Heat-related Illness
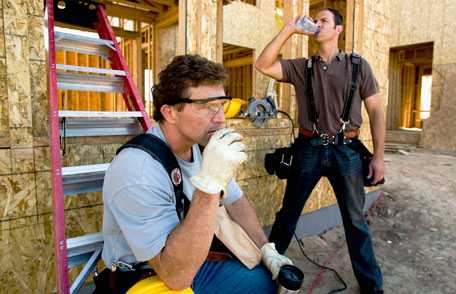
Heat stress can affect many outdoor and indoor workers. To prevent heat-related illnesses and injuries on the job, an in-depth heat-related illness prevention program should be developed and utilized.
Occupational exposure to heat can result in illnesses, injuries, reduced productivity, and death. In 2016, NIOSH published the Criteria for a Recommended Standard: Occupational Exposure to Heat and Hot Environments, which provides detailed guidance for preventing heat-related illnesses and injuries. Some of this guidance has been briefly summarized below, and should be considered when developing a heat-related illness prevention program.
Control of Heat Stress
Employers should reduce workplace heat stress by implementing engineering and work practice controls.
Engineering controls might include those that:
- Increase air velocity (if air temperature is below 95°F) .
- Use reflective or heat-absorbing shielding or barriers.
- Reduce steam leaks, wet floors, or humidity.
Work practice recommendations include the following:
- Limit time in the heat and/or increase recovery time spent in a cool environment.
- Reduce the metabolic demands of the job.
- Increase the number of workers per task.
- Implement a buddy system where workers observe each other for signs of heat intolerance.
- Require workers to conduct self-monitoring and create a work group (i.e., workers, a qualified healthcare provider, and a safety manager) to make decisions on self-monitoring options and standard operating procedures.
- Implement a heat alert program whenever the weather service forecasts that a heat wave is likely to occur.
Training
Train workers before hot work begins, and tailor the training to cover worksite-specific conditions.
Employers should provide a heat stress training program for all workers and supervisors about the following:
- Recognition of the signs and symptoms of heat-related illnesses and administration of first aid.
- Causes of heat-related illnesses and the procedures that will minimize the risk, such as drinking enough water and monitoring the color and amount of urine output.
- Proper care and use of heat-protective clothing and equipment and the added heat load caused by exertion, clothing, and personal protective equipment.
- Effects of nonoccupational factors (drugs, alcohol, obesity, etc.) on tolerance to occupational heat stress.
- The importance of acclimatization.
- The importance of immediately reporting to the supervisor any symptoms or signs of heat-related illnesses in themselves or in coworkers.
- Procedures for responding to symptoms of possible heat-related illnesses and for contacting emergency medical services.
In addition, supervisors should be trained on the following:
- How to implement appropriate acclimatization.
- What procedures to follow when a worker has symptoms consistent with heat-related illnesses, including emergency response procedures.
- How to monitor weather reports and respond to hot weather advisories. (Download Heat Safety Tool App)
- How to monitor and encourage adequate fluid intake and rest breaks.
Acclimatization
Workers become acclimatized to heat when they gradually work for longer periods in a hot environment. Benefits of acclimatization include physiological adaptations, such as increased sweating efficiency and stabilization of the circulation.
Employers must make certain that workers acclimatize to heat by gradually increasing the time they work in hot environments:
- New workers, and workers returning from an absence of more than a week, should follow a schedule to gradually acclimatize to the hot conditions. Begin with 20% of the usual duration of work in the hot environment on the first day, increasing gradually by no more than 20% each day that follows.
- Experienced workers should begin on the first day of work in excessive heat with 50% of the usual duration of work. They should work 60% on the second day, 80% on the third day, and 100% on the fourth day.
- Depending on individual or environmental factors, it might take up to 14 days or longer for a worker to become fully acclimatized.
Hydration
Employers should provide the means for appropriate hydration of workers.
- Water should be potable, <15°C (59°F), and made accessible near the work area.
- Individual, not communal, drinking cups should be provided.
- Encourage workers to hydrate themselves.
Workers should drink an appropriate amount to stay hydrated.
- If in the heat <2 hours and involved in moderate work activities, drink 1 cup (8 oz.) of water every 15–20 minutes.
- During prolonged sweating lasting several hours, drink sports drinks containing balanced electrolytes.
- Avoid alcohol and drinks with high caffeine or sugar.
- Generally, fluid intake should not exceed 6 cups per hour.
Rest Breaks
Employers should ensure and encourage workers to take appropriate rest breaks to cool down and hydrate.
- Permit rest and water breaks when a worker feels heat discomfort.
- Modify work/rest periods to give the body a chance to get rid of excess heat.
- Assign new and unacclimatized workers lighter work and longer, more frequent rest periods.
- Shorten work periods and increase rest periods:
- As temperature, humidity, and sunshine increase.
- When there is no air movement (see above engineering controls for limits to fan usage).
- If protective clothing or equipment is worn.
- For heavier work.
While these basic recommendations can be applied to many different workplaces, if heat stress is a hazard at your workplace, consult with a safety and health professional, and review the full recommendations provided in the NIOSH Criteria for a Recommended Standard: Occupational Exposure to Heat and Hot Environments.
More Information
- NIOSH Heat Stress
- NIOSH Criteria for a Recommended Standard: Occupational Exposure to Heat and Hot Environments
- Download Heat Safety Tool App
- NIOSH Infographic: Protect Your Workers from Heat Stress
- NIOSH Preventing Heat-related Illness or Death of Outdoor Workers </a
- OSHA-NIOSH INFOSHEET: Protecting Workers from Heat Illness
- CDC Extreme Heat
- Page last reviewed: June 19, 2017
- Page last updated: June 19, 2017
- Content source:
- National Institute for Occupational Safety and Health
- Page maintained by: Office of the Associate Director for Communication, Digital Media Branch, Division of Public Affairs