countertop fabrication and installation[4.62 MB] is an emerging issue. NIOSH researchers are at the forefront in evaluating the efficacy of engineering controls for protecting workers in this industry. Field studies have been performed in several workplaces to measure the effectiveness of wet grinding and polishing in reducing worker exposures. Data collected to date show that existing engineering controls may not be sufficiently protective of workers’ health. These investigations are ongoing.
- During hydraulic fracturing, more than a million pounds of sand may be delivered, handled and pumped deep underground to retrieve oil and gas. Dust from this “frac sand” contains[2.02 MB] large amounts of RCS. With the help of industry partners, NIOSH researchers have developed and evaluated an engineering control for “frac sand” dust released from thief hatches on sand moving equipment, the major source of RCS exposure to workers. This control, called the NIOSH mini-baghouse retrofit assembly (NMBRA)[3.12 MB] is an inexpensive, portable system with no moving parts, which can be installed on a sand mover in the field. The NMBRA has shown excellent efficiency in filtering RCS from the air, and is currently being tested in the field for its long-term performance characteristics.
- NIOSH research identified cutting of fiber cement siding[561 KB] as a source of worker exposure to RCS. Employing a simple and low-cost local exhaust ventilation on dust-collecting circular saws has been proven effective in reducing worker exposure.
- Workers performing tuckpointing experience some of the highest measured construction exposures to RCS. Clouds of mortar dust also make it difficult for workers to see the work surface. Application of local exhaust ventilation[303 KB] with tuckpointing grinders can improve both the health and the safety of these workers. Recently, NIOSH researchers began investigating dust controls for RCS exposures from tools other than grinders that can be used to remove mortar.
- Local exhaust ventilation has also been used in concrete dowel drilling[947 KB] operations. NIOSH research showed that some of the highest RCS exposures to workers doing these tasks came from unexpected sources, such as from RCS that had accumulated on the worker’s clothing, or from cleaning of the dust collection equipment.
- An area in which NIOSH research has been very successful is in the asphalt milling industry. NIOSH participated in a Silica/Asphalt Milling Machine Partnership that was coordinated by the National Asphalt Pavement Association (NAPA) and included all U.S. and foreign manufacturers of heavy construction equipment that sold pavement-milling machines to the U.S. market. The partnership included many stakeholders from labor, industry, and government who worked together to reduce silica exposures on asphalt milling machines. As a result of the collaborative research, all manufacturers of half-lane and larger cold milling machines implemented dust controls that include local exhaust ventilation as a control for RCS exposures by January 1, 2017. A NIOSH best practices document, published in March, 2015, highlights the most successful engineering controls to reduce RCS exposures on asphalt pavement milling machines.
More Information
More Information
- Silica
- Engineering Controls for Silica in Construction
- NIOSH Workplace Solutions
- Construction Safety and Health
- Hydraulic Fracturing[2.02 MB]
- Engineering and Physical Hazards Reports
- Occupational Safety and Health Administration (OSHA), Silica
- OSHA Fact Sheet, OSHA’s Crystalline Silica Rule: Construction[182 KB]
- CPWR – The Center for Construction Research and Training
- Working Safely with Silica
- Page last reviewed: March 20, 2017
- Page last updated: March 20, 2017
- Content source:
- National Institute for Occupational Safety and Health
- Page maintained by: Office of the Associate Director for Communication, Digital Media Branch, Division of Public Affairs