Control of Health and Safety Hazards in Commercial Drycleaners: Chemical Exposures, Fire Hazards, and Ergonomic Risk Factors
December 1997
DHHS (NIOSH) Publication Number 97-150
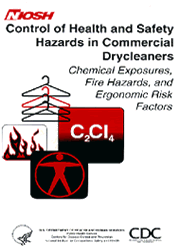
DISCLAIMER: Mention of company names or products does not constitute endorsement by the Centers for Disease Control and Prevention (CDC).
Foreword
The Occupational Safety and Health Act of 1970 (Public Law 91-596) assures as far as possible every working man and woman in the Nation safe and healthful working conditions. The act charges the National Institute for Occupational Safety and Health (NIOSH) with recommending occupational safety and health standards and describing exposures that are safe for various periods of employment, including but not limited to the exposures at which no worker will suffer diminished health, functional capacity, or life expectancy as a result of his or her work experience.
This document represents the efforts of NIOSH researchers who have worked in collaboration with industry, labor, and other governmental organizations to protect the health of workers in the commercial drycleaning industry. Drycleaning is predominantly a small business industry with a substantial percentage of minority workers who are exposed to a wide array of hazards. The purpose of the document is to present the research findings and provide guidance to regulatory agencies and owners of drycleaning shops regarding hazard control measures. Control technologies and methods are presented for reducing occupational exposures to perchloroethylene (PERC), as well as for controlling exposures to spotting chemicals, fire, and ergonomic hazards. It is not intended to provide total information in all areas of safety and health.
Significant attention has been paid to the effects of perchloroethylene on the environment while the effects of perchloroethylene on workers have often been overshadowed. Health effects associated with exposure to perchloroethylene include depression of the central nervous system; damage to the liver and kidneys; and impaired memory, confusion, and dizziness. There is increasing evidence of human carcinogenicity. The uncontrolled use of PERC has the potential to cause widespread harm to the health of the workers, the people living near drycleaning shops, the general public, and the global environment.
This document is a positive contribution to worker health and safety. It is an essential reference on health and safety in the drycleaning industry, which I strongly recommend to all concerned. It is my hope that this document will assist in providing a safe and healthful working environment by describing the most effective control technologies and procedures.
Linda Rosenstock, M.D., M.P.H.
Director, National Institute for
Occupational Safety and Health
Centers for Disease Control and Prevention
Abstract
This report investigates control methods and technologies used in the drycleaning industry for reducing occupational exposures to tetrachloroethylene, also known as "perchloroethylene" (PERC). It also examines drycleaning machines that use petroleum-based solvents. It addresses methods for controlling exposures to spotting chemicals, fire, and ergonomic hazards in commercial drycleaning shops. Data were gathered during ten field surveys at drycleaning shops across the U.S. and through a World Health Organization (WHO) fellowship in Europe.
The study by the National Institute for Occupational Safety and Health (NIOSH) looked at various categories of drycleaning equipment, such as transfer and dry-to-dry, vented and nonvented, and modern machines equipped with various vapor recovery devices. The evaluated shops maintained full-shift, time-weighted average (TWA) exposures to PERC below 25 ppm; however, peak exposures during machine loading and unloading were frequently near 2,000 ppm. Most operator exposures could have been further reduced during machine loading and unloading by additional control measures: the use of another cleaning media, such as petroleum-based solvents or water; the isolation of the drycleaning process through "satellite shops"; a switch to state-of-the-art drycleaning machines equipped with both refrigerated condensers and carbon absorbers; and more effective use of local and general ventilation.
Inhalation of spotting chemicals was not a significant hazard; however, isolation of this process would avoid unnecessary exposure to other workers. A number of recommendations are given to further reduce spotting chemical exposures. Ergonomic hazards usually involve repetitive motions and awkward postures. In drycleaning, these problems primarily occur at the pressing stations and can be controlled. Redesigned, adjustable workstations for pressing will decrease the awkward postures and excessive reaching. Frequent breaks and worker rotation will reduce worker repetition.
Fire hazards can be reduced by a two-pronged approach. The greatest risk of fire and explosion in drycleaning shops comes from petroleum-based solvents used in some drycleaning machines. First, new petroleum-based solvents and machines, both of which are inherently safer than those traditionally utilized, are currently available and could serve as an alternative to PERC in some U.S. shops. Second, all shops should comply with appropriate National Fire Protection Association/Building Officials & Code Administration (NFPA)/(BOCA) codes to reduce the risk of fire not only in the drycleaning area but also throughout the entire shop.
Preface
Under the authority of the Occupational Safety and Health Act of 1970 (Public Law 91-596), the National Institute for Occupational Safety and Health (NIOSH) conducts research to prevent occupational safety and health problems through the application of control technology in the workplace. The goal of this program is to assist in preventing hazardous exposures to workers and to document successful approaches and control measures.
This report evaluates control methods and systems for reducing perchloroethylene (PERC) exposures in commercial drycleaning shops throughout the United States. During ten field surveys, NIOSH researchers inspected various categories of drycleaning equipment, such as transfer and dry-to-dry, vented and nonvented, and modern machines equipped with various vapor recovery devices. This study also addressed control of health and safety hazards related to petroleum-based drycleaning solvents, control of exposure to spotting chemicals, and control of ergonomic risk factors.
Additionally, NIOSH researchers received a World Health Organization (WHO) fellowship to study methods and controls to reduce occupational exposure to and environmental emissions of PERC in Europe. This study involved gathering information concerning drycleaning regulations, equipment, exposure levels, work practices, and alternatives to PERC in Europe. Important research into new technologies for reducing emissions and exposure to PERC has been conducted in Europe. These technologies include improved design and engineering controls for PERC drycleaning machines and alternative technologies, such as cleaning with petroleum-based solvents or aqueous-based cleaning methods. The European visit enabled NIOSH researchers to learn about differences in the drycleaning processes between the U.S. and Europe. Findings from this fellowship are also included in this report.
Information gathered during the study was supplemented by a literature review. This report provides a reference for anyone interested in protecting drycleaning workers from exposures to PERC, spotting chemicals, ergonomic risk factors, and fire hazards. Individual in-depth and walk-through survey reports, which include more detailed information on specific characteristics of each drycleaning shop and control systems studied, are available from the National Technical Information Service, Port Royal Road, Springfield, Virginia 22161.
Acknowledgements
Manuscript Authored by: Gary S. Earnest, M.S., P.E., C.S.P.
Amy Beasley Spencer
Stephen S. Smith, M.S.
William A. Heitbrink, Ph.D., C.I.H.
Ronald L. Mickelsen, M.S., P.E.
James D. McGlothlin, M.P.H., Ph.D, C.P.E.
Lynda M. Ewers, Ph.D.
Manuscript Prepared by:
Bernice L. Clark Robin F. Smith
Manuscript Edited by: Anne L. Votaw
Cover Prepared by: Anne M. Stirnkorb
Survey and Technical Assistance by:
Jim P. Agee
Paul A. Jensen, Ph.D., P.E., C.I.H.
Phillip A. Froehlich, M.S.
James H. Jones
Michael G. Gressel, M.S., C.S.P.
Ronald J. Kovein
Ronald M. Hall
Dennis M. O'Brien, Ph.D., P.E., C.I.H.
The authors would like to thank the following individuals and organizations for providing input to the study protocol: International Fabricare Institute, Fabritec International, Dryclean U.S.A., Boewe Passat Corporation, Union of Needle Trades Industrial and Textile Employees.
The authors would like to thank the following individuals and organizations for providing input and general assistance throughout the study: Boewe Passat Corporation, MultiTEX Corporation, Realstar Corporation, Union Corporation, Hohenstein Institute, Kruessler Corporation, The World Health Organization, U.S. Environmental Protection Agency, Michigan Department of Public Health.
The authors would like to express a special thanks to Mr. Max Zimmerman.
Introduction
Historically, drycleaning was performed by hand, using petroleum-based solvents that had dangerously low flash points.1 In fact, drycleaning is believed to have originated in France in 1825 when a worker in a dye and cleaning factory spilled lamp oil, a flammable petroleum-based solvent, on a soiled tablecloth.1 When the tablecloth dried, the spots were gone. The drycleaning industry first used turpentine and kerosene before moving to benzene and gasoline. All of these solvents had one major disadvantage: they were flammable and caused fires and explosions.2
Over time, better petroleum-based solvents were introduced, having higher flash points. In 1928, W.J. Stoddard, president of the U.S. National Institute of Drycleaning (now the International Fabricare Institute), introduced Stoddard Solvent, a nearly odorless, petroleum-based solvent, which gained widespread acceptance in the industry.1 Stoddard Solvent™, having a flashpoint of approximately 49°C (120°F), reduced the risk of fire and explosion, but did not eliminate it. Petroleum-based solvents eventually were restricted in urban areas because of their inherent fire hazard.
Near the turn of the century, chemists learned to synthesize chlorinated hydrocarbons and produce them in large quantities. Many of these nonflammable solvents came into use for drycleaning. Early on, carbon tetrachloride was the favorite chlorinated hydrocarbon for drycleaning; but because of its toxicity and aggressiveness to metals, textiles, and dyes, it was gradually replaced in the 1940s and 1950s by trichloroethylene and tetrachloroethylene.2 Tetrachloroethylene is also commonly known as "perchloroethylene" (PERC).
In the 1960s, CFC 113, a chlorofluorocarbon solvent, was used in drycleaning, but never reached a significant market share. Because of its potential to deplete ozone and cause global warming, it is now banned in the U.S. and in most other countries under the Montreal Protocol. Today, approximately 90% of U.S. drycleaners use PERC in their machines.3 PERC (C2Cl4) is a colorless, clear, heavy liquid with an ethereal odor. The odor threshold is approximately 30parts per million (ppm).4 However, because significant adverse health effects have been discovered, many countries have imposed stringent regulations for the control of PERC exposures and emissions.
The Need For Controls
Background
In the late 1970s and early 1980s, the National Institute for Occupational Safety and Health (NIOSH) sponsored an engineering control technology study in the drycleaning industry.5 Among other health hazards, this evaluation found high exposures to the drycleaning solvent PERC. In 1988, the Occupational Safety and Health Administration (OSHA) Director of Federal-State Operations conducted a nationwide query of the OSHA State Consultation Programs to assess which small businesses were considered to be "high risk." The drycleaning industry was the second most mentioned small business, preceded only by autobody repair shops.6 In 1993, NIOSH researchers conducted a preliminary hazard analysis and based upon that analysis decided to evaluate control of PERC exposures, spotting chemical exposures, ergonomic risk factors, and fire hazards.
Significant changes involving equipment, processes, and work practices have occurred within the drycleaning industry since the earlier NIOSH study. These changes include alternative solvents and cleaning methods; a shift away from older drycleaning machines that require manual transfer of solvent-laden garments between washer and dryer to modern, closed-loop machines; and innovations in vapor recovery equipment and other technologies to reduce occupational exposures and environmental emissions. Many of these changes have been initiated by new epidemiologic, toxicologic, and environmental data for the primary solvent PERC. Nonetheless, many of the exposure problems identified during studies in the late 1970s and early 1980s still exist in the U.S. because traditional drycleaning machines are still being used. Many of the modern controls that have been developed are cost prohibitive for small shops, and some work practices are inadequate.
Profile of the U.S. Drycleaning Workforce
The Business America on Disc® CD-ROM7 file includes 48,087 drycleaners in the U.S. The distribution by number of employees is shown in Table 1. If the number of employees/shop is a reliable estimate, between 150,000 and 365,000 individuals work in drycleaning shops. Seventy percent (33,853) of shops employ one to four workers. Unlike the OSHA list of employees, which does not include nonsalaried owners, the Business America definition includes owners on site as employees since many of these firms are family operated. The U.S. Environmental Protection Agency (EPA) recently estimated that there were 30,000commercial drycleaning shops and approximately 244,000 employees. The National Occupational Exposure Survey8 (NOES) estimated that in 1982-83 there were over one-half million drycleaning shop employees in more than 40,000 plants potentially exposed to PERC.
Table 1: Quantity of U.S. Drycleaners and Number of Employees
Number of Employees | Number of Shops | Percentage of Total Shops | Minimum Total Employees | Maximum Total Employees |
---|---|---|---|---|
1-4 | 33,853 | 70 | 33,853 | 135,412 |
5-9 | 8,252 | 17 | 41,260 | 74,268 |
10-19 | 3,482 | 7 | 34,820 | 66,158 |
20-49 | 1,095 | 2 | 21,900 | 53,655 |
50-99 | 175 | 0.3 | 8,750 | 17,325 |
100-249 | 62 | 0.1 | 6,200 | 15,438 |
250-499 | 6 | 0.01 | 1,500 | 2,994 |
500-999 | 1 | 0.01 | 500 | 999 |
UNKNOWN | 1,161 | 2 | 1,161 | 1,161 |
TOTAL | 48,087 | 10 | 149,944 | 367,410 |
Potential Hazards
Perchloroethylene (PERC)
In the U.S. PERC is the most commonly used drycleaning solvent and is also occasionally used as a spotting agent. PERC can enter the human body through both respiratory and dermal exposure. Although nonflammable, if PERC is heated sufficiently, thermal decomposition will result in the formation of hydrogen chloride and phosgene gases. Symptoms associated with respiratory exposure include the following: depression of the central nervous system; damage to the liver and kidneys; impaired memory; confusion; dizziness; headache; drowsiness; and eye, nose, and throat irritation. Repeated dermal exposure may result in dry, scaly, and fissured dermatitis.9
Link Between PERC Exposure and Cancer.—The possible link between PERC exposure and cancer was first suspected through studies conducted by the National Cancer Institute (1977) and the National Toxicology Program (1986). A 1987 EPA study of PERC showed that, in addition to the numerous adverse health effects already known and outlined above, there was evidence of carcinogenicity. In December 1991, the EPA began regulating PERC as a hazardous air pollutant under Section 112 of the Clean Air Act.10 Other studies, including one at NIOSH, showed an elevated risk of urinary tract,11-13 esophageal,14 and pancreatic cancer15,16 among individuals who worked in drycleaning establishments; however, since most of these studies involved exposures to various solvents in addition to PERC, a conclusive link between PERC exposure and cancer could not be made.
Although PERC has been a known animal carcinogen since the early 1990s,17 the International Agency for Research on Cancer (IARC) did not find adequate evidence to classify the solvent as a possible human carcinogen until recently.18 In 1995 the IARC classified PERC in group 2A, meaning that it is probably carcinogenic to humans. IARC also has recently classified drycleaning in group 2B, meaning that it is possibly carcinogenic to humans. Cancer mortality research is continuing at NIOSH and other research organizations.
PERC Evaluation Criteria.—The current OSHA permissible exposure limit (PEL) for PERC is 100ppm, as an 8-hour time-weighted average (TWA). The acceptable ceiling concentration is 200 ppm for five minutes in any three-hour period, not to exceed a maximum peak of 300ppm.19 OSHA had lowered the PEL to 25 ppm in 1989 under the Air Contaminants Standard.20 In July 1992, the 11th Circuit Court of Appeals vacated this standard. OSHA is currently enforcing the 100 ppm standard; however, some states operating their own OSHA-approved job safety and health programs continue to enforce the lower limits of 25 ppm. OSHA continues to encourage employers to follow the 25ppm limit.21 NIOSH considers PERC to be a potential occupational carcinogen.22 The American Conference of Governmental Industrial Hygienists (ACGIH) threshold limit value (TLV®) for PERC is 25 ppm.23
Current Exposures.—OSHA Integrated Management Information System (IMIS) data from 1984-1988 indicated that approximately 20% of exposures measured in U.S. drycleaning shops exceeded 100 ppm for PERC.24 The more recent and comprehensive data gathered by the International Fabricare Institute's (IFI) vapor monitoring service, using passive monitoring badges, reported a lower percentage of shops exceeding 100 ppm TWA. A summary of the IFI data is shown in Table 2.
Table 2: Passive Air Monitoring Results Collected by International Fabricare Institute
Before 1/1/87 | 1/1/87-9/30/89 | After 10/1/89 | |
---|---|---|---|
TRANSFER (AVG TWA PPM) |
55.3 ppm | 46.4 ppm | 42 ppm |
%>25 ppm | 76.2% | 59.9% | 56.8% |
%>100 ppm | 7.7% | 5.6% | 7.0% |
DRY-TO-DRY*** (AVG TWA PPM) |
20.5 ppm | 16.1 ppm | 17.2 ppm 16.9 ppm* 16.7 ppm** |
%>25 ppm | 24.3% | 18.5% | 18.6%* 17.2%** |
%>100 ppm | 1.0%> | 0.8% | 1.3%* 0.8%** |
*Denotes dry-to-dry refrigerated with small vent to purge cylinder at end of dry cycle.
**Denotes dry-to-dry refrigerated with no vent.
***Denotes standard dry-to-dry with water-cooled condenser and vent at end of dry cycle.
Solvent Alternatives to PERC
Alternative drycleaning solvents are available, which can be effectively substituted for PERC. All petroleum-based, drycleaning solvents are aliphatic hydrocarbons having a carbon chain of eight to twelve carbons. Hydrocarbon solvents are usually produced through fractional distillation of crude oil to produce various cuts, such as gasoline, naphtha, Stoddard solvents, mineral spirits, and kerosene. There are inherent properties that all petroleum-based drycleaning solvents possess. These properties include flammability, solvent power, volatility, odor, and toxicity.25
Petroleum-based solvents have a much lower Kauri-Butanol (KB) value than PERC. The KB value is a relative index of solvent power. On this scale, benzene is equal to 100, and all other solvents are compared to it. Higher KB values imply better removal of oil and grease stains.26 Linear paraffins generally have relatively low KB values while aromatics generally have high KB values.
Volatility refers to the propensity of a liquid to vaporize and is quantitatively expressed as vapor pressure. The evaporation rates for Stoddard solvents are between three and six times higher than the reference solvent, n-butyl acetate. Newer petroleum-based solvents have rates as low as 10% of the reference solvent. Because petroleum-based, drycleaning solvents generally have a lower vapor pressure than PERC, the drying process takes longer for garments cleaned with these solvents than those with PERC.
Petroleum-based solvents have a distinctive odor. Linear and branched hydrocarbons have relatively low odors while naphthenes and aromatics have strong and usually objectionable odors. Petroleum-based solvents also provide a better living condition for the growth of bacteria when water is present. The products of metabolism can cause very unpleasant odors, which can be retained by the garments. Because of this, distillation is very important, as well as antibacterial additives in the solvent.27 Petroleum solvents are toxic, but they are generally thought to be less toxic than PERC. Because the vapor pressures are lower than PERC, exposures from inhalation will generally be lower.
Health Effects of Petroleum-Based Drycleaning Solvents.—Aliphatic hydrocarbons are asphyxiants and central nervous system depressants. Aliphatic hydrocarbons have different toxicological properties, often based upon the length of their carbon chains. Most will cause irritation of the skin and mucous membranes of the upper respiratory tract. Repeated and prolonged exposure may cause dermatitis. Aspiration of liquid aliphatic hydrocarbons may cause diffuse chemical pneumonitis, pulmonary edema, and hemorrhage. Contamination of aliphatic hydrocarbons by benzene will significantly increase the hazard.
The most common petroleum-based drycleaning solvents in the U.S. are Stoddard solvents and mineral spirits. Sufficient quantities of either of these solvents can cause central nervous system depression. Symptoms include inebriation followed by headache and nausea. In severe cases, dizziness, convulsions, and unconsciousness occasionally result. New petroleum-based solvents have recently been developed; however, there is a lack of health effects data for these new solvents.
Evaluation Criteria for Mineral Spirits.—Some shops use mineral spirits in their drycleaning machine. The current OSHA PEL for mineral spirits is 500ppm, 8-hour TWA. There is no 15-minute short-term exposure limit or peak exposure limit. The NIOSH recommended exposure limit for mineral spirits is 350 mg/m3 or approximately 66 ppm. The American Conference of Governmental Industrial Hygienists (ACGIH) threshold limit value (TLV®) for mineral spirits is 100 ppm.28
Exposure to Spotting Chemicals
The chemicals commonly used in the U.S. to treat stains through pre-spotting and post-spotting are trichloroethylene; various ketones, especially methyl isobutyl ketone; petroleum naphtha; and hydrofluoric acid. Individuals who perform the spotting process could be exposed to many of these toxic chemicals through skin or eye contact and inhalation of vapors. However, the primary hazard posed by the majority of the chemicals is skin damage, resulting from chronic or acute exposure, or injury to the eyes. Although chemicals that readily vaporize and have a high toxicity can pose an inhalation risk, previous studies have shown that inhalation exposures are minimized because of the limited quantities of chemicals and the intermittent nature and short duration of the spotting task.5 Commonly, PERC exposures during spotting are many times lower than OSHA standards, as are other spotting chemical exposures, which are often below detection limits.29
Trichloroethylene is a colorless, nonflammable, noncorrosive liquid, having a "sweet odor" that is characteristic of some other chlorinated hydrocarbons. Exposure to trichloroethylene vapor can cause irritation of the eyes, nose, and throat. Prolonged skin contact with liquid may cause dermatitis. Acute exposure depresses the central nervous system and may cause headache, dizziness, vertigo, tremors, and nausea, or vomiting. In extreme cases, unconsciousness and death have been reported. Trichloroethylene addiction and peripheral neuropathy have been reported.9
The ketone family includes acetone, diacetone, methyl ethyl ketone, methyl n-propyl ketone, and methyl isobutyl ketone. Methyl isobutyl ketone is the one ketone that is primarily used in paint, oil, and grease removers. The route of entry for ketones is inhalation of vapors or percutaneous absorption. These solvents produce dry, scaly, and fissured dermatitis after repeated exposure. High vapor concentrations may irritate the conjunctiva and mucous membranes of the nose and throat, producing eye and throat symptoms. High concentrations can produce narcosis with symptoms of headache, nausea, lightheadedness, vomiting, dizziness, incoordination, and unconsciousness.9
Petroleum naphtha is an organic solvent used to dissolve or soften oils, greases, paints, and varnishes. Route of entry for this chemical is inhalation of vapors or percutaneous absorption. Naphthas are irritating to the skin, the conjunctiva, and the mucous membranes of the upper respiratory tract. Skin "chafing" and photosensitivity may develop after repeated contact with the liquid. If confined against skin by clothing, the naphthas may cause skin burns. Sufficient quantities cause central nervous system depression, and symptoms include inebriation, headache, and nausea.9
Dilute hydrofluoric acid poses a greater risk than the other spotting chemicals of acute dermal exposure; however, many of these chemicals can cause occupational dermatitis from chronic exposure to the skin. Hydrogen fluoride and its aqueous solution, hydrofluoric acid, are primary irritants of skin, eyes, mucous membranes, and lungs. Thermal or chemical burns may result from contact. Chemical burns cause deep tissue destruction and may not become symptomatic until several hours after contact, depending on the concentration. Nosebleeds and sinus trouble may develop following chronic exposure to low levels of fluoride in air.9
Evaluation Criteria for Spotting Chemicals.—The following criteria for spotting chemicals applies to chemicals for which air sampling was performed. Trichloroethylene has a PEL of 100 ppm as an 8-hour TWA, and a short-term exposure limit (STEL) of 200 pm;19 The NIOSH recommended exposure limit (REL) is 25 ppm, as an 8-hour TWA.20 For 2-butoxyethanol, the OSHA PEL is 50 ppm27 and the NIOSH REL is 5ppm.20 For hexylene glycol, NIOSH recommends a ceiling of 25 ppm.20 For methyl isobutyl ketone (MIBK), the OSHA PEL is 50 ppm, and the STEL is 75ppm.27 For n-butyl acetate, both NIOSH and OSHA have a PEL/REL of 150 ppm, and the STEL is 200 ppm.20,27
Combined Exposures.—The combined exposures of the drycleaning solvent PERC with various spotting chemicals is a concern. The ACGIH TLV® value for PERC is 50 ppm. Because PERC and other drycleaning/spotting solvents have some similar health effects, the additive effect of exposure must be computed as a combined exposure (CE).
Ergonomic Risk Factors
Ergonomics is the study of human abilities and characteristics that affect the design of equipment, systems, and jobs. Its aims are to improve efficiency, safety, and well being. As such, ergonomics can be applied to relieve and prevent work-related injury or illness to the musculoskeletal system of the worker. Ergonomic risk factors can include excessive manual force, repeated and sustained exertions, temperature extremes, vibration, and awkward postures resulting from inappropriately designed workstations, equipment, and work methods. Other factors are excessive work rates and duration, external pacing of work, shift work, imbalanced work to rest ratios, and restriction of worker body movement. Work-related musculoskeletal disorders can result in damage to tendons, tendon sheaths, muscles, nerves, and ligaments of the area affected.30,31
Highly repetitive tasks may consist of rapid and frequent high velocity muscle contractions. Such tasks cause the muscles to develop less tension than when contracting slowly and thereby require more muscle effort and recovery than less repetitive tasks.32 Insufficient recovery time can contribute to the incident rate of cumulative trauma disorders and can compound the musculoskeletal symptoms from repetitive tasks. In one study that did not involve drycleaning workers, the prevalence of tenosynovitis and humeral tendinitis was significantly higher for workers engaged in machine-paced repetitive assembly work than for workers with variable tasks. Repetitive motions of the hands for some workers reached up to 25,000 cycles per workday.33
Awkward or sustained postures can pose a risk of biomechanical stress to the body, especially the joints of the upper extremities and surrounding soft tissue. Several shoulder ailments, such as thoracic outlet syndrome, have been associated with workers repeatedly reaching above shoulder level.34 Reaching above shoulder level is an activity that frequently occurs in drycleaning shops during pressing and hanging of garments. In addition, work postures involving elevated arms could accelerate tendon degeneration by increasing the friction of tendons.35 This increased friction could be related to a decreased amount of synovial fluid acting as a lubricant.
Ergonomic Risk Factors in Drycleaning.—Ergonomic risk factors in the drycleaning industry primarily occur among workers performing pressing operations that are dynamic and repetitive tasks, requiring reaching, precision gripping, and maintenance of awkward postures. These awkward postures are also present during material handling when heavy lifting may occur. In addition, pressers spend much of the day standing, which adds a potential risk for the lower limbs. Studies have shown that muscles subjected to static work require more than 12 times longer than the original muscle-contraction duration for complete recovery from fatigue.36 Information gathered by NIOSH researchers has shown a high incidence of back pain among laundry and drycleaning workers.37
Ergonomic Criteria.—Ergonomic risk factors related to garment pressing are evaluated through time study and evaluation of workstation design and anthropometry. High repetition/insufficient recovery time, awkward postures, and other risk factors all contribute to cumulative trauma disorders.27 Repetitiveness and recovery time are evaluated according to cycle time. Low repetition jobs are categorized as such if the cycle time exceeded 30 seconds or less than half the cycle time involved to perform the same kind of task. High repetition jobs are those with cycle times less than 30 seconds or over half the cycle devoted to similar tasks.38 Awkward and sustained postures are examined with respect to guidelines found in the current literature.
Fire Hazards
Drycleaning with petroleum-based solvents differs significantly from drycleaning with PERC. The difference goes beyond the fact that the petroleum-based solvents are flammable and PERC is not. However, when the health and safety hazards of petroleum-based solvents are considered, flammability is the most important property.
Flammability of Petroleum-Based Solvents.—Approximately 10% of drycleaning shops in the U.S. use traditional, petroleum-based solvents, such as Stoddard Solvent/mineral spirits. All of these solvents are flammable or combustible liquids. Mineral spirits is a class II, combustible liquid with a flash point of 49°C (120°F). Its lower explosive limit is 0.7% or 7,000 ppm.
Exposure to the products of combustion presents numerous hazards to humans. Most prominent among these are effects from heat, impaired vision because of smoke density or eye irritation, narcosis from inhalation of asphyxiants, and irritation of the upper or lower respiratory tracts. These effects often occur simultaneously during a fire and can contribute to physical incapacitation, loss of motor coordination, faulty judgment, disorientation, restricted vision, and panic. Smoke and gases are responsible for approximately 70% of deaths during a fire.39
Carbon monoxide is generally the most abundant toxic gas produced during a fire. Carbon monoxide is produced in an accidental fire when some of the carbon present in organic materials is incompletely oxidized. Because of the large number of textiles present in drycleaning shops, the production of hydrogen cyanide gas is another cause for concern during a fire. Hydrogen cyanide is produced from burning materials that contain nitrogen. Nitrogen is present in natural and synthetic materials, such as wool, silk, acrylonitrile polymers, and nylons. Hydrogen cyanide is a rapidly acting toxicant, which is approximately 20 times more toxic than carbon monoxide.27
Fire Codes.—The fire laws of the state, county, fire district, or community delegate general responsibility and authority to the fire officials involved in fire prevention activities. Many large cities have adopted some regulations from codes written by national technical organizations, such as the National Fire Protection Association (NFPA) or the Building Officials and Code Administrators (BOCA). Codes affecting drycleaners that are commonly adopted are:
- NFPA 30—Flammable and Combustible Liquids Code,
- NFPA 32—Standard for Drycleaning Plants,
- NFPA 101—The Life Safety Code,
- BOCA Basic Fire Prevention Code
Some older, drycleaning shops are not required to comply with codes that were passed after that shop began operation. This process is known as "grandfathering." However, compliance with current codes should reduce the risk of a fire and the associated property damage, injury, or death. Compliance may also reduce property insurance premiums. According to NFPA 101, drycleaning plants are classified as industrial occupancies. According to NFPA 101 and the BOCA code for drycleaning plants, those facilities having greater than 60 gallons of combustible liquid present are considered a high hazard area.
The Study
Research Objectives
NIOSH began the present study of the drycleaning industry as a re-evaluation of the 1980 NIOSH Report. Investigators wanted to determine which of the previous engineering control recommendations were still valid, in addition to providing drycleaners with current recommendations for practical control measures. The focus of this study was to determine the best controls for PERC exposure; however, other health and safety hazards in the industry were evaluated on a more limited basis.
NIOSH researchers prepared a preliminary hazard analysis (PHA) for the drycleaning industry. The PHA was based upon previous industry studies and walk-through surveys. For this PHA, a hazard was defined as an activity or condition that posed a threat of loss. During this analysis, the hazards listed below were identified:
- p inhalation of PERC and other solvent vapors
- p ergonomic risk factors
- p exposure to hazardous chemicals used in the spotting process
- p fire hazards
- p direct (dermal) exposure to PERC
- p thermal burns
- p heat stress
- p mechanical hazards
- p electrical hazards
- p slips/ trips/ falls
These hazards are listed from top to bottom in decreasing order of risk. The level of risk was based upon two factors:
- likelihood of occurrence
- severity of consequence
Each risk ranking is of a qualitative nature based upon the professional judgment of the authors. Because of limited resources, the authors concentrated on the following health and safety hazards in the drycleaning industry:
- p inhalation of PERC and other solvent vapors
- p ergonomic risk factors
- p exposure to hazardous chemicals used in the spotting process
- p fire hazards
The study objective was met by evaluating controls for the various hazards and documenting results in NIOSH reports as shown in Table 3.40-49
Table 3: Hazards Studies in Plant Survey Reports
ECTB Report # |
PERC Dry-to-Dry |
PERC Transfer |
Petroleum | Spotting Agents |
Ergonomics | Fire Safety |
---|---|---|---|---|---|---|
201-11a | X | X | ||||
201-12a | X | |||||
201-13a | X | |||||
201-13b | X | |||||
201-14a | X | |||||
201-15a | X | |||||
201-16a | X | X | ||||
201-17a | X | |||||
201-18a | X | X | X | |||
201-19a | X | X |
Study Design
Ten drycleaning shops were visited during walk-through and in-depth surveys between August 1993 and January 1995. Following literature searches and reviews of previous NIOSH research reports, NIOSH investigators conducted four walk-through surveys to observe a variety of drycleaning operations. Photographs were taken during these initial surveys, as well as limited air sampling and ventilation measurements.
Results of the walk-through surveys helped determine specific businesses of interest for the six in-depth surveys. NIOSH engineers, industrial hygienists, and ergonomists surveyed each site, evaluating equipment, controls, and potential hazards (exposures to PERC and spotting chemicals, ergonomic risk factors, and fire hazards). Air sampling, video-exposure monitoring, ventilation system measurements, and process and workplace observations were performed. These data were evaluated to determine the effectiveness of each control system. Plant reports were prepared, which presented the data and results of the analysis, conclusions, and recommendations. These plant reports have served as the basis for the findings outlined in this report, as has information gathered during a World Health Organization (WHO) fellowship to study drycleaning in Europe.
Typical Drycleaning Process
The walk-through and in-depth surveys of various commercial drycleaning shops in the U.S. revealed that although practices varied from one shop to another, the overall drycleaning process was similar. The typical process begins when garments are brought to the shop by customers or arrive by van from another "satellite shop," which does no drycleaning on site. Garments are initially tagged for identification. Prior to spotting or being loaded into the drycleaning machine, garments are typically inspected and sorted according to weight, color, and finish. Modern garments are made from many different types of fabrics, and most drycleaners have the tools to clean all types.
Spotting
Particular attention was paid to spotting during the surveys to determine if excessive exposures occurred during this process. The spotting process might assume greater importance if wet cleaning methods in the U.S. were more widely used. Information was gathered prior to shop visits to determine which spotting chemicals a particular shop used most frequently. Purchasing records and Material Safety Data Sheets were reviewed.
In a typical shop, garments with visible stains are routinely treated at the spotting station. Spotting involves the selective application of a wide variety of chemicals and steam to remove specific stains from the garments. The three general categories of stains are water soluble, solvent soluble, and insoluble. Stains rarely consist of a single substance. Spotting chemicals and chemical mixtures are either solvent-based liquids (dryside) or water-based detergents (wetside). Wetside chemicals, which may contain water, remove water-soluble stains; and dryside chemicals, which never contain water, remove solvent-soluble stains.
The spotting chemicals, contained in small, plastic squeeze bottles, are applied to the stain. Spotting usually occurs on a spotting board equipped with pressurized air, steam, and water guns designed to flush the chemicals and stains from the garment. Air, steam, a small brush, a spatula, and fingers are all used to help break up the stains and wash them away. A pedal-actuated vacuum is used to capture the spotting chemicals, which are either held in a local storage reservoir or transported to a vacuum canister for discard.
In addition to PERC, some of the more common chemicals and chemical families for spotting are other chlorinated solvents, amyl acetate, petroleum naphtha, oxalic acid, acetic acid, esters, ethers, ketones, dilute hydrofluoric acid, hydrogen peroxide, and aqueous ammonia. Each of these chemicals are used in limited quantities. Most spotting chemicals are purchased from a company that supplies proprietary products to the industry. However, some shops use their own concoctions, which are prepared by individuals highly skilled in the art of stain removal.50
The spotting process has two components: pre-spotting, which involves dryside chemicals to remove or loosen solvent-soluble stains; and post-spotting, which utilizes wetside chemicals to remove water-soluble stains. Water-soluble stains, which may further set during the drycleaning process, are pre-spotted before drycleaning. Post-spotting is often used if the stain was not visible before drycleaning, or if the stain was not completely removed after pre-spotting and drycleaning. However, some shops utilize the more time-intensive post-spotting exclusively since many spots are removed during drycleaning. Some spotting processes involve little use of tools; the solvent is simply squirted liberally on all the stains before the garments are cleaned in the machine.
Machine Cleaning
Drycleaning, a three-step process, involves washing, extracting, and drying. A diagram of this process can be seen in Figure 1. Before washing, a worker adds detergent to the solvent in one of two ways: 1) A charge detergent is added to the solvent in set concentrations. The charged solvent is re-used in successive loads, and fresh detergent is periodically added to maintain the proper detergent concentration. 2) Injection or no-charge detergent is added to each load, based on each load's weight. Water is added to the system before or during drycleaning and aids in removing water soluble soils from the fabric.
To begin washing, clothes are manually loaded into the machine, followed by the solvent. The contents of the machine are then agitated for a period of time, allowing the solution to remove soils. Next, the clothes are spun at a high speed to extract the solvent.
After extraction, the fabric is tumbled dry. The drying process may occur in the same machine or a different one, depending on the system. Recirculated warm air vaporizes the residual solvent. Unheated air is then passed through the system during the cool-down cycle. This step reduces wrinkles. Following cool-down in vented machines, fresh air is passed through the system to freshen and deodorize the clothing during the aeration step.27 Garments are then removed from the machine prior to pressing.
Figure 1.The drycleaning process flow diagram
Drycleaners use filtration and/or distillation to recover and purify solvent. Filtration removes insoluble soils, nonvolatile residues, and loose dyes from the solvent and, in some cases, soluble soils. Filtration is usually a continuous process in which the solvent passes through either an adsorbent powder or filter cartridge, both needing periodic replacement. Additionally, new, powderless, spin-disc filters51 significantly reduce the generation of hazardous waste because they are regenerated instead of discarded.52
Distillation, used by 90% of the industry, removes soluble oils, fatty acids, and greases not removed by filtration. Drycleaning stills typically consist of a kettle, condenser, and separator. Distillation occurs by heating PERC to its boiling point. The PERC vaporizes and condenses back into a liquid form. During this process, nonvolatile impurities, which do not evaporate, remain at the bottom of the still and are discarded as hazardous waste. Both filtration and distillation produce solid wastes containing PERC.
Pressing
Pressing is generally a dynamic and repetitive task that requires reaching and precision gripping. Pressers usually stand at nonadjustable workstations for much of the day and reach well overhead for hanging garments. When a garment is placed on a pressing machine, it is pressed between two surfaces, at least one of which is heated to a temperature around 149°C (300°F).
Some of the equipment used by pressers includes general utility presses; puff irons; pants toppers; finishers; electric irons; bosom, body, and yoke presses; collar, cuff, and yoke presses; and sleevers. Because this equipment is highly specialized, drycleaners do not necessarily have all of these presses. Once the garments have been completely pressed, they are returned to the overhead rack and wrapped in plastic for customer pick-up.
Drycleaning Machine Control Technologies
Shops included in the current NIOSH study were collectively selected to represent a cross-section of the controls available within the drycleaning industry. The most important factor for site selection was the effectiveness of the control system for reducing exposures to PERC. The NIOSH study evaluated the primary working hypothesis that four general categories of drycleaning machines were capable of maintaining an 8-hour TWA personal exposure to PERC of less than or equal to 25 ppm.
The four general categories of drycleaning machines evaluated were:
- transfer machines
- vented and nonvented dry-to-dry machines
- machines with refrigerated condensers and/or carbon adsorbers
- "fifth generation," nonvented, dry-to-dry machines, having residual controls.
Two Basic Types of Drycleaning Machines
Two basic types of machines are generally used in drycleaning: transfer and dry-to-dry. Transfer machines are older, less expensive, and require manual transfer of solvent-laden clothing between the washer and dryer, a source of high worker exposure. Dry-to-dry machines eliminate clothing transfer because items are processed in one step, entering and exiting the machine dry. Transfer machines process more clothing than comparably sized dry-to-dry machines because the process time is approximately half that of a dry-to-dry machine. To compensate, some owners of dry-to-dry machines reduce the cycle time, thereby increasing productivity. Such practices can also increase exposures that result from unevaporated residuals in the drycleaned clothing.53
Transfer machines are generally vented, but dry-to-dry machines can be vented or nonvented. Vented dry-to-dry machines exhaust residual solvent vapors directly into the atmosphere or through some form of vapor recovery system, usually during the aeration process. Nonvented dry-to-dry machines are essentially closed systems, which are open to the atmosphere only when the machine door is opened. These machines recirculate the heated drying air through a vapor recovery system and back to the drying drum, eliminating the aeration step. Unfortunately, significant concentrations of PERC remain in the drum at the end of the cycle.
Approximately 70% of the drycleaning machines found today in the U.S. are of the newer dry-to-dry design. Transfer machines are no longer manufactured in the United States because of the high solvent usage rate, emissions, and exposures during transfer. However, used or reconditioned transfer machines can still be purchased. Either PERC or petroleum-based solvents can be used in dry-to-dry or transfer machines, but PERC is the solvent of choice for the majority of U.S. drycleaners.
Two Primary Vapor Recovery Technologies
The two primary technologies used to recover PERC vapors from drycleaning machines are the carbon adsorber and the refrigerated condenser. Carbon adsorbers are used in approximately 35% of controlled machines and refrigerated condensers, in approximately 65%. Carbon adsorbers remove PERC molecules from the air by passing solvent-laden vapors over activated carbon with a high adsorption capacity. The carbon is then desorbed and the PERC recovered, or the carbon is discarded when saturated. Carbon desorption typically occurs with steam or hot air. Desorption can be done automatically after each load, at the end of the day, or it can be done at other intervals depending on the PERC concentration and amount of carbon. If not done regularly, the carbon bed will become saturated and ineffective.
Refrigerated condensers use a refrigerant to cool the solvent-laden air below the dew point of the vapor to recover the PERC. The number of transfer machines using refrigerated condensers is roughly equivalent to the number of transfer machines using carbon adsorbers. However, on dry-to-dry machines there are approximately twice as many refrigerated condensers in use (see Table 4).
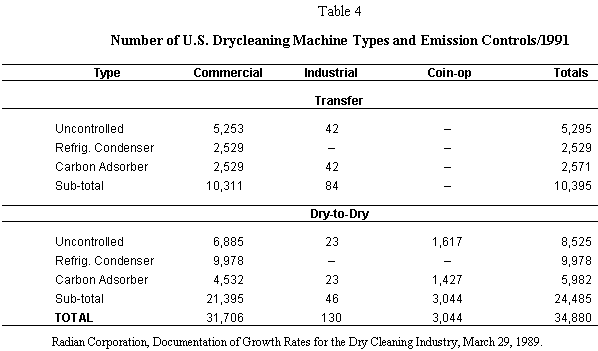
Drycleaning Machine Types in the U.S.
In 1988, the International Fabricare Institute (IFI) conducted a national drycleaning plant and equipment survey in which 5.8% of U.S. drycleaners participated. Results of that survey indicated that 79% of the shops responding used PERC only, and another 9% of shops used PERC and another solvent. For all PERC drycleaning machines, regardless of age, approximately 34% were dry-to-dry nonvented, 32% were dry-to-dry vented, and the remaining 34% were transfer machines. For PERC drycleaning machines that were less than five years old at the time, approximately 62% were dry-to-dry nonvented, 31% were dry-to-dry vented, and 7% were transfer. The majority of PERC drycleaning machines had a capacity of 30-39 lb, followed by 40-49 lb, and 50-59 lb, respectively. The average cleaning volume was 1,926 lb of clothing per week.54
The Evaluated Drycleaning Machines
During the six in-depth surveys conducted in various U.S. commercial drycleaning shops, NIOSH investigators evaluated sources of emissions and exposures from machines in the four general categories given above. Descriptions of the specific drycleaning equipment evaluated follow.
The Evaluated Transfer Drycleaning Machine.—The transfer unit studied consisted of two separate machines: a J & T® Model 60, 60-lb washer and a Model SF-145 Hoyt® Solvo-miser reclaimer. Both machines were over ten years old. The washer and reclaimer were connected to a Kleenrite® Vapor Condenser. The reclaimer had an internal, water-cooled condenser and separate refrigerated, vapor condenser. The reclaimer operated in three different modes: dry, cool, and aerate. During the dry mode, recirculated air was heated and then cooled in the condenser to recover PERC. During the cool mode, the air was diverted to the separate vapor condenser and cooled to recover PERC. During the final aeration cycle, fresh air was drawn into the reclaimer and exhausted outside of the building.
The Evaluated Dry-to-Dry, Vented Drycleaning Machine.—An Omega® Model CE55, 55-lb dry-to-dry machine, which was about six years old, was evaluated. This machine had a refrigerated condenser as the primary vapor recovery device. The secondary vapor recovery device consisted of a small, centrifugal fan rated at 110 cubic feet per minute (cfm) that was ducted to a carbon canister. When the machine door was opened, a microswitch energized the fan to draw PERC-laden air from the cylinder through the activated carbon.
The Evaluated Dry-to-Dry, Nonvented Machine.—Two nonvented, refrigerated, dry-to-dry machines, each less than five years old, were evaluated: a Boewe® Permac Model P540, 46-lb dry-to-dry machine and a Fluormatic® Model M242, 30-lb dry-to-dry machine. Both had a refrigerated condenser as the primary vapor recovery device. Both machines were connected to a Rite-Temp® Model RTR1003AWC Chiller used to chill water for reclamation, distillation, and maintenance of proper solvent temperature. There were no secondary vapor recovery devices.
Modern "Fifth Generation" Machine Technology.—Modern, dry-to-dry, nonvented drycleaning machines with residual controls are commonly referred to as "fifth generation" machines. The design of "fifth generation" machines began in Germany where their use is now mandated primarily by the Second German Emission Standard. "Fifth generation" drycleaning machines have engineering controls which dramatically reduce residual PERC in the machine's cylinder at the end of the dry cycle. These closed-loop, dry-to-dry machines rely on both an integrated, refrigerated condenser and a large carbon adsorber to recover PERC vapors during the dry cycle. "Fifth generation" machines are much more effective at recovering solvent vapors while drying garments than are machines equipped with only a carbon adsorber or refrigerated condenser alone. They are capable of lowering the PERC concentration in the machine's cylinder to below 290 ppm at the end of the dry cycle.
"Fifth generation" machines use a single beam, infrared photometer to monitor the PERC concentration in the machine cylinder. An interlock on the machine door prevents the operator from opening the machine door until the PERC concentration in the cylinder is below 290 ppm. The drying cycle will continue to operate until the cylinder concentration is sufficiently low. Such sophisticated machines are expensive and not widely used in the U.S.
Two Boewe Passat® dry-to-dry, nonvented drycleaning machines with residual controls were evaluated. One machine was a model P546, 46-lb machine, and the other was a model P536, 36-lb machine. Both machines had an integrated, refrigerated condenser and a large regenerable carbon adsorber to recover PERC vapors during the dry cycle. These machines were designed to lower the PERC concentration in the machine cylinder at the end of the dry cycle. This was accomplished using a large carbon adsorption system to capture PERC in the airstream and a single beam infrared photometer to continuously monitor the PERC concentration in the machine cylinder. An interlock on the machine door prevented opening until the PERC concentration in the cylinder was sufficiently low. The machines had a cleaning cycle of 35 to 40 minutes; however, the drying cycle was often automatically extended to ensure that the PERC concentration in the cylinder was below 290 ppm. The operator could determine the PERC concentration in the cylinder by reading a printout from the infrared photometer. The emission-free, still-cleaning device required still-raking only once every three weeks. A dosing unit enabled the operator to perform garment waterproofing within the machine.
Methodology
The principle measurements in this study were air concentrations of PERC measured both with conventional air-sampling pumps with charcoal tubes, and real-time instruments.
Air Sampling
Personal, area, and background air sampling was conducted using NIOSH Method 1003 for PERC and other halogenated hydrocarbons. In this method, organic vapors were drawn through 100 mg/50 mg coconut shell charcoal tubes. Carbon disulfide was used to desorb the solvents from the charcoal tube. Analysis was done using a gas chromatograph, fitted with a flame ionization detector to determine PERC concentrations and, in some instances, to determine all halogenated hydrocarbons concentrations. Samples were collected over 120-minutes at a flow rate of 0.1 liters/minute and a volume of 12liters. The limit of detection for this method is 0.01 mg/sample.55
Two-hour consecutive personal sampling was conducted on all of the machine operators, as well as on some of the spotters and pressers who worked in proximity to the drycleaning machines. Two-hour consecutive samples were used to determine full-shift TWA exposures.The purpose of conducting personal sampling was to compare worker perchloroethylene exposures to a TWA of 25 ppm. In addition to TWAs, 5-minute and 15-minute exposures were measured during some manual tasks. This was done at a flow rate of 0.1 liters/minute and a volume of 0.5 and 1.5 liters respectively.
Area sampling determined which areas of the shop had the highest concentrations and were collected at various distances and locations around the periphery of the drycleaning machine. Air samples were generally collected in front of and behind the drycleaning machines, in the pressing area, in the spotting area, in the hazardous waste storage area, near the customer counter, and outside of the building. These locations were similar for each shop evaluated. This data helped in the development of strategies to reduce the exposures.
Air sampling was also used to evaluate the risk of chemical inhalation during the spotting process. Air sampling was conducted for two days to evaluate worker exposures to PERC, trichloroethylene, 2-butoxyethanol, hexylene glycol, MIBK, and n-butyl acetate. Additionally, five area samples were taken to determine concentrations of PERC and trichloroethylene. The ratio of equilibrium vapor concentration to TLV was used to compute a vapor/hazard ratio. Peak and 8-hour TWA personal sampling of spotters were conducted for halogenated hydrocarbons that could be sampled using NIOSH Method 1003. When combined exposures of PERC and other spotting chemicals were involved, the combined exposure (CE) was determined as follows.
CE = C1/T1+C2/T2+...+ Cn/Tn
Where:
Cn = Exposure to an individual contaminant (ppm)
Tn = The OSHA PEL for the individual contaminant (ppm)
If the value of CE is less than 1, the combined exposure is believed to be acceptable. When this calculation was used during the in-depth spotting evaluation, the OSHA PEL for each chemical was applied if available. For hexylene glycol, no OSHA PEL was available; therefore, the NIOSH ceiling of 25 ppm was used.
Real-Time Monitoring
Real-time monitoring was used to study how specific manual tasks and maintenance operations affected worker exposure to PERC. Some drycleaning procedures occurred frequently throughout the day, such as loading/unloading the machine, while others, such as cleaning the lint and button traps, were less often. Most of these tasks took between 5 and 30 minutes. Real-time monitoring of PERC exposures were performed using a MicroTIP® IS3000® (PHOTOVAC Inc, Thornhill, Ontario) with a 10.6 EV ultraviolet lamp. This instrument uses a photoionization detector (PID) to provide an analog output response proportional to the concentration of ionizable chemicals present in the air. The MicroTIP® was spanned, using 100 ppm isobutylene span gas, and calibrated for both PERC and mineral spirits, using five standard concentrations of PERC vapor and mineral spirits vapor. Instrument readings and actual concentrations were used to construct two calibration curves and find predictive equations. The following formula was used to convert the output of the PID (volts) to concentration of contaminant (ppm):
C(t) = IR(t) * CF* MR
where:
C(t) = concentration of vapor at time t (ppm)
IR(t) = instrument response at time t (volts)
CF = conversion factor from calibration equation
MR = MicroTIP® range
Information gathered using the MicroTIP® was electronically recorded on a Rustrak® data logger (Rustrak® Ranger, Gulton, Inc., East Greenwich, RI) and downloaded to a portable computer, using Pronto® software. During the gathering of real-time data, a video camera recorded worker activities. This videotape permitted detailed analysis of tasks for quantitative determination of work activities causing the highest exposures.
Real-time monitoring was used for brief periods of time and focused on worker exposure during manual tasks and maintenance operations which might be related to high exposures. The frequency of manual tasks varied from shop to shop. Some common activities and their approximate frequencies follow:
Maintenance procedure Approximate frequency Still cleaning Daily Filter replacement Demand related Filling the tank Demand related Water separator Weekly maintenance Button/lint trap cleaning Daily
Specific questions addressed from real-time monitoring results included:
- p Are certain controls more effective at reducing exposures around cleaning and pressing stations?
- p Do specific actions result in higher exposures?
- p How does air contaminant concentration decay over time?
Real-time monitoring was also used to study off-gassing of garments and to compare vapor recovery efficiency of the machines. A standard test swatch, approximately 5 in. by 6 in. and made of 51% rayon and 49% polyester, was added to several runs of the drycleaning machine. At the completion of the dry cycle, the test swatch was placed in a small glass test chamber. As the solvent residuals in the swatch vaporized, PERC concentrations were monitored and recorded, using the MicroTIP® and Rustrak® data logger. This method detailed garment off-gassing and provided continuous concentration profiles, which were used to quantitatively compare the vapor recovery system's performance for each machine evaluated.
Evaluation of Ventilation Systems
Another aspect of this study was the evaluation of ventilation system performance. The various components of both the local and general ventilation systems were documented in order to assess the role of the entire ventilation system in controlling worker exposures. Data gathered during study of the ventilation system was compared to recommended values in the literature.
The following factors were examined when appropriate:
- p exhaust hood design, dimensions, and location
- p hood face velocity, capture velocity, and flow rate
- p airflow patterns and velocity around the source of exposure
- p system design specifications
A Kurz® Model 1440 Air Velocity Meter was used to measure air speed. Smoke tubes were used to qualitatively evaluate airflow patterns near the machine and within the building.
General dilution ventilation was evaluated at each drycleaning shop studied. General ventilation can reduce contaminant concentrations in large areas that are not controlled locally. As part of the evaluation, a layout of the facilities was obtained, showing locations of exhaust ducts and makeup air. Flow rates, face velocities, and airflow patterns in the building were documented. All of the data gathered were compared to design specifications when possible.
Ergonomic Evaluation
Hazards and risk factors present during the pressing operation were evaluated by examining work station design, anthropometry, and conducting time studies of the tasks performed. Based upon walk-through surveys, preliminary information indicated that high repetition/insufficient recovery time, and awkward postures might be risk factors present during pressing operations. Interaction of these and other risk factors have been shown to result in cumulative trauma disorders.35,55
Repetitiveness and recovery time were evaluated by examining cycle time. This was accomplished by videotaping and analyzing tasks in their elemental forms. Awkward and sustained postures performed during the pressing operation were examined to determine whether they were a problem in light of the general guidelines which can be found in the current literature. Each of the tasks were videotaped and measurements were made to determine height, reach, anthropometric envelope, and physical layout of the workstation.
Work Practice Observations
Because work practices often have a dramatic effect on exposures, observations recorded during site visits were an important aspect of this study. Of particular importance were activities related to loading/unloading the machines, maintenance procedures, pressing operations, spotting, and use of personal protective equipment.
Control of Drycleaning Solvent Exposures
The following section gives results from the six in-depth drycleaning surveys, discusses exposures and emissions, and suggests control options for U.S. commercial, drycleaning shops. Information gathered during the WHO fellowship in Europe is included primarily in the sections addressing substitution and "fifth generation" drycleaning machines.
Sampling and Monitoring Results
Air Sampling
Results of personal air sampling can be seen in Table 5. Generally, air samples gathered near the drycleaning machine had higher PERC concentrations than those farther away from the machine. Similarly, the more time a worker spent near the drycleaning machine, the higher the PERC exposures tended to be. Those drycleaning machines that were designed to lower the PERC concentration, emitted from the machine cylinder, were more effective than traditional machines at reducing worker exposures. Operators received the highest exposures from loading and unloading the machine; whereas, pressers were primarily exposed from garment off-gassing.
Table 5: Time-Weighted Average Worker Exposures to PERC (for entire survey)
Transfer Equipment.—All but one of the daily TWA personal samples taken on the transfer machine operator and two pressers were below 25 ppm. The transfer machine operator was exposed to 19.5 ppm TWA PERC for the entire survey. The operator's two-hour samples ranged from 3.9 to 42.3 ppm. The two pressers, who did not work in as close proximity to the transfer machine as the operator, were exposed to 3.3 and 3.8 ppm TWA PERC during the entire survey. Statistical analysis showed a significant difference between the operator's and pressers' TWA exposures.
NIOSH investigators gathered 5- and 15-minute personal air samples on charcoal tubes during transfer operations and filter changing (Figure 2). Neither of these activities exceeded the OSHA ceiling of 200 ppm or OSHA peak of 300ppm. Exposure during transfer operations was 57.5 ppm for a 5-minute period and 21 to 22ppm during a 15-minute period. The reason for the differences between 5- and 15-minute concentrations was due to time taken for tasks. Exposure during filter changing was approximately 121 ppm for 5minutes and 118 ppm for 15 minutes.
Figure 2. Five-minute and fifteen minute personal exposures to PERC from transfer equipment.
The highest area concentrations were above the reclaimer door. The geometric mean concentration in that area was 15.2 ppm, which was significantly different from all other areas. It seems logical that these area concentrations would have been the highest because the air was heated, and the PERC was in the vapor state during loading/unloading the reclaimer, but the solvent and air in the washer were not heated.
Dry-to-Dry, Vented Equipment.—All of the individual personal samples taken for the dry-to-dry, vented machine were below 25 ppm. The machine operator was exposed to 15.8 ppm TWA PERC for the entire survey. Two-thirds of these exposures resulted from loading and unloading the machine. The two pressers were exposed to 5.0 and 2.5 ppm TWA PERC for the entire survey. The highest geometric mean area concentrations measured, 9 and 12 ppm PERC, were near the drycleaning machine where a vapor leak was detected. The next highest geometric mean concentrations, 6 and 8 ppm PERC, were above the machine door.
Dry-to-Dry, Nonvented Equipment.—The machine operator, a presser, and a clothing inspector were sampled at the shop having two nonvented dry-to-dry machines, and all individual personal samples were below 25 ppm. The machine operator was exposed to 7.8 ppm TWA PERC for the entire survey. Nearly half of this exposure resulted from loading and unloading. The presser and inspector were exposed to less than 1 ppm TWA PERC. The highest area samples, 5.4 and 5.7 ppm PERC, were taken above the drycleaning machines' doors. The next highest concentrations were behind the machines.
Dry-to-Dry, Nonvented with Residual Control.—Figure 3 summarizes personal air samples gathered for the two dry-to-dry, nonvented machines with residual controls. All of the personal samples were well below 25 ppm and were dramatically lower than exposures on any other machines evaluated. The operator of the "fifth generation" machine had the highest exposure to PERC, ranging from 0.31 to 4.9 ppm TWA. Almost all of the operator two-hour samples were below 2ppm PERC, and most samples were below 1 ppm. The only exception to these low exposures occurred when the operator raked the still bottoms of both machines. During the last morning of sampling, the operator was exposed to approximately 12 ppm over a two-hour period and 4.9 ppm full-shift TWA PERC primarily because of cleaning the stills. If the stills had not been cleaned, the TWA exposure probably would have been less than 2 ppm.
Figure 3. Time-weighted average worker exposure to PERC from "fifth generation" drycleaning machines. (Four days of air sampling.)
The pressers were protected from PERC vapors originating from the machine by ventilation and barriers between the pressing station and drycleaning machine. All of the PERC concentrations measured near the presser's breathing zone were at or below the limit of detection, 0.01 mg/sample. This minimal exposure resulted from almost no PERC retention in the clothing. Little PERC was detected on samples outside of the drycleaning room. This nondetection of PERC can be attributed to excellent machine design and ventilation near the machines. The highest area concentrations, ranging from 0.0 to 1.9 ppm, were detected above and behind the drycleaning machines.
Statistical Analysis of Air Sampling Data
Summaries of the personal air sample results and their statistical analysis are in Tables 5, 6, 7, and 8. All of the TWA and mean exposures to PERC in these tables were below 25 ppm. However, some of the individual two-hour samples exceeded 25 ppm, and so did a small number of the daily TWA exposures. Time-weighted average exposures would have been somewhat lower if sampling had occurred for a full 8-hour shift; however, air sampling generally occurred when the drycleaning machines were in operation, typically six or seven hours per day.
Statistical analysis was performed on log transformed air sampling data for PERC. A two-way analysis of variance (ANOVA) showed that job title and shop had a significant effect upon concentration (p<0.0001). A multiple comparison test with 5% significance level, least significant difference (LSD), was used to analyze concentration differences.
Table 5 gives the TWA personal air samples by job for each shop evaluated. The TWA exposures in the table are for the duration of the entire survey. At each shop evaluated, the machine operator had consistently higher exposures than did any other job title. Most of the workers performing other jobs were exposed to less than one-third of the machine operator's exposure. Much of the difference can be attributed to the fact that the other jobs did not include the peak exposures associated with loading and unloading the machine.
Table 6 provides arithmetic and geometric mean personal exposures to PERC by shop for machine operators and the results of the two-way analysis of variance (2-WAY ANOVA). It also includes the concentration range and geometric standard deviation. This statistical analysis indicates that the operator of the advanced, "fifth generation" drycleaning machines was exposed to significantly lower PERC concentrations than operators of any other type of machine. Differences between operator exposures at all other shops were not statistically significant.
*Different letters indicate a statistically significant difference using the least significant difference test. (Α = .05)
Table 7 gives the results of a one-tailed (Α = 0.05) t-test, comparing operator exposure to PERC at each shop evaluated to 25 ppm. All of the machines studied maintained operator exposures to PERC below 25 ppm with the exception of the shop having two dry-to-dry, vented machines. Another shop with similar equipment, but only one machine, was able to control exposures below 25 ppm. Part of this difference may be due to production volume; this shop had two machines and a higher volume of garments, which required machine loading/unloading nearly twice as often.
Statistically significant at (Α = .05)
Table 8 is a summary of personal exposures to PERC by job title across shops. As expected, the machine operator had the highest mean exposure to PERC, which was 13.3 ppm for all shops evaluated. The machine operators' exposures were significantly different from exposures experienced by pressers or "other" workers. The bulk of operator exposures resulted from loading/unloading the machine, or in some cases from transferring garments. The next highest mean exposure by job title, 6.8 ppm, occurred in a group of workers labeled as "other." This group included workers who were not full-time operators or pressers. Finally, the pressers from all of the shops studied were exposed to the lowest mean concentration, 2.1 ppm.
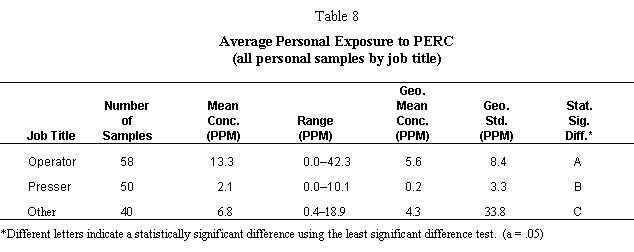
Real-Time Monitoring
Results of real-time analysis tended to support the air sampling results. Real-time results gave further insight into the reason why exposures from one type of machine were lower than exposures from another machine. The most significant source of PERC exposure occurred during loading/unloading the machines and garment transfer. Loading the machine frequently resulted in concentrations as high as or higher than unloading the machine due to air displacement. This was because of large quantities of PERC contaminated air being forced from the machine when dirty garments were loaded. Since high peak exposures occurred during these activities, the frequency of machine loading, unloading, and transfer played an important role in affecting total exposure. Exposure sources other than those directly from the machine, such as garment off-gassing and pressing, were substantially lower than exposures that occurred directly from the machine.
Transfer Equipment.—Figure 4 shows real-time data during garment transfer, loading the washer, and hanging the garments. Exposures during loading and unloading reached instantaneous concentrations between 1,000 and 1,500 ppm. The highest average exposures, 500-600 ppm, occurred during garment transfer from the washer to the reclaimer. The next highest average exposures occurred during loading the washer, unloading the reclaimer, and hanging clothing, respectively. Based on a comparison of real-time and air sampling results, over one-half of the operator's exposure resulted from loading/unloading the machine and garment transfer. A comparison of unloading the reclaimer, transfer, and loading the washer indicated that transfer generally occupied more time. After the garments were dried, hanging the garments took even more time than other tasks, but the average exposure during handling was relatively low, 14-21 ppm. Some of the bulkier garments, which retained solvent and took longer to dry, resulted in instantaneous PERC exposures near 70 ppm.
Figure 4. Operator exposure to PERC during clothing transfer, loading washer, and hanging clothing.
Dry-to-Dry, Vented Equipment.—The process of unloading took nearly twice as long as loading. Real-time monitoring (Figure 5) showed that average PERC exposure during loading was much higher than unloading the cleaned garments. The average exposure during loading was 846 ppm; average exposure during unloading was 271 ppm. The integrated exposure (area under the curve) was also higher during loading the machine, approximately 11,850 ppm*sec. versus 7,050 ppm*sec. Real-time measurements near the carbon canister on the top of the machine indicated that concentrations of PERC (approximately 1,500 ppm) were blown into the work environment each time the machine door was opened (Figure 6).The carbon canister was ineffective at capturing PERC in the exhausted air.
Figure 5. Operator exposure to PERC from a dry-to-dry, vented drycleaning machine during unloading/loading.
Figure 6. Real-time measurements of PERC concentration near carbon canister exhaust of a dry-to-dry, vented drycleaning machine.
Dry-to-Dry, Nonvented Equipment.—Concentrations during loading/unloading were higher than any other activity; however, the instrument used to conduct real-time monitoring in the present NIOSH study became saturated and did not read the highest concentrations. This was because the maximum concentration the instrument was capable of reading was 156 ppm. Real-time measurements taken by NIOSH researchers at other shops using dry-to-dry, nonvented machines were approximately 1,500 to 2,000 ppm during machine loading and unloading. Figure 7 gives operator exposure during loading and unloading a machine and hanging clothing. The tops of the largest peaks are truncated because of the upper limit of the real-time detector. The larger machine generally took longer to unload than the smaller machine. Hanging the clothing took approximately 9 minutes. For both machines, the average PERC exposure while loading the machine with dirty clothing was almost the same as unloading garments cleaned in PERC. The similar exposures were caused by PERC contaminated residual air being forced from the cylinder while the door was opened to admit unclean clothing.
Figure 7. Operator exposure to PERC from a dry-to-dry, nonvented drycleaning machine during loading, unloading, and hanging clothing.
When the 46-lb machine was loaded/unloaded, the integrated exposure to PERC was higher during unloading (1,955 ppm-sec. vs. 1,572 ppm-sec.); however, the average exposure was actually higher during loading (98 ppm vs. 89 ppm). The difference is made more profound through an examination of the median exposure during loading (147 ppm) versus unloading (98 ppm). Average exposure from loading and unloading the 30-lb machine was slightly higher than that from the 46-lb machine. There are two factors at work here: less efficient solvent recovery from the 30-lb machine and better local ventilation near it. Average exposure while hanging the clothing was approximately 5 ppm. The operator was exposed to higher PERC concentrations when hanging bulky items, which had not completely dried.
Dry-to-Dry, Nonvented with Residual Control.—Although these full-shift, TWA exposures were lower than at other shops, the greatest source of operator exposure from "fifth generation" machines continued to be from loading and unloading the machines. Exposures during this procedure peaked at approximately 160 ppm, which is an order of magnitude lower than most peak exposures at shops using different types of machines.
Figure 8 shows operator exposure during the first cycle of the day when only loading occurred. When dirty clothing was added to the cylinder, contaminated air was forced from the cylinder into the worker's breathing zone. This was characterized by a rapid increase and an almost instantaneous peak which approached 160ppm. The concentration in the worker's breathing zone dissipated over the next 10 to 20 seconds and then returned to zero. This peak occurred because the machine cylinder, which was not fully isolated from the other sources of PERC within the machine, was not purged immediately prior to the door's being opened. PERC vapors apparently diffused from the vapor loop, into the machine cylinder, and eventually out into the work environment because of air displacement during loading. Operator exposure for loading the 46-lb machine was higher during this first cycle than for loading a smaller machine. This result may have been caused by differences in general ventilation near the machine doors, greater air displacement from the machine cylinder, and/or differences in the PERC concentrations within the machine cylinder.
Figure 8. Operator exposure to PERC from "fifth generation" machine during the first cycle of the day.
Figure 9 gives operator exposure during unloading and loading both machines. For most cycles, average operator exposures and integrated exposures were higher during unloading than loading. The exception to this general finding occurred when dirty garments were processed in the 36-lb machine (Figure 9). The average operator exposure for loading was 101 ppm, which was significantly higher than the average exposure of 34.6 ppm for unloading. Again, in this instance, the machine had been idle for several minutes prior to the door's being opened. Because of this inactive period, PERC was able to diffuse from the sources within the vapor loop into the machine cylinder. PERC vapors were forced from the cylinder because the centrifugal fan provided insufficient airflow when the machine door was opened.
Figure 9. Operator exposure to PERC from "fifth generation" machine during unloading/loading.
Garment Off-gassing.—Garment off-gassing was evaluated for each machine during a typical cycle. Evaluation of garment off-gassing revealed that the "fifth generation" machines were much more effective at recovering solvent from the garments. This efficiency was directly related to machine design.
During an average cycle of the transfer machine, the total PERC off-gassing from the test swatch was 89.0 mg PERC/kg cloth. The dry-to-dry, vented machine had a total PERC off-gassing from the test swatch of 31.8 mg PERC/kg cloth. The total PERC off-gassing from the test swatch in the dry-to-dry, nonvented machines varied according to the size of the machine. The PERC concentration from the 30-lb machine was 126 mg PERC/kg cloth and 69.4 mg PERC/kg cloth for the 46-lb machine. Both "fifth generation" machines were extremely effective at recovering solvent from the garments. The total PERC off-gassing from the test swatch was 1.34 mg PERC/kg cloth. Figure 10 provides a comparison of typical off-gassing from a swatch cleaned in a "fifth generation" machine with a swatch from a refrigerated, dry-to-dry machine.
Figure 10. A comparison of typical swatch off-gassing from a refrigerated, dry-to-dry drycleaning machine versus a "fifth generation," dry-to-dry drycleaning machine. The total PERC off-gassed was approximately 31.8 mg PERC/kg cloth and 1.34 mg PERC/kg cloth, respectively.
Machine Maintenance
Real-time evaluation of drycleaning machine maintenance showed that exposures during maintenance were less than exposures during loading/unloading or transfer. Maintenance activities that were evaluated included cleaning the drycleaning machine's lint trap, button trap, and still; changing solvent filters; and disposing of hazardous waste. One reason for lower exposures from machine maintenance tasks than from loading/unloading was that the former occurred much less often than the latter.
Figure 11 provides operator's exposures during lint and button trap cleaning on a dry-to-dry, vented machine. The activity took less than 10 minutes, and the average exposure to the worker was approximately 22 ppm. Figures 12 and 13 give maintenance exposures on two modern, dry-to-dry machines with residual controls. One machine had a 46-lb capacity, and the other a 36-lb capacity. Figure 12 shows exposures for cleaning the lint traps. This task was done every day and involved cleaning the lint/button traps and disposing of hazardous waste. Normally, lint traps were cleaned in the morning. The average exposure during maintenance on the 46-lb machine was approximately 44 ppm PERC, and on the 36-lb machine, 16 ppm. For "fifth generation" machines, instantaneous exposures could be higher during maintenance tasks than during loading and unloading.
Figure 11. Operator exposure to PERC during maintenance on lint and button traps of a dry-to-dry, vented drycleaning machine.
Figure 12. Operator exposure to PERC while cleaning lint traps on a "fifth generation" machine.
Figure 13 presents operator exposures during still rake out on each machine. These stills were fitted with a pump that enabled the residue to be pumped directly into a safety can. This device reduced still rake out from a daily or weekly task to an approximately once-every-three-week task. Operator exposure to PERC while raking the still of the 46-lb machine was in excess of 156 ppm, the limit of detection, and that of the 36-lb machine averaged 35 ppm. During the cleaning of the 46-lb machine still, the instrument became saturated, which is shown by the horizontal line. The proximity of the 36-lb machine to a supply fan, which moved 2,100 cfm of air, helped to reduce airborne PERC concentrations.
Figure 13. Operator exposure to PERC while cleaning the stills on two "fifth generation" machines.
Figure 14 gives exposures for changing the solvent filters. There was no still on this machine; rather, clay and carbon filters removed both soluble and insoluble soils. There were several tubes which held five filters each. Each tube was changed once for every 10,000 pounds of clothing cleaned, or approximately once a month. Real-time monitoring revealed that the greatest exposures occurred when the filters were placed into the hazardous waste container and when the new filters were placed into the tubes. Higher exposures probably resulted from contaminated air being displaced by filter deposition or insertion, as Figure 14 demonstrates.
Figure 14. Worker exposure to PERC during changing clay/carbon solvent filters on a transfer machine.
Figure 15 shows worker exposure during machine maintenance on two nonvented, dry-to-dry machines. As was the case for most machines observed in the study, the lint and button traps were located behind the machines, near a wall. Fairly significant concentrations were discovered in this area. This background concentration can be attributed to exhaust from the secondary control device, located behind the machines. Additionally, lint from the lint trap and other hazardous waste was inappropriately stored behind the machines in a cardboard cylinder. The highest maintenance exposure occurred while the lint trap of the 80-lb machine was cleaned. The average exposure during this operation was approximately 180 ppm, as compared to the average exposure for cleaning the lint trap of the 70-lb machine, which was approximately 149 ppm.
Figure 15. Exposure to PERC while cleaning lint traps on two dry-to-dry, nonvented drycleaning machines.
Ventilation
Most of the shops studied had inadequate local and general ventilation systems to control worker exposures. Local ventilation can be used to reduce worker exposure during a variety of tasks, such as loading/unloading the machine, maintenance, spotting, or waterproofing, but loading/unloading is the most important activity to control.
None of the evaluated machines provided 100 feet per minute (fpm) air velocity at the face of the drycleaning machine doors. The door face velocity recommended by much of the literature is 100 fpm.56,57,58,59 In most cases, the airflow was significantly less, and in many cases there was no ventilation. This reduction and elimination of ventilation can be attributed to environmental regulations restricting solvent vapor emissions. Many machine designers have eliminated process ventilation to reduce emissions. Ventilation was used on machines in several evaluated shops as part of a secondary control that exhausted into the work environment. The air passed through a vapor recovery system that did not capture all of the PERC, and workers continued to be exposed to the remaining hazardous concentrations emitted from the machine. In one evaluated shop that exhausted air outside, air currents carried the contaminated air back into the shop through a nearby doorway.
General ventilation, appeared to be primarily used for comfort rather than for dilution of air contaminants. Many shops were located in buildings that were originally constructed for purposes other than drycleaning, and the ventilation systems were ill-equipped to remove or dilute hazardous vapors. Several shops had no operable windows to provide natural ventilation. Observed ventilation cases follow.
CASE 1:
At one shop evaluated, two modern "fifth generation" machines were used. These machines reduced the instantaneous PERC concentration in the cylinder to below 290 ppm (an order of magnitude lower than concentrations in machines of a different design). Because the PERC concentrations were so low, local exhaust ventilation was less of a concern. Although there was minimal airflow at the face of the open machine door, it was not a significant problem with respect to the overall control system because the concentration in the cylinder was so low.
Several propeller fans were located in the drycleaning area to provide dilution ventilation. Most of the PERC contaminated air originating from the machines was prevented from escaping into other areas because the room was under negative pressure. Figure 16 shows airflow measurements moving to and from the drycleaning area.
Figure 16. Airflow balance in/out of drycleaning room having effective general ventilation.
CASE 2:
A transfer unit was used at another shop consisting of a washer and reclaimer, which were connected to a vapor condenser. During the final aeration cycle, fresh air was drawn into the reclaimer and exhausted outside the building. The building, originally designed to be a gas station, had no operable windows. Face velocity at the open reclaimer door was approximately 78 fpm, and the airflow was approximately 221 cfm.
The exhaust exited the building through a hole in the wall, which was within several feet of an open doorway. Smoke tubes demonstrated that much of the PERC-laden air being exhausted reentered the building because of the poorly located reclaimer exhaust ducts. A depiction of the air currents entering the building and the resulting eddy currents are shown in Figure 17.
Figure 17. Air currents near the drycleaning machine in a room having poor general ventilation.
CASE 3:
Another shop had a dry-to-dry machine with a refrigerated condenser as the primary vapor recovery device. A small centrifugal fan, providing 110 cfm, was ducted to a carbon canister, which comprised the secondary vapor recovery device. When the machine door was opened, a microswitch energized the fan to draw PERC-laden air from the machine cylinder through activated carbon. These two controls operated independently.
Air velocity measured at the face of the opened drycleaning machine door was negligible. Two reasons for instantaneous exposures, ranging from 1,500-2,000 ppm, were noted earlier under loading and unloading the machine. The machine cylinder was not fully isolated from the other sources of PERC within the machine, and the cylinder was not adequately ventilated immediately prior to the doors being opened. These factors permitted PERC vapors to diffuse into the cylinder and escape when the door was opened. Inadequate airflow was the most important factor which contributed to the operator's daily TWA PERC exposure. Airflow patterns showed that PERC vapors escaping through the machine door not only exposed the operator but also were able to diffuse throughout the building, exposing other workers.
Waterproofing
Some drycleaning shops do not offer a waterproofing service. Additionally, many shops that do perform waterproofing, do not use the dip-tank method. However, dip-tank waterproofing operations occurred at several evaluated shops. Figures 18 and 19 give operator exposures during dip-tank waterproofing operations. Operator exposures were high because the operator was working over an open tank of PERC combined with small quantities of other chemicals used to waterproof clothing. The clothing was dipped into the PERC solution, raised, and allowed to drain. It was then hand carried to the drycleaning machine. There was no local ventilation during this task. The highest average exposures (approximately 150 ppm) occurred when the clothing was put into the drycleaning machine. Some of the recorded real-time values were significantly lower than actual values because the photoionization detector (PID) became saturated and was off scale. The greatest integrated exposure to PERC occurred when the clothing was scrubbed at the waterproofing barrel. Because this activity took longer than any other single task (approximately 140seconds), the average exposure was relatively high (approximately 100 ppm). Although short-term exposure was not evaluated during dip-tank waterproofing, it is probable that peak or short-term exposure limits of 300 ppm and 200ppm, respectively, would be exceeded during dip-tank waterproofing.
Figure 18. Average operator exposure to PERC during dip-tank waterproofing operations having no local ventilation.
Figure 19. Operator exposure to PERC during dip-tank waterproofing operations having no local ventilation.
Personal Protective Equipment
At most of the shops studied there was no established respiratory protection program. A review of OSHA citations in the drycleaning industry from January 1984 to January 1994 revealed that most violations resulted from noncompliance with one broad paragraph in the standard 29 CFR 1910.132a: "Personal protective equipment shall be provided, used, and maintained in a sanitary and reliable condition wherever it is necessary by reason of hazards of processes or environment . . . ."60 This paragraph addresses use and maintenance not only of respirators but also of other types of personal protective equipment.
All of the shops studied had respirators; however, most respirators were not properly maintained and were seldom used. Most of the respirators were defective, having deformed face pieces and straps that had lost their elasticity. Only one shop, which performed respirator fit testing, met the requirements in 29 CFR 1910.134 for a minimum acceptable program.
Discussion and Conclusions
How Exposures Occur
In order for occupational exposure to occur, PERC must come in contact with the body through inhalation, skin adsorption, or ingestion. In the evaluated drycleaning shops, the most frequent route of exposure was inhalation. Whenever PERC vapors escape or are emitted from the drycleaning machine, the potential for inhalation exists. These studies have identified two major pathways for the release of solvent vapors, which can result in exposures: atmospheric emissions and losses in hazardous waste. Atmospheric emissions are estimated to account for between 44% and 74% of total PERC losses, and the remainder occur during disposal of hazardous waste.61
Atmospheric emissions can occur from process or fugitive emissions. Process emissions, observed during this study, include process ventilation of the machine either directly to the atmosphere or through a vapor recovery device; and process emissions from opening doors on the drycleaning machine, such as the loading, still, button trap, or lint trap doors.
Fugitive emission sources that were observed include evaporation during clothes handling, equipment leaks, and evaporation from hazardous wastes. The EPA estimates that as much as 25% of solvent emissions from an uncontrolled drycleaning shop can be attributed to solvent leaks. Occupational exposures were shown to occur from many of these emission sources.
This study identified a number of important factors which can affect emission sources and ultimately exposures. The factors can be placed into four broad categories: machine design, ventilation, maintenance and housekeeping tasks, and equipment operation/operating procedures (Figure 20). These categories are not entirely separate and distinct.
Figure 20.Factors influencing worker exposure to PERC in drycleaning shops.
Machine Design and Number of Machines.—Evaluation of operator exposures indicated that the most important factor affecting PERC exposure was the drycleaning machine design. Research results showed that worker exposure occurred from three primary drycleaning machine sources: residual solvent expelled from the machine cylinder during loading/unloading, residual solvent off-gassing from garments, and solvent expelled by some machine vents during the deodorizing step.
Related to machine design is the machine capacity. Machine's having a larger capacity can clean more garments in fewer cycles than machine's having smaller capacities, thus reducing the number of times the machine must be loaded and unloaded and thereby reducing exposure. Another relevant factor is the number of drycleaning machines at each shop. Each machine can be thought of as a generation source. The number of drycleaning machines in a shop is an indicator of the quantity of garments being processed. The number of machines and quantity of garments processed will determine the number of times the machines must be loaded and unloaded and therefore will impact exposure.
Another source of solvent exposure arises from residual solvent vapors in insufficiently dried garments that are being hung, already hung, or being pressed. Machines that do not sufficiently dry the garments can permit clothing to off-gas into the work environment for days. Based on the real-time analysis during this study, it is clear that operator exposure from garment off-gassing was much less of a problem, however, than exposure from loading and unloading the drycleaning machine.
In every shop studied, the pressers were exposed to PERC concentrations that were approximately two to three times less than that for machine operators. Garment off-gassing can expose the person pressing the garments; however, real-time analysis graphically demonstrated that the instantaneous exposures were typically well below 50 ppm. Garment off-gassing tends to increase background concentrations of PERC within the shop, but is not the major factor affecting operator exposure.
In all of the evaluated shops, comparison of real-time and air sampling data demonstrated that the greatest source of operator exposure came from loading and unloading the drycleaning machines. Concentrations of PERC expelled from the machine drum, at the end of the dry cycle, ranged from several hundred ppm to over 2,000 ppm, depending on the design of the drycleaning machine and control options. This solvent-laden air, forced out into the worker's breathing zone during the machine loading/unloading process, contributed more to worker exposure than any other activity. The problem is exacerbated by environmental restrictions on venting in some localities.
Ventilation.—The findings from this research confirm that inadequate local exhaust and general ventilation increase exposures from process emissions. A study from the early 1980s conducted at 67 drycleaning facilities in New Jersey found 60% of transfer machines had inadequate local exhaust ventilation based upon air velocity at the face of the washer door. While 13% of the machines had no local exhaust, 15% had an inoperable fan, and 42% were below the recommended ventilation rate of 100 fpm. However, only 14% of dry-to-dry machines were below the recommended ventilation rate. Similar problems were also discovered during this study. Although more modern, nonvented, dry-to-dry machines are designed to significantly reduce process emissions, the lack of ventilation was shown to contribute to worker exposure by permitting PERC-laden air to escape from the machine into the work environment.
Ventilation is of particular importance near the drycleaning machine door and in the areas where clothes are hung immediately after they are removed from the machine. Some drycleaning shops have placed local exhaust vents on the floors because it was wrongly thought that PERC vapors, being heavier than air, would sink to the floor. However, a 5,000 ppm PERC air mixture is only 1.02 times heavier than air, and this small difference is easily overpowered by normal room air currents. Other evaluated shops had machines that exhausted inside the building, which increased worker exposures. General ventilation can also impact exposures. If plants are not designed to pass fresh air by the workers and draw contaminated air away from them, then high exposures may result.
Maintenance and Housekeeping.—Maintenance is an important part of any industrial process. Drycleaning is no exception. Well-designed equipment operates properly with a minimal need for routine maintenance. Some examples of equipment designed for minimal maintenance, which were observed during this study, include automatic desorption of some carbon beds used as a secondary control and emission-free still cleaning devices that eliminate the need to rake out the still. Nevertheless, there are many machine components that must be regularly maintained at various intervals. As observed during this study, machine maintenance can cause excessive exposures to PERC, such as when filters are changed, the still is cleaned or residue removed, the lint and button traps are cleaned, and the water separator maintained. In many shops, respirators may be needed to control exposures during maintenance.
The vapor recovery system is a critical machine component that requires both maintenance and monitoring. Carbon adsorbers and refrigerated condensers must be properly maintained to efficiently recover solvents. Refrigerated condensers require less maintenance than carbon adsorbers. The balance between condenser water temperature and drying air temperature is crucial for refrigerated condensers. If it is not cold enough, the solvent will not be recovered; and if it is too cold, the air will not effectively dry the garments. Carbon adsorbers require frequent desorption. If the carbon beds are not regularly regenerated or replaced, uncaptured solvent vapors can be discharged through vents which may increase worker exposure, as was observed during this study.62
Prolonged periods of inadequate maintenance and housekeeping can potentially result in severe exposure from leaks in older equipment. Leaks can allow vapors to escape or fluid drips and puddles to form, depending on the severity. Several vapor leaks were observed during this study, which caused increased solvent consumption and worker exposures. Lint and dirt build-up near the machines may make leaks more difficult to detect. PERC is corrosive to the machine gaskets. As gaskets age and are continually exposed to solvent, they become hard, cracked, and deteriorated. In one older study, 25 to 30% of businesses had visible solvent leaks; however, improvements to seals and gaskets in modern machines have significantly reduced this problem.63
Equipment Operation or Operating Procedures.—Excess levels of PERC may be present in the drycleaning machine cylinder if the extraction system fails, the vapor recovery system fails, or improper operating procedures are followed. Premature removal of garments from the drying cycle can increase exposures. Some operators may shorten the drying cycle to increase productivity. Thick, solvent-retaining items, such as heavy coats, comforters, or sleeping bags, require longer drying times, and operators may remove them prematurely. Real-time monitoring showed that when solvent-laden garments were removed from the machine, pressed, and hung, residual solvent in the garments evaporated into the work environment, often exposing workers directly or indirectly.
Another problem observed during this study was improper handling and storage of hazardous waste that increased background concentrations of PERC. Hazardous waste comes from the still residue, dirty filters or filter powder, contaminants in the lint and button traps, and water separator run off. If these materials are not properly handled and promptly stored in an air-tight container, evaporation of residual solvent may occur, increasing background concentrations, as observed during this study. If filters are not allowed to drain prior to changing, high exposures may occur.
Many workers are aware that certain tasks are associated with higher exposures to PERC, and many shops have respirators available. Unfortunately, many shops do not have a written respirator program with standard operating procedures for wearing respirators when workers perform those tasks or do not want the discomfort associated with wearing a respirator.
Overall Control Strategies
At drycleaning facilities, a combination of substitution, isolation, effective drycleaning machine design, and ventilation appear to be the most effective and realistic control approaches for reducing PERC exposure. Each of these control strategies must be applied based upon the needs of the shop. Substitution for the process, equipment, and material has been researched extensively in drycleaning. In terms of impact on the industry, process and equipment substitution has been successful, while until recently, substitution for PERC has been less promising.
Substitution.—Whenever a substance is found to be hazardous to health or to the environment, standard industrial hygiene practice dictates that a less dangerous material or process should be considered. Extensive work has been done to find a PERC alternative. Finding an effective substitute is difficult because many of the chemicals that potentially could be used fall under one of several classes, each having physical properties that make them toxic, flammable, hazardous to the environment, or technically unsuitable for cleaning garments (see Table 9).
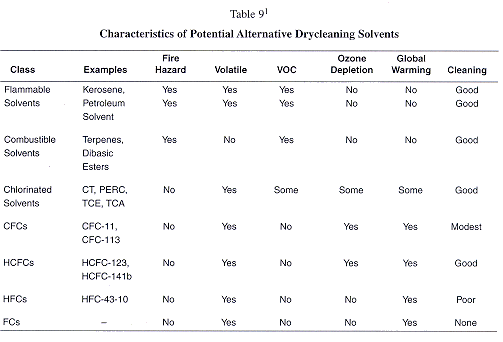
All of the new substitute technologies for PERC textile cleaning must meet certain criteria. First, they must break down the interactive forces which bind the soils to the textile surfaces. Second, they must carry away the loosened soils to prevent redeposition. Most importantly, the cleaning medium must prevent textile damage. If such a solvent can be used economically and under safe and environmentally acceptable conditions, the technology may be potentially successful for textile cleaning.2
There are a number of different substitute technologies that could potentially replace drycleaning with PERC; however, many of these technologies are only in the developmental stage. Technologies, that accomplish garment cleaning by using liquid carbon dioxide or ultrasound are currently under development. Two substitute technologies now in limited use are wet cleaning and petroleum-based drycleaning. Much of the original research and testing for these technologies has occurred in Europe. Information and discussion of these technologies, observed during a WHO fellowship, can be found in the following sections.
Wet Cleaning.—Wet cleaning became popular recently in Europe and the U.S. because of the strong environmental regulations restricting the use of solvents. Wet cleaning (by water immersion) is a method to clean garments that normally would have been cleaned in solvent. One difference between water and solvents is that water tends to expand natural and cellulose fibers, while solvents do not change the fiber properties. When natural and cellulose fibers expand, they also wrinkle, lose their strength, shrink, and lose their shape. In general, the higher the synthetic content of the garment, the lower the risk of shrinkage through wet cleaning.
According to discussions with experts in Europe, four factors play an essential role in soil removal: temperature, time, mechanical action, and chemical agents. The importance of each factor varies depending upon whether solvent or water is used for cleaning. High mechanical action and high temperatures tend to increase the expansion of natural fibers in water. Therefore, each of the factors must be properly blended to achieve the best cleaning results. There are minor variations in machine wet cleaning, but according to NIOSH research, most techniques are similar in that they all use:
- specially formulated wet-cleaning soaps and spotting agents, (consisting of enzymes, peptides, synthetic polymers, and anionic and nonionic tensides).
- increased extraction of water prior to drying, (extraction speeds as high as approximately 1,000 rpm).
- close monitoring of heat and moisture content during the drying process, (moisture sensors control the fabric drying. Temperature in the drum should not exceed 60°C (140°F) for normal garments and 50°C (122°F) for sensitive garments).
- machines designed to insure low levels of mechanical action during washing through speed reduction and time limits.64
Garments are washed with various levels of limited mechanical action based on garment type and amount of soilage. The greatest risk to the garment occurs during drying. Many fibers can be fully machine dried with little or no difficulty. However, delicate garments or those susceptible to high shrinkage must be machine dried for only a few minutes before being hung to air dry in the shop. Discussions with wet cleaning experts in Europe have revealed a number of pros and cons associated with the wet cleaning process.
One of the major advantages of wet cleaning is that there are none of the associated health or fire hazards found with drycleaning solvents. If shops exclusively performed wet cleaning, they would eliminate the burden of strict regulations.
Many soils are more easily removed with water than solvent. This is particularly true for water-soluble stains resulting from sugars, salts, drinks, body fluids, starch, milk, and most foods. However, it is not true for greases, oils, waxes, and resins.65
The cost of wet cleaning is comparable to cleaning a garment using solvent-based methods. Wet-cleaning machines are less expensive than solvent machines (see Table 10). However, this economic advantage is balanced over time by the additional costs of the water, chemical additives, and labor required to wet clean. A United States EPA multiprocess wet-cleaning report states that "... under certain situations, the wet cleaning process is technically feasible and economically competitive with PERC drycleaning. Wet cleaning appears to be a viable option to reduce the usage of drycleaning solvents."66
Table 10: Cost of Three Categories of Drycleaning Equipment
PERC | Hydrocarbon | Wet cleaning |
---|---|---|
Boewe P546 (46-lb) dry-to-dry machine $56,290 |
Boewe K540 (45-lb) dry-to-dry $103,133 |
Miele WS 5190 TR 42-lb elec. washer $32,000 |
Union U2000 P45 (45-lb) dry-to-dry machine $54,975 |
MSG Swiss Clean HC SOL- 25 K dry-to-dry $137,700 |
Miele T 6550 TR 31-lb elec. dryer $8,500 |
Multimatic 45-lb Shop star with all environmental options $48,950 |
MSG Swiss Clean HC SOL- 35 K dry-to-dry $163,500 |
IPSO HF 145 30-lb washer $13,930 |
Boewe Consorba large regeneratable carbon bed $16,000 |
SATEC KWL, Model 250.01 Conc. Control 15 K dry-to-dry $89,300 |
IPSO HF 234 50-lb washer $16,473 |
Boewe PMS 2000 Infrared PERC monitor $12,700 |
SATEC KWL Model 101.11 N2 controlled 20 K, transfer $105,700 |
IPSO ADS30 30-lb dryer $2,715 |
Boewe emission-free still cleaning device $4,403 |
SATEC KWL, Model 181.01 N2 controlled 25 K, dry-to-dry $140,000 |
Electrolux/Wascomat Aquaclean ACS30G 30-lb washer/dryer $25,782 |
Electrolux/Wascomat Aquaclean ACS50G 50-lb washer/dryer $34,590 |
||
UNIMAC UA160W 35-lb washer $11,081 |
||
UNIMAC UA230W 50-lb washer $13,658 |
Wet cleaning may help to keep the white garments whiter. Sometimes white garments can be dulled when cleaned with recycled PERC or other solvents. Also, wet-cleaned garments have a more pleasant smell when compared to the chemical odor associated with garments cleaned in solvent.
There are, however, a number of problems associated with wet cleaning. Garments made of wool, silk, and rayon cannot easily be immersed in water because of possible garment damage from fiber shrinkage or bleeding of dyes. Most problem garments fall into one of the following categories: suit jackets with front fixing in the construction, coats, items with shoulder pads, and ornate clothing. A study conducted by the Hohenstein Institute in Germany showed that for garments made of wool, silk, or rayon, PERC cleaning resulted in considerably less shrinkage than wet cleaning (Figure 21). As much as 50% of wool, silk, and rayon garments used in this study showed unacceptable garment shrinkage during wet cleaning. Furthermore, as these fabrics were repeatedly cleaned in water, the risk of shrinkage became greater (Figure 22). All wool, silk, and rayon garments that were cleaned five times in water had more shrinkage than those cleaned only one time. This was not the case for the same types of garments when cleaned in solvent. Some garments which have shrunk may be stretched back into shape. This can be done using special equipment, which blows warm moist air through the garments and stretches the seams. Unfortunately, it is difficult to restore the garment to its original size and shape.
Figure 21. Shrinkage comparison of woolk silk and rayon graments because of drycleaning and wet cleaning. (Provided by the Hohenstein Institute, Boennigheim, Germany).
Figure 22. Percentage of garments having over 2% shrinkage when cleaned 1 and 5 times in solvent versus water. Provided by the Hohenstein Institute, Boennigheim, Germany).
Another disadvantage of wet-cleaning is the slight fabric deterioration from each cycle. Although some level of deterioration will be observed from any cleaning method, it appears to be more pronounced with wet cleaning. One physical difference between wet-cleaning and PERC-cleaning a garment can be observed under a microscope where wet-cleaned fibers are often seen to swell. Other negative effects on the wet-cleaned garments may include structural surface changes, felting, loss of luster, loss of shape, dye transfer, and/or color change.67
Wet cleaning is very labor intensive and requires a highly skilled and trained workforce. There is a significant increase in the amount of time required to properly press and finish the clothing. Air-dried garments usually have more wrinkles, which in turn, require more pressing. Wet cleaning results are also dependent upon the skill of the spotter.
Wet cleaning produces large quantities of contaminated wastewater. In contrast, solvents used in normal drycleaning are recycled and reused, and small amounts of hazardous wastes are disgarded.
There are several major manufacturers of wet cleaning machines and even more manufacturers of wet-cleaning chemicals. The largest machine manufacturers are Miele®, Electrolux-Wascomat®, IPSO®, and Unimac®. Miele-Kreussler®, two German companies, have conducted extensive research in this area. Approximately 400 systems have been installed in Germany, as well as in several other European countries. Few of these shops perform only wet cleaning.
According to a representative of Kreussler, which is the market leader of wet-cleaning chemicals in Europe, wet cleaning can be used to clean almost any garment. However, Kreussler literature recommends that "Suits, costumes, and highly tailored rayon or linen are examples...for which treatment is simpler and less chancy in solvent."65 While visiting a commercial wet-cleaning shop near Frankfurt, Germany, which did only wet cleaning, NIOSH investigators learned that approximately 25-30% of the garments brought to this shop were cleaned at another facility with solvent.
Wet cleaning today in Europe and the U.S. is limited, but could be used more extensively. In order to be effective, wet-cleaning systems must balance the need for low garment shrinkage, good cleaning results, and reasonable processing times. Based upon observations and discussions with individuals involved in wet cleaning in Europe, the researchers believe technology has not reached the point to completely eliminate the need for solvents. Wet-cleaning shops cannot effectively, efficiently, and repeatedly clean all garments with water. There are still problems with fiber damage; bleeding of dyes; and most importantly, cleaning ability. Inappropriate use of wet cleaning can expose shop owners to liability for damaged clothing. For this reason Kreussler and other wet-cleaning advocates are working to persuade garment manufacturers to use fabrics that can be more easily wet cleaned. These fabrics should not only include the outer part of the garment, but also the threads and internal materials.
Although some advocates have claimed to be able to wet clean 100% of garments, most shops that use wet cleaning also clean with solvents. Many wet-cleaning shops send certain garments to other facilities for solvent cleaning. Several studies report that 30-70% of garments that have been traditionally cleaned in solvent can be safely wet cleaned.65,68,69
New Petroleum-Based Solvents and Machines.—Two different approaches have been followed in Europe to reduce the fire hazard posed by cleaning with petroleum-based solvents: the development of new petroleum-based solvents with higher flashpoints and the redesigning of machines to make them inherently safer.
New petroleum-based solvents, having higher flashpoints, are widely used in Europe and are either straight chain, branched, or cyclic alkanes (or paraffins), having a chain length between ten and twelve carbons. They are colorless, non-water miscible liquids, which have a faint smell of mineral oil and a boiling range between 180° and 210°C (356° and 410°F). These solvents generally contain only trace amounts of polycyclic aromatics. There is little information available concerning toxicological properties and health-related data for these new solvents. Petroleum-based solvents have a lifetime of only a few days, are halogen-free, and do not lead to ozone depletion. Petroleum-based solvents play only a minor role in the greenhouse effect.
The new solvents are being sold under various trade names. Table 11 outlines the solvents that are most widely used and their physical properties. There are approximately ten other similar solvents not listed in Table 11 that are used by less than 1% of the market. Some of the German requirements for petroleum-based, drycleaning solvents are outlined below:70
- Boiling range between 180° and 210°C (356° and 410°F)
- Flashpoint higher than 55°C (131°F)T Aromatic, benzene, halogen, and polycyclic aromatic content less than 0.01 weight percent
- Thermally stable at operating conditions
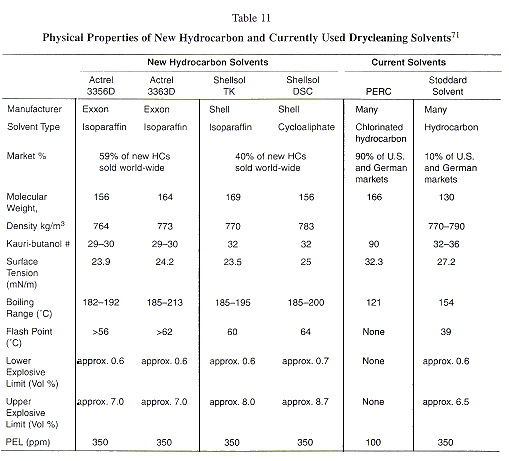
Drycleaning machines manufactured for petroleum-based solvents in Europe today are much safer than those of the past. There have been several technical advances to improve machine safety and reduce the risk of fire and explosion, such as using vacuum technology, or using an inert gas, or controlling the operating parameters of the machine to prevent fire or explosion. The following measures are being used in Germany either in combination or separately:
- Use of an inert gas, such as nitrogen or argon, to displace oxygen and ensure that the oxygen concentration is sufficiently low to prevent combustion (approximately 8%).
- Operation under a vacuum to displace oxygen and lower its concentration to below 8%, if necessary, employing additional safety measures to avoid possible ignition sources.
- Ensuring that the operating temperature remains 15°C below the flash point.
- Ensuring that the vapor concentration remains below 50% of the lower explosive limit (LEL). This may be achieved by controlling operating temperatures or by providing sufficiently high airflow. Air temperature is typically measured behind the condenser and heating units.
In addition to these measures, there are other safety factors which have been considered:
- The control system is designed so that the failure of any part relevant for safe operation does not lead to unsafe conditions.
- If certain limit values are exceeded, measures are automatically taken to shut down the machine.
- The cleaning solvent temperature is automatically monitored at a level determined by the specific solvent being used.
- The oxygen concentration is automatically monitored during the drying process when inert gases are in use.
- The oxygen measuring device is regularly tested and maintained.
Isolation.—Isolation of both equipment and solvents from the worker is used in some drycleaners today and was observed throughout this study. "Isolation" describes the placement of a physical or time barrier between the hazard and the worker. Process isolation can occur in two ways: between shops and within shops. An example of isolation between shops, noted during this study, occurred when businesses utilized "satellite shops," where no drycleaning occurred. Workers at the "satellite shop" were isolated from significant exposures to PERC associated with drycleaning operations. Because the majority of PERC emissions originate from the drycleaning machine, isolating employees by either time or space from the drycleaning machines can reduce worker exposures. Isolation within shops was not frequently used or was used ineffectively at studied shops because appropriate ventilation was absent. Process isolation within shops is more easily achieved in larger shops because they have more space and provide greater flexibility for isolating high exposure processes. Some facilities have built a wall or barrier within the shop to separate the drycleaning machine from other areas of the shop.
The EPA currently requires drycleaning shops with a transfer machine that uses over 1,800 gallons of PERC per year to install a room enclosure and vent the enclosure to a carbon absorber.72 Room enclosures have the potential to increase worker exposures by preventing vapors from rapidly leaving the work environment. Room enclosures are one method to address contamination of adjacent apartment buildings and food stores, situations which have become a problem for drycleaning shops in urban areas. Diffusion barriers, which are impervious to PERC vapors, have been used in Germany to prevent solvent vapors from migrating to adjacent occupancies and affecting neighbors.
Drycleaning Machine Design.—The primary source of exposure to the workers in all shops studied was the drycleaning machine. Real-time evaluation showed that machine loading and unloading had the greatest impact upon exposures. These exposures are directly related to machine design. Operator exposures can be dramatically reduced during loading/unloading by controlling the PERC concentration in the machine cylinder at the end of the dry cycle and by controlling where the air in the machine cylinder goes during loading/unloading. There are basic distinctions between types of drycleaning machines and the physical principles that dictate the level of exposure to expect from each machine design. Those distinctions include the type of vapor recovery system, whether the machine is transfer or dry-to-dry, and whether the machine is vented or nonvented.
The vapor recovery system will determine the concentration of PERC remaining in the cylinder at the end of the dry cycle, and also the amount of PERC remaining in the garments that off-gas inside the shop. The primary vapor recovery technologies are the carbon adsorber and the refrigerated condenser.
Carbon adsorbers can achieve a 95-99% vapor reduction by removing PERC molecules from the air. Solvent-laden vapors pass over activated carbon having a high adsorption capacity. Factors, such as the flow rate of the air stream, concentration of PERC in the air stream, adsorption time, capacity of the carbon bed, humidity, temperature of the air stream, and/or condition of the carbon, all affect adsorption. Generally, airflow rate and carbon bed capacity are the most important factors.73
Carbon adsorption systems can handle high volumes of air with relatively low solvent concentrations and maintain a high removal efficiency. The drawbacks are the need for frequent desorbing, the possible generation of solvent contaminated wastewater, and the potential for high emissions and exposures if the carbon is not properly maintained. This study found that many machine manufacturers are using carbon improperly, and many machines currently used in the U.S. are equipped with small carbon canisters containing 1- to 2-lb of carbon to purge the air in the machine cylinder at the end of the dry cycle. The poor vapor recovery system design permits the effluent to enter the work environment after passing through an inadequately sized carbon canister.
Theoretical calculations, based on the design of one machine studied, indicated that at least one-tenth of a pound of carbon was needed per load, if the concentration in the cylinder was 2,000 ppm when the fan activated.27,73,74 The machine had a 17 cubic foot cylinder and contained approximately 0.96 liters of PERC (gas phase) or 6.47 grams of PERC. With an average of eight loads per day, the quantity of activated carbon currently used (1-2 lb) should have been changed on nearly a daily basis to be effective. At the shop evaluated, the carbon in the canister was changed monthly or even less frequently.
Even if there had been sufficient carbon in the canister and the machine had operated at optimal efficiency, the PERC effluent would have tended to remain in the 50-150 ppm range. This concentration translates to approximately 95% to 99% efficiency. When the working capacity of the carbon is approached, breakthrough occurs and the concentration of PERC in the effluent stream increases dramatically. Even if the carbon canister were operating at optimal efficiency, the design of the secondary vapor recovery device would have permitted PERC-contaminated air to be exhausted into the work environment.
The second type of vapor recovery system, the refrigerated condenser, uses a refrigerant to cool the solvent-laden air below the dew point of the vapor to recover the PERC. Refrigerated condensers operate on the principle that the ability of air to hold a solvent in the vapor state is based on the temperature. The process can achieve 95% vapor control in dry-to-dry machines and 85% control in transfer machines. The residual concentration is reduced to the saturation concentration, based on the temperature and air volume. The lowest condensation temperature is -22°C (-8°F); however, in practice, machines operate at a minimum of -20°C (-4°F). At this temperature the air still contains approximately 2,000 ppm, although concentrations could be higher depending on air temperature (Figure 23).
Figure 23. Concentration of PERC saturated air.
Condensers require little maintenance and minimize the potential for wastewater because steam regeneration that is used on many of the old carbon adsorption technologies is not required for the refrigeration technology. However, the refrigeration technology generally only reduces the PERC air concentration to about 2000 ppm, whereas, the carbon adsorption technology can reduce the PERC air concentration to below 200 ppm. Water vapor which is present in the air during solvent recovery may also pose a problem because it can condense and freeze, impeding gas flow and heat transfer.75
Drycleaning machines are generally configured in one of three ways: drycleaning machines without refrigeration technology, drycleaning machines with refrigeration technology, and drycleaning machines with both refrigeration and carbon adsorption technology. In drycleaning machines without refrigeration technology, the exhaust air is adsorbed by an activated carbon air filter. During the drying process, air is conducted in a circuit through a fan, water-cooled air cooler, air heater, cage, and lint filter. The solvent vapors condense on the recovery condenser and flow to the water separator. Air from the recovery condenser has a temperature of approximately 30°C (86°F) and will only reduce solvent concentrations in the machine cylinder to approximately 30,000 ppm. Concentrations could range from 25,000 to 75,000 ppm, depending upon cooling water and air temperatures. It is then heated in the air heater to absorb new solvent from the load. After this, the air passes through the lint filter and is conducted to the fan.
The drying temperature, 50 to 70°C (122 to 158°F), is regulated by a variable thermostat that switches a steam control valve on or off. A thermostat controls the temperature behind the air cooler. Drying is considered finished when the solvent behind the air cooler has been reduced to such a concentration that any further expenditure of time and energy would be inefficient. At the end of the drying process, fresh air is drawn in through a trap. Air passes through the load to the carbon adsorber. The blow-out process takes place when the machine is loaded and unloaded. The fan draws air and gaseous solvent in through the loading door to minimize worker exposure.
On machines having refrigeration technology, the air cooler is connected to a refrigerated condenser and operates at considerably lower temperatures than a water-cooled condenser. Two air heaters are used instead of one. The more powerful one is fed with hot gas from the refrigeration unit. The remaining heat is supplied by a small auxiliary electric or steam heater. At the end of the drying process, the air contains substantially lower quantities of PERC than a water-cooled condenser (approximately 2,000 ppm). The solvent concentration depends on the temperature and air volume. On these machines the blow-out phase is not used. Small quantities of air escape from the machine during loading and unloading.
"Fifth generation" machines having refrigeration and carbon adsorption technology. Lowered cylinder concentrations are extremely important for reducing TWA exposures to PERC, as shown by the air sampling and real-time results of this study.27 Very low exposures and emissions can be accomplished by using both a refrigerated condenser and carbon adsorber. The two technologies used together are more effective than alone. Both technologies were used in the state-of-the-art "fifth generation" drycleaning machines that were evaluated.
Figure 24 depicts how the PERC concentration in the cylinder of one such machine is reduced during the vapor recovery process. During the main drying cycle, the solvent-laden air recirculates through the refrigerated condenser, which condenses and recovers most of the residual solvent. While passing through the cooling coil, PERC vapors condense and flow to the separator where water is removed. Liquid PERC flows back into the machine tank. A drying sensor, which measures temperature change or solvent flow between the refrigerated condenser and water separator, automatically switches the system to the cool down/deodorize step. During this part of the cycle, the air is cooled in the refrigerated condenser before passing through the carbon absorber and returning to the drying drum.
Figure 24. PERC cylinder concentration during the vapor recovery process of a "fifth generation" drycleaning machine. (Used with permission of Boewe Passat, Wichita Falls, Texas.)
Several other technologies are used to ensure low cylinder concentrations. A single beam infrared photometer continuously monitors the PERC concentration in the machine cylinder and in the work environment. An interlock on the machine door ensures that the drying/vapor recovery process continues to operate until the PERC concentration in the cylinder is below 290 ppm. The carbon adsorption system is automatically desorbed by hot air during the subsequent dry cycle. Hot air desorption as opposed to steam desorption eliminates retention of water vapor in the carbon, an event that adds to the hazardous waste produced in more traditional equipment.
Figure 25 depicts the significant vapor recovery components of a "fifth generation" PERC drycleaning machine. This study found that "fifth generation" PERC machines can easily reduce TWA worker exposures to PERC to below 5 ppm.46,76 Table 12 outlines the significant features of the "fifth generation" PERC equipment and the German regulations requiring that feature. Figure 26 depicts how personal exposures to PERC have fallen from 1990 to 1994 in Germany because of the widespread use of "fifth generation" drycleaning machines that began to be required in that country during that time.
Table 12: Drycleaning Machine Design Requirements from German Law
Legal Requirement | Law | Features |
Emission-free solvent filling of machine | 2nd BImSchV | Limits solvent emissions No open handling of solvent Filling with machine's pump |
Still tank rinsing | 2nd BImSchV | Automatic flushing of still tank walls |
Emission-free still rake-out | 2nd BimSchV | Completely closed system automated pumping and steaming |
Cooling water temperature control | 2nd BImSchV | Cooling water temperature maintained below 45°C |
Waste water contains less than 5 mg/m3 solvent | VBG 66 ISO 8230 |
Double water separator |
Maintenance protection with limit switches | VBG 66 ISO 8230 |
Safety switches on still, button trap, and loading door |
Solvent safety trough below machine | VBG 66 ISO 8230 |
Volume contains 110% soil/groundwater protection |
Less than 2g/m3 or 290 ppm in cylinder at end of dry cycle | 2nd BimSchV | Refrigerated condenser and carbon bed in series Infrared detector measures concentra tion in drum |
Only regenerable filters permitted | 2nd BimSchV | Nylon, ECO-filters |
Regenerable activated carbon for adsorption at end of dry cycle> | 2nd BimSchV | Automatic hot air/steam adsorption with each load |
Figure 25. Flow diagram and major components of a "fifth generation" drycleaning machine.
Figure 26. Percentage of PERC samples in German drycleaning shops at various concentrations from 1990 to 1994. (Provided by the Hohenstein Institute, Boennigheim, Germany.)
Transfer and Dry-to-Dry Machines. Most federal and state regulations do not require the use of dry-to-dry machines; however, a few states such as California and New York have begun requiring all new machines to be dry-to-dry. Many shops have replaced transfer machines with dry-to-dry machines because of stricter air regulations; however, some shops still use the transfer equipment for increased productivity and to avoid the cost of new machines.
In the evaluated transfer equipment, the greatest operator exposures occurred during loading/unloading the machines and garment transfer. Exposures during this procedure frequently reached instantaneous concentrations between 1,000 and 1,500 ppm. Operator exposure could be reduced by more than half by eliminating exposure during these activities. This reduction can be seen by determining the operator TWA integrated exposure in ppm*seconds during the workday from air sampling (25,200 sec * 19.5 ppm = 491,400 ppm*sec) and comparing the TWA integrated exposure to the operator's total exposure during loading/unloading and transfer from real-time measurements (25,370 ppm*sec * 10 times/day = 253,700 ppm*sec/day).
During the evaluation of transfer equipment, it was seen that loading was responsible for a greater average exposure than unloading. Surprisingly, average PERC exposure during the transfer operation was not as high as average PERC exposure from loading/unloading some of the dry-to-dry machines studied at other shops. This could be attributed to the fact that the garments being transferred have not been heated, and the reclaimer had greater door ventilation than many dry-to-dry machines.
Dry-to-dry machines eliminate exposures from the transfer operation. Data from the International Fabricare Institute has indicated that since 1989 TWA worker exposures from dry-to-dry machines were less than half of those from the transfer equipment.77 The IFI data seems to contradict some of this study's findings because the data from this study reported only a small difference between the transfer machine and the dry-to-dry machines, but there is a plausible explanation. Part of the exposure difference may be due to the fact that transfer machines are typically older than dry-to-dry machines and because they are older, they may have more leaks which would account in part for the higher exposures reported in the IFI study. Additionally, statistical variance may play a significant role. This study had a more limited sample size than the IFI study.
Vented and Nonvented Machines. Environmental regulations have played an important role in affecting machine design. Transfer machines were first replaced by dry-to-dry machines, vented directly to the atmosphere. Unfortunately, these machines permitted significant concentrations of PERC to enter the atmosphere, which may be harmful to the environment. Dry-to-dry, nonvented equipment was later introduced to help reduce the significant environmental emissions of PERC that occurred from venting. Machine designers thought that the simple solution was to eliminate exhaust air.
Unfortunately, there are still significant concentrations of PERC in the drum at the end of the dry cycle, which can cause high worker exposures. Internal ventilation can be an extremely important component of machine design. Ventilation determines where the air in the machine cylinder is directed during loading and unloading. Air in the machine cylinder is always contaminated with PERC to some degree, and it should not be allowed to escape directly into the worker's breathing zone. This contaminated air should also not be exhausted behind the machine, or into the work environment. Rather, the contaminated air should be captured and exhausted outside the work environment.
In a nonvented dry-to-dry machine, greater exposures often occur during loading than during unloading. Because the machine cylinder has not been evacuated immediately prior to loading, the residual PERC vapors, having diffused into the cylinder, are ejected when the garments are loaded, as shown by the airflow patterns, not only exposing the operator but also diffusing throughout the building. This air displacement rapidly increases PERC concentration in the operator's breathing zone, an almost instantaneous peak, which in the NIOSH study approached 2,000 ppm. The concentration in the worker's breathing zone dissipates over the next 10 to 20 seconds and then returns to background.
At one shop evaluated, operator exposure could have been reduced by two-thirds by controlling the exposure during loading and unloading. The operator's TWA exposure during the workday, based on air sampling data, was 270,000 ppm*sec (17,040 seconds * 15.82 ppm), whereas the exposure during loading/unloading, using real-time data, was 184,100 ppm*sec/day (23,010 ppm*sec * 8 times/day). If exposure during loading/unloading were reduced near zero, then the operator's total 8-hour TWA exposure would be reduced from approximately 15.8 ppm to approximately 5 ppm, and more importantly, the peak exposures of approximately 1,500 ppm would be eliminated. At another shop evaluated, a small centrifugal fan used as a secondary control, provided inadequate airflow to prevent vapors in the cylinder from escaping into the operator's breathing zone.
Other Machine Options. Other technologies that reduce occupational exposures to PERC include the following: emission-free still cleaning devices that produce less waste; regenerable solvent filtration systems that eliminate the need to handle spent cartridges; emission free solvent filling devices; automatic regenerable carbon adsorbers; seals and fittings that have tighter tolerances, resisting deterioration; process controls that lower garment residuals after the drying process; and controls that reduce vapors escaping from the button and lint traps.
Emission-free still cleaning and regenerable solvent filtration systems are required on machines in Germany. On most drycleaning machines in the U.S., still doors are commonly opened, and still bottoms are raked out into an open catch basin. On the most advanced machines, still bottoms are either raked out through a small hole in the wall of the still, which is enclosed with a seal and gasket, or still bottoms are pumped out. In order for still bottoms to be pumped out, they must be fluid and have minimal solids. Filter powder is a significant source of still bottom solids.
Spin-disc filters have become standard equipment on modern machines because of the expense to dispose of hazardous waste and associated emissions and exposures. Spin-disc filters consist of approximately 36 15-in. diameter discs made of a polyester fine mesh mounted on a center support. These double-walled discs have a total of approximately 85 ft2 of surface area. The solvent flows through the filters and out through the center shaft. Soils collect on the stationary disc, and when the pressure differential across the disc reaches approximately 22 pounds per square inch gage (psig), the filters are regenerated by spinning the discs and directing the solvent, soils, and sludge out through a drain valve and to the still.78 Spin-disc filters reduce the solids in still residue and reduce the quantities of hazardous waste produced. Each of the previously mentioned options will help to reduce exposures; however, the most effective options reduce exposure during loading and unloading.
Several safety items can be found on well-designed drycleaning machines. The machine's loading door and other doors for machine maintenance can be fitted with a safety switch to prevent the machine from being started or continuing to operate if the door is not completely closed. Some machines are equipped with safety interlocks to stop the machine if the heating or cooling system for the dry cycle or the still fail. These machines remain in a fail-safe condition until the malfunction is corrected.
Machine Retrofits.—Shops that are unable for economic reasons to replace equipment without advanced controls can take other less expensive measures to reduce exposures. Machine retrofits, which are available through local distributors, will generally be one of two types: a refrigerated condenser or a carbon adsorber. A refrigerated condenser could be retrofitted on any machine that is currently using a water-or air-cooled condenser for solvent recovery/drying purposes. A carbon adsorber could be retrofitted on a drycleaning machine that has only a refrigerated condenser or only a small carbon canister containing one or two pounds of carbon. The carbon adsorber should ideally have a large bed of carbon (approximately 50-60 lb or more) and be automatically regenerable. Modern carbon adsorbers produce minimal hazardous waste during regeneration, and the solvent captured by the carbon is recoverable using the machine's refrigerated condenser.
Ventilation.—Many of the evaluated ventilation systems appeared to have been designed more for thermal comfort than for reduction of worker exposure to PERC. This may be attributed to the more obvious effects of thermal discomfort, (fatigue, irritability, etc.). Workers are often unaware of chronic vapor exposures because of desensitization. Furthermore, unlike ventilation for comfort, ventilation to reduce air contaminants does not always affect productivity.
Local exhaust ventilation is a relatively inexpensive control option that attempts to capture contaminants before they escape into the work environment. Local exhaust ventilation is effective because it captures solvent vapors where they are most concentrated, at the source. This prevents vapors from reaching the worker's breathing zone and reduces diffusion throughout the plant. Hood modifications, such as a flange placed on a slotted hood which isolates the capture area from strong air drafts, can improve performance.79
External, local exhaust ventilation could be installed near the loading/unloading door of the machine to capture solvent vapors that escape from the machine. Ventilation systems that are installed should be designed in accordance with guidelines established by the National Fire Protection Association (NFPA) or Michigan Department of Public Health. NFPA codes for the drycleaning industry recommend drycleaning machines that have an integral exhaust system and a door face velocity of 100 fpm. These guidelines have become the widely accepted practice in the industry for machines which utilize ventilation.5,57 An alternative is a ventilation hood placed outside the machine door and an airflow capacity in cfm, not less than 100times the door opening area in square feet.8
Local exhaust ventilation consisting of an exhaust fan, duct work, and hood can significantly reduce exposures. The captured air is then ducted outside the building or to a vapor recovery unit. Exposures during unloading have been shown to be reduced from 1,000 ppm to 28 ppm by having a fan that operated at 990 cfm and a slotted hood design.80
General dilution ventilation can reduce contaminant concentrations that are not controlled locally by adding fresh air or removing air to dilute contaminant concentrations below a specified level. To be effective, the quantity of contaminant must be relatively low, the production of the contaminant must be relatively uniform, the contaminant must have a low toxicity, and workers must be a reasonable distance from the source. Because these conditions are not met during loading and unloading, dilution ventilation is not the best control for this exposure. Replacement air enters naturally through windows and doors or through large fans in the ceiling or walls. Fans should pull fresh air through the cleaning area and draw vapors away from the workers prior to exhaust. This airflow reduces the movement of contaminated air into other areas of the shop. The American Society of Heating, Refrigerating, and Air-conditioning Engineers (ASHRAE) standard for acceptable indoor air quality recommends a minimum of 30 cfm per person for commercial drycleaners.81 Emergency ventilation systems have been used to control spills and leaks.
Administrative Controls.—Substitution, isolation, effective machine design, and ventilation are preferable to the following administrative controls because the former either eliminate use of PERC or prevent the escape of vapors from the machine itself. However, while less effective, administrative controls, such as maintenance and monitoring, can be used to reduce the vapors that reach the workers' breathing zone.
Maintenance procedures and schedules varied among the evaluated shops, and written maintenance plans were generally lacking. The procedures should be developed by knowledgeable persons who consider the equipment manufacturer's recommendations, frequency of use, and other circumstances that might affect the integrity of the equipment. The maintenance should include regular checks of door gaskets, valves, tubing, and piping connections. Maintenance workers should wear proper personal protective equipment to prevent skin or inhalation exposures. In order for respirators to be beneficial, they must be properly used, and a written respirator program must be in place. Maintenance workers should be aware of potential sources of PERC exposure.
Solvent exposures that occur during maintenance activities on drycleaning equipment can be substantial, as shown with real-time monitoring. Because of lower frequency, it is less of a problem than exposure during loading/unloading the machines or the hanging of garments.
Another control is routine monitoring. Routine monitoring of the drycleaning equipment and the work environment can help to ensure the continued effectiveness of other control measures. Continuous monitoring was used on the evaluated "fifth generation" drycleaning machine, while other shops performed periodic leak checks or air monitoring, using passive air monitoring or leak detection equipment. Each of these approaches to monitoring will reduce exposures to PERC.
Respiratory protection is the least preferred method for controlling worker exposure to PERC, and as such is seldom the only means recommended for controlling exposure. Required written respirator programs provide an evaluation of the workers' abilities to perform their jobs while wearing a respirator, regular training of personnel, periodic environmental monitoring, and respirator fit testing. All but one of the evaluated shops was lacking in this area.
Cost of New Drycleaning Machines
One of the most important aspects of each technology is the capital investment required for each type of equipment. Each of these technologies are significantly different and cannot be interchanged (for instance, petroleum-based solvents cannot be used in a machine designed for PERC, and PERC cannot be used in a machine designed for wet cleaning). Therefore, if a shop owner has been cleaning with PERC and wants to clean with petroleum-based solvents, he/she will have to purchase new equipment. Many large shops having available capital can afford to own several types of machines, but this same economic freedom is not necessarily true for smaller shops. Table 10 outlines the costs of various types of equipment and equipment features. Cost of equipment is only one minor aspect of the total cost to a business from acquisition of new technologies. Other important aspects include solvent costs, hazardous waste disposal costs, labor costs, water and sewer costs, and utility costs. A rigorous economic analysis of these alternative processes is beyond the scope of this report.
Recommendations
Occupational exposures should be controlled by the application of many well-known principles, including engineering measures, work practices, and personal protection. In order to reduce exposure to drycleaning solvents, a comprehensive control approach should be followed which addresses all of the appropriate control options. Engineering measures are the preferred and most effective means of control and should generally be considered first. These include material substitution, process and equipment modification, isolation and automation, and local and general ventilation. Control measures also may include good work practices and personal hygiene, housekeeping, administrative controls, and use of personal protective equipment, such as respirators, gloves, and goggles. Table 13 summarizes the principles and methods of controlling occupational health hazards.
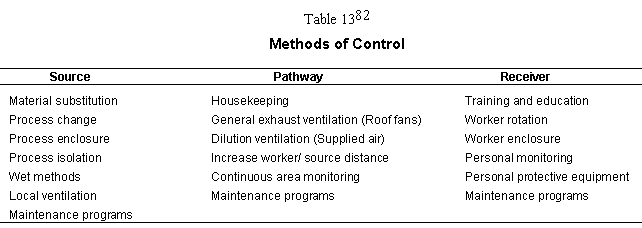
Each of these approaches must be considered when developing a comprehensive, effective control strategy; however, their optimum application varies from case-to-case. Substitution and design modifications are the preferred method of control because their effectiveness is generally not dependent on human behavior. Additionally, monitoring and maintenance of controls, training/education, and commitment of both management and employees are all important ingredients of a successful control system.
Substitution Recommendations
Substitute technologies are currently available to dramatically reduce occupational exposures to PERC in the U.S. commercial drycleaning industry. Advanced "fifth generation" drycleaning machines and alternative cleaning media, such as petroleum-based solvents/machines and wet cleaning, are currently available, effective, and widely used in Germany. Greater use of these alternatives in the U.S. would reduce occupational exposures to PERC, just as has occurred in Germany. Although the alternatives are promising, they are not without cleaning quality concerns. Primarily, some fabric deterioration is increased by wet cleaning, a problem that is still being addressed. These alternatives may also have their own set of safety and health concerns.
Use of alternatives to PERC is not necessarily an all or nothing proposition, especially for larger shops with more capital. For many shops, substitutes should be considered to complement rather than compete with PERC use. Shops that reduce the quantity of garments cleaned in PERC will experience a corresponding drop in PERC exposures. Most experts agree that a minimum of 30% of the garments currently drycleaned could be wet cleaned, and others suggest a much higher percentage. As research and development in this area continues, the percentage of garments that can be safely wet cleaned could go much higher. U.S. shop owners should increase their use of these alternatives to reduce occupational exposures to PERC.
Isolation Recommendations
All shop owners and managers should consider process isolation. On a macro scale, large drycleaning shops with multiple stores should think about using satellite shops which do not perform drycleaning on the premises. Isolation between shops is already being done by many larger shops, and this trend should continue in the future. Use of satellite shops has the effect of increasing turn-around time because the garments must be transported to and from the main shop. However, most customers are willing to wait a day or two to have their garments professionally cleaned. When opening a new shop, owners should attempt to locate in stand-alone buildings when possible. This will reduce the risk of contaminating adjacent apartment buildings and food stores, sometimes a significant problem when facilities share a common wall.
Within each shop, the drycleaning machines should be isolated from other work areas. Because the majority of PERC emissions originate at the machine, isolating employees from the drycleaning machines by either time or space will reduce exposures to those employees. In order to be effective, process isolation should be used in conjunction with good local and general ventilation.
Machine Design Recommendations
To reduce exposures during loading and unloading on traditional drycleaning machines, improved ventilation is needed to increase airflow and capture the residual PERC escaping from the cylinder. Additionally, a large carbon bed that is capable of repeatedly capturing the high concentrations of PERC that remain in the cylinder at the end of the dry cycle would improve PERC capture efficiency. Finally, machines that provide any exhaust ventilation should terminate outside the shop rather than inside. This will ensure that any remaining effluent will not expose workers.
Drycleaning shop owners should purchase the most advanced drycleaning machine that the budget allows because modern designs can reduce TWA exposures to PERC to less than 5 ppm, the shop owner will save money in solvent costs, and the facility will more easily comply with safety and health/environmental regulations. Ideally, shop owners should strive to purchase "fifth generation" machines. The most important component of a drycleaning machine is a vapor recovery system, which has both a refrigerated condenser and a large carbon adsorber. However, there are many options that will further reduce exposures. A detailed discussion of machine design considerations is included above in the Overall Control Strategy section.
Maintenance Recommendations
Proper maintenance procedures should be used to reduce PERC exposures during drycleaning in two ways. First, maintenance should be done properly to prevent the drycleaning machine's performance from degrading, which might result in increased solvent exposures. Increased exposures may occur through less efficient solvent recovery or solvent vapor/liquid leaks. Second, worker exposures to PERC should be controlled during maintenance activities, and proper procedures are important in reducing these exposures.
Poor machine maintenance will eventually result in increased emissions and exposures. This study examined several common maintenance activities and evaluated exposures during those activities. Table 14 lists common maintenance activities and their recommended frequency. These frequencies apply to the majority of machines, but can vary depending upon machine design. When manufacturers' maintenance recommendations are available, they should be consulted.
Table 14: Recommended Maintenance Schedule for Drycleaning Machines 86
Component | Frequency | Maintenance Procedures |
Machine cylinder | Weekly | Leak check door seatings and gaskets |
Monthly | Leak check exhaust damper (vented) | |
Heating/condensing coils | Monthly | Check for lint build-up |
Annually | Clean coils | |
Button trap | Daily | Clean strainer |
Weekly | Check for lid leaks | |
Lint trap | Daily | Clean lint bag |
Weekly | Launder lint bag | |
Monthly | Check ductwork for leaks | |
Monthly | Check lint build-up on temperature probe | |
Filters | Demand | Clean and change |
Distillation unit | Daily/Weekly | Rake out still |
Weekly | Leak check seals/gaskets | |
Muck cooker | Semi-annually | Clean steam and condensation coils |
Water separator | Daily | Dispose of contaminated water |
Weekly | Clean separator tank | |
Monthly | Check vent | |
Refrigerated condenser | Weekly | Measure exhaust temperature |
Weekly | Leak check seals, gaskets, diverter valve | |
Monthly | Check coils for lint build-up | |
Annually | Clean refrigerant coils | |
Carbon adsorber | Daily | Desorb |
Weekly | Measure PERC in exhaust stream | |
Monthly | Leak check gaskets and ducts |
Owners and operators should pay particular attention to maintenance activities that reduce solvent losses, a potential source of worker exposure. Maintenance activities which are particularly important in reducing solvent exposures include ensuring vapor recovery systems are in good working order and checking for liquid/vapor leaks on equipment piping, ductwork, and the machine. Solvent recovery efficiency should be measured at least twice a year or as frequently as needed to achieve reliable performance.83 Proper operation and maintenance of the vapor recovery system is imperative for maximum solvent recovery. Poor reclamation efficiency can be caused by inadequate condenser temperatures, inefficient carbon adsorption, dirty lint traps, clogged condenser or heating coils, leaky door gaskets, leaky inlet or exhaust dampers, clogged solvent drain from separator, clogged air vent in separator, and improper fan operation.84
Equipment should be maintained in accordance with manufacturer's recommendations. An important operating parameter for water-cooled condenser temperature is typically 29°C to 32°C (84°F to 90°F), and for a refrigerated unit is typically 13°C to 16°C (55 °F to 61°F). The temperature of air leaving the clothes should typically be 57°C to 63°C (135°F to 145°F) for a regular cycle and 49°C (120°F) for a fragile load.85
Carbon adsorber beds should be regularly desorbed according to manufacturer's instructions. Modern machines desorb their carbon beds automatically, having no production of hazardous waste; however, there continues to be significant quantities of the less advanced adsorbers in use. It is better to desorb the bed early than to lose solvent and increase exposures because of late desorbing. If the machine has an exhaust stack inside or outside the shop, the exhaust should be monitored during the exhausting process. Operators can track the weight of clothing cleaned to determine when the adsorber should be desorbed. If a small carbon canister is used as a secondary control, the carbon should probably be changed on a daily basis. If steam is used for desorption, the bed should fully dry in order to restore the adsorption capacity.
Steam and condensing coils in the still should be kept free of scale and hardened residues. For minimal solvent content in the still residue, the still should be operated according to manufacturer's instructions. Steam sweeping or air sweeping above the still residue at the end of the distillation process may reduce solvent content to approximately 5 weight percent. If possible, still bottoms should not be exposed to the atmosphere, and they should be properly stored in approved, sealed, and labeled containers. Owners/operators should have the solvent content of still bottoms analyzed regularly to determine solvent loss and still performance. The IFI has estimated PERC content in still residues for a range of densities at room temperature.84 Still maintenance on open systems should only be performed under cold conditions.
Leak checks should be performed daily, and if found, leaks should be repaired immediately. Fugitive emissions result from liquid and vapor leaks, which are strongly influenced by maintenance practices. Leaks can be stopped by repair or replacement of the gasket material at the point of occurrence. Small fugitive losses can occur in the most well-maintained system from slight imperfections in the sealing surface of joints and fittings, and from vents or door openings on older machines.84
Ventilation Recommendations
Ventilation should be used to control worker exposure to PERC, in addition to ensuring thermal comfort. Thermal comfort and reduction of worker vapor exposure are both extremely important in drycleaning shops, but a greater emphasis should be placed on ventilation to reduce chemical exposures.
Ventilation is most effective in reducing drycleaning exposures when used as one component of an overall control strategy. Control techniques that eliminate or reduce PERC use or prevent vapors from escaping from the machine should be employed first. Ventilation does not eliminate vapors; rather, it can prevent vapors from reaching the worker's breathing zone. Ventilation is an important technique that should be considered for improving and maintaining the quality of air in the drycleaning work environment. Ventilation control should be accomplished by capturing and removing the contaminant at or near the source (local ventilation), or diluting the concentration of the contaminant before it reaches the worker's breathing zone (general ventilation). Local ventilation prevents vapors from reaching the worker's breathing zone, as well as reduces diffusion throughout the plant. Local ventilation could best be used in drycleaning shops to reduce worker exposure during loading/unloading the machine and performing maintenance.
Drycleaning shop owners should use local exhaust ventilation in accordance with appropriate guidelines. NFPA codes and Michigan Department of Public Health Rules recommend drycleaning machines with an integral exhaust system having an inward air velocity through the loading door of 100 fpm.5,57 The Michigan rules call for the blower to be ducted to a point 5 ft above the roof. A face velocity of 100 fpm will help reduce solvent vapors escaping into the shop by providing a draft of clean air that passes over the items being removed from the machine. Placing the exhaust 5 ft above the roof helps to prevent the vapors from reentering the work environment. Integral exhaust systems are typically activated by a door interlocking switch. An alternative to an integral exhaust system is an external ventilation hood outside the machine door, having an airflow capacity in cfm of not less than 100 times the door opening area in square feet.49 This type of system could best be used for transfer or dry-to-dry, nonvented units. Hood modifications, such as placing a flange on a slotted hood to reduce turbulence and isolating the capture area from strong air drafts, can improve performance of an external system. Local ventilation systems should ideally be passed through a control device to recover solvent vapors.
General ventilation should be used to add fresh air or remove air to dilute background PERC concentrations. NFPA codes and Michigan Department of Public Health Rules recommend an air change in the workroom every 5 minutes.5,57 Replacement air enters naturally through windows and doors or through large fans in the ceiling or walls. Fans should pull fresh air through the cleaning area and draw vapors away from the workers prior to exhaust. This reduces movement of contaminated air into other areas of the shop. Emergency ventilation systems should be available to control solvent vapors if a solvent spill or leak occurs.
Waterproofing Recommendations
Dip-tank waterproofing should ideally be eliminated. Equipment is now available to perform waterproofing inside the drycleaning machine. In most shops, waterproofing is performed infrequently on an as-needed basis. When dip-tank waterproofing occurs, it is a significant source of exposure. Shops not able to purchase drycleaning machines that permit waterproofing inside the drum should ensure dip-tanks have adequate local exhaust ventilation and that proper respiratory protection and gloves are used.
Work Practice Recommendations
Exposure to PERC can be reduced by proper work practices. Good work practices are more important in reducing exposures near more traditional, less automated drycleaning machines than near more modern drycleaning machines. Many of the modern machines have design features that will compensate for poor work practices, which may cause high exposures. For example, operators should not exceed the machine's rated capacity, shorten the drying cycle, or open machine doors while the machine is operating because each of these activities will increase worker exposure. Modern "fifth generation" machines are designed so that the dry cycle cannot be shortened and if the machine is overloaded, the dry cycle will run longer to compensate. Furthermore, many of the machine doors are locked and cannot be opened while the machine is in operation. The following is a list of recommendations related to proper work practices:
- Solvents or hazardous waste should never be left standing in an open container.
- Drycleaning machines should never be loaded beyond the manufacturer's capacity rating. Drying times and temperatures should be regularly monitored.
- All ventilation systems within the drycleaning room should be operating when the drycleaning machine is in operation.
- All forms of machine maintenance should be performed when the machine and solvent are under cold conditions. Machine maintenance, such as cleaning the button/lint trap, should never be performed when the machine is in operation.
- Machine maintenance should be performed on a routine basis, in accordance with machine manufacturer's guidelines.
- All doors on drycleaning machines should be opened for a minimal amount of time.
- Leak checks should be regularly performed, and any leak that is identified should be immediately repaired.
Personal Protective Equipment Recommendations
Though not recommended by NIOSH because PERC is a potential human carcinogen, the respirators found at the shops studied (half-mask face piece with organic vapor cartridges) and used for short-term exposures to low concentrations of PERC must have the cartridges changed prior to breakthrough (approximately 130 minutes based on average room concentrations).87 Regular cartridge changes are important because the odor threshold of PERC is 27 ppm, and a worker may not smell PERC until significant breakthrough and exposure have occurred.4
When employees must wear respirators, an appropriate written respiratory protection program in accordance with 29 CFR 1910.134 must be instituted. This regulation contains provisions for:
- a written standard operating procedure.
- respirator selection based upon hazards.
- instruction and training of the user concerning the proper use and limitations of respirators.
- regular cleaning, disinfection, and proper storage.
- medical review of the health and condition of the respirator user.
- use of certified respirators, which have been designed according to standards established by competent authorities.79
It is recommended that at a minimum, operators should use proper respirators and gloves during machine maintenance and waterproofing operations. Additionally, because of extremely high exposures during loading and unloading of most machines, it is recommended that respirators be worn during this activity in cases where controls have not yet been implemented to reduce peak exposures to below 300 ppm.
Gloves and goggles should be used to reduce exposure to PERC during machine maintenance or other activities where the skin may come in direct contact with solvent. Gloves provide limited dermal protection and should be made of solvent-resistant materials, such as Viton® fluoroelastomer, polyvinyl alcohol, or unsupported nitrile. When a specific glove is chosen, factors such as permeation, durability, dexterity, and cost should be considered. Viton® and polyvinyl alcohol have a PERC breakthrough time in excess of 8 hours.88 A 1987 study showed that unsupported nitrile was impervious to PERC after a 2-hour challenge period.89 Some of the drawbacks associated with these materials are that Viton® is expensive, polyvinyl alcohol significantly reduces dexterity, and unsupported nitrile has a higher permeation rate than Viton® or polyvinyl alcohol. Whenever swelling or softening of the gloves or seepage of PERC into the glove is observed, the gloves should be replaced. Gloves should also be regularly checked for perforations and cuts.
Chemical splash goggles should be worn to prevent eye injury when workers are using PERC or other hazardous chemicals. Use of chemical splash goggles is particularly important during machine maintenance operations, waterproofing, and spotting. An eye wash station should be located near the drycleaning machine and the spotting station.
Control of Chemical Exposures From Spotting
Case Study
The spotting process was evaluated at several shops using limited air sampling and qualitative analysis. One detailed in-depth evaluation was conducted at a single, large, commercial drycleaning shop. Spotting agent vapors used at this shop were irritating some employees, and an OSHA complaint was filed as a result. The workers suffering irritation worked in proximity to the pre-spotting station where the evaluation occurred. Conditions at this shop were probably worst case.
Water-soluble stains that could set during the drycleaning process (rendering them more difficult or impossible to remove later) were sent to the pre-spotting station for treatment. Post-spotting was used for stains not completely removed after drycleaning. Post-spotting was much more time intensive and involved the use of a spotting board equipped with pressurized air, steam, and water guns.
Four spotting agents were used during the evaluation: Pyratex®, Picrin®, Two-in-one®, and Wetspo®. Pyratex® is primarily methyl isobutyl ketone (MIBK), n-butyl acetate, and 2-butoxyethanol. Picrin® is primarily trichloroethylene. Two-in-one® is a mixture of trichloroethylene, hexylene glycol, and diacetone alcohol. Wetspo® is primarily composed of PERC. Pyratex® is used for collar stains and grease, oil, ink, and paint stains; it is mainly used for tough stains on durable garments. Picrin® is used to remove paints. Two-in-one® is used for light oil and grease stains. Wetspo® is used for ink stains. On an average day, the spotter used 48 oz of Pyratex®, 24 oz of Two-in-one®, 6 oz of Wetspo®, and 6 oz of Picrin®. The spotter also used approximately 4 oz of PERC per day to check for fabric colorfastness.
Spotting occurred in a room that was approximately 20 x 30 ft with a door opening covered by thick plastic strips. Five to six other employees worked in the same room. The spotting table was approximately 3 ft high and approximately 3.5 ft wide and 2.5 ft long. The spotting table had a nonporous laminated top. A small kitchen exhaust hood (Broan Microtek Systems IV®, Model 88,000C) was located above the spotting station to reduce inhalation hazards from the spotting chemicals. The hood exhausted into the adjacent drycleaning room. The hood was mounted on the wall, approximately 3 ft above the spotting table. Average air velocity at the face of the hood was approximately 170 fpm. Six inches below the face of the hood, there was no induced air movement caused by the fan and none at the working surface.
The spotting room had a dedicated air handling unit. The supply and exhaust were located in the middle of the room, side by side. Examination of the air handling unit located on the roof showed that it was in good condition. However, the air intakes were closed, thereby allowing no makeup air to enter the room.
Spotting Chemical Results
The results of air sampling for spotting chemicals revealed that all concentrations of PERC, trichloroethylene, methyl isobutyl ketone, and n-butyl acetate were below OSHA limits and many concentrations were below detection limits. The long-term exposures were collected for an average of 115 min. No 2-butoxyethanol or hexylene glycol was detected. The spotter's TWA exposures to PERC and trichlorethylene for days 1 and 2 were, respectively, 5.40 ppm and 12.31 ppm; for the tagger, the exposures were 2.64 ppm and 9.50 ppm. Time-weighted average exposures are shown in Table 15. For the four chemicals that have a STEL, short-term exposures were measured and are shown in Table 16.
Because the spotter was exposed to multiple solvents, the additive effects of multiple solvent exposure were evaluated. The highest percentage of the TLV calculated for the mixture was 10% during day 2 for the tagger, who was tested for PERC and trichloroethylene exposures.
Because the air sampling results found relatively low concentrations, the real-time data was evaluated qualitatively. The real-time data was gathered over a basket beside the spotting table where garments were placed after being spotted. The spotting agents in the garments off-gassed into the work environment, as they sat in the basket. The relative concentration of solvents above the basket peaked when a recently spotted garment was placed in the basket. There appeared to be a cumulative effect; as more garments were placed in the basket, the background concentration of solvents also increased, as shown in Figure 27.
Figure 27. Real-time solvent concentrations measured over a basket which is slowly being filled with garments as they are spotted. There is no local ventilation.
Discussion and Conclusions
It appeared that excessive quantities of spotting solvents were applied. There was little examination of the type of stain before solvents were poured onto the garment. Lowered solvent use would have reduced off-gassing when garments were placed in baskets next to the spotting table.
Local exhaust ventilation is probably the most effective control approach for reducing solvent exposures during the spotting process. Spotting tables are now available that are equipped with an exhaust hood. Another appropriate control option is isolation by placement of a physical or time barrier between the hazard and the workers.
Larger shops, having more space, provide greater flexibility for isolating processes. Smaller shops do not have room to easily isolate the spotter from other workers while maintaining proximity to the drycleaning room. In this setting, workers near the spotting table can be needlessly exposed. In the evaluated shop, most of the reported worker headaches were believed to be caused by solvent vapors. There were several complaints regarding the solvent odor. Process isolation should be used in conjunction with good local and general ventilation.
The small kitchen exhaust hood in the evaluated shop was not appropriate or effective for three reasons:
- The velocity of air from the hood was inadequate to capture the contaminants originating from the table surface.
- The hood was improperly placed. If the velocity of air had been high enough to capture the contaminants, the contaminants would have been pulled through the worker's breathing zone.
- The contaminated air was exhausted into the adjacent room where a worker was performing drycleaning. General ventilation should add fresh air and remove general facility air to dilute contaminant concentrations. The air handling unit which serviced the room appeared to be in good condition; however the fresh air intake was closed.
Use of personal protective equipment in the facility studied was inappropriate. Personal protective equipment is particularly important for the spotters who work with a wide variety of hazardous chemicals. There was a very brief written policy regarding respirators, but no fit testing occurred. There was no written program or policy concerning the use of other personal protective equipment. Both gloves and respirators were available, but not used. The gloves were made of natural rubber, and the respirator was a disposable particulate respirator that was inappropriate for organic vapors. The gloves were inappropriate because of the variety of chemicals being used.
Recommendations
All exposures to spotting chemicals evaluated during this study were below OSHA limits. That included exposures to PERC, trichloroethylene, 2-butoxyethanol, hexylene glycol, MIBK, and n-butyl acetate. As expected, the highest TWA full-shift exposures and short-term exposures were for the spotter. The highest area concentrations were measured at the spotting table. These concentrations were due to inadequate local exhaust ventilation. The additive effect of multiple solvents still did not cause exposures to exceed acceptable concentrations.
Based on OSHA standards, chemical exposures in the evaluated shop were not excessive; however, there were still complaints from employees who worked in the spotting room. When employees are bothered enough to complain, additional measures should be taken to reduce unpleasant odors that are an irritant to workers. Exhaust ventilation for the spotting process should be ducted through a carbon adsorber outside of the building, rather than into another work area. A slot hood at table level or a downdraft table exhausting to the outside should be considered. The exhaust hood should be located near the source of contaminants to prevent the contaminants from being drawn through the workers' breathing zones.
Ideally, the spotting process should be isolated from other workers. Proper general ventilation should be provided that includes makeup air to compensate for any exhausted air. An inadequate volume of makeup air may result in negative pressure areas, perhaps resulting in drafts which may interfere with the exhaust hood. If makeup air is introduced, it should enter some distance from the exhaust to prevent short circuiting. As recommended by ASHRAE, ventilation systems in drycleaning shops should provide a minimum of 30 cfm of outside air per person.81 The spotting table should be made of a material impervious to the numerous chemicals used during the spotting process.
Spotters should be trained in selective pre-spotting. They should know the proper techniques for stain removal and the correct way to utilize spotting chemicals in the smallest quantities possible. To reduce solvent usage the spotter should recognize stains that will be removed in the drycleaning process. All garments do not require pre-spotting. Spotters who reduce the number of treated garments will reduce immediate exposures and those from off-gassing garments.
Training should also include the proper use of personal protective equipment (PPE). PPE such as gloves, goggles, and chemical resistant aprons should be routinely used by the spotter to reduce dermal exposures. Gloves and aprons should be made of solvent-resistant materials, such as Viton® fluoroelastomer, polyvinyl alcohol, or unsupported nitrile. When deciding on a specific glove to use, workers should consider factors such as permeation, durability, dexterity, and cost.
Chemical splash goggles should be worn to prevent eye injury during spotting. Accidental contamination of the eye could result in minor irritation or complete loss of vision. An unobstructed eye wash station should be located near the spotting area to provide prompt eye irrigation. If chemical contamination of the eye occurs, prompt irrigation for at least 15 minutes can play a deciding role in limiting the extent of damage. These recommendations should help lower exposures to volatile spotting solvents to the lowest technically feasible concentration. Effective engineering measures, good work practices, and appropriate PPE should be used and maintained in order to minimize exposures.
Control of Ergonomic Risk Factors
Ergonomic Study
Some drycleaning workers may also be at risk of incurring musculoskeletal strain because of repetitive work. An ergonomic evaluation was performed at two drycleaning shops. One evaluation was a walk-through evaluation and the other was an in-depth evaluation. Job analyses evaluated garment transfer, pressing, and bagging operations. The following is a brief description of the jobs investigated, the associated sub-tasks, and related findings and observations from the in-depth report. The equipment described in this section is typical of drycleaning equipment used throughout the U.S.
Garment Transfer
Garment transfer consisted of transferring clothing from the washer to the reclaimer. The amount of clothes handled and the frequency of handling during the transfer process was dependent on the quantity of garments an employee could functionally "grab," which can vary per load. The tasks associated with this process were identified as follows:
- Moving a cart filled with dirty garments to be placed inside the washer. Three different sized carts were used. The dimensions, based on height, width, and length, were 34x27x38, 30x21x29, and 29x19x32 inches, respectively.
- Unloading the reclaimer, hanging clothes such as shirts and blouses, and placing pants on a cart or table to be transferred to the pressing area. Time required for this task varied. During this study, unloading time was approximately 15 to 20 seconds.
- Unloading the washer and loading the reclaimer (transfer time was approximately 15 to 30 seconds).
- Loading the washer with the next load of clothing (approximately 10 to 15 seconds).
- Setting the controls and starting each machine.
- Sorting, if necessary, dried clothing for the appropriate pressing station.
- Transporting dried clothing to the pressing area.
At this particular shop the washer and reclaimer were located next to one another, requiring the garments to be carried approximately 6 ft during transfer.
Pressing Operations
Pressing operations consisted of four separate workstations: two multi-press stations for pants, suits, dresses, skirts, coats, and some shirts and blouses; a shirt pressing station; and another station for less typical items such as draperies (NIOSH researchers did not evaluate the drapery presses during this study). A railing was suspended from the ceiling to approximately 74 in. above the floor (the rail height varied by as much as 3 in. because of floor unevenness). The railing was located at each pressing station to hold garments and aid in their transport.
Multi-press Station. The multi-press station consisted of general utility presses, puff irons, pants toppers, a steam-fed partial mannequin "suzie," and a hand iron. The process at this station began when a worker grasped the garments from the overhead railing or cart and either placed them on the "suzie" or the utility press. The mannequin was typically used for jackets, coats, and dresses. The presser placed a garment on the mannequin and activated a foot lever, which would gradually release steam. The presser then began to press other garments on the utility press.
The utility press was positioned horizontally. The base of the machine was stationary and the top of the press, which was mobile, was activated by the press operator. Clothing was positioned on the pad and the operator simultaneously activated the pressing lid and steam via two hand controls and a pedal. Once the lid had closed, the operator pressed down on a lever located on top of the lid to increase the pressure and steam on the garment. This procedure was repeated until the garment was fully pressed. The operator frequently used a hand-held iron to remove small wrinkles, which were difficult to remove with the utility press. The iron, weighing approximately 8 lb, was connected to a steam line, equipped with small buttons and levers for steam generation and regulation.
The shirt collar and cuff press was similar to the top-loading press. The press loading process consisted of placing the shirt's collar and cuffs on designated pads and activating the top-load press with a front lever. Additional steam and pressing action was available from levers located on the top-load press. As with the larger presses, this machine was controlled by an automatic timer.
The repetitive nature of this job was a potential concern. Although pressing did not appear to include heavy lifting, it was highly repetitive and involved some awkward postures because of excessive reaching. Because the pressing stations were nonadjustable, average-sized people might be required to reach beyond their normal limit. This situation was evident with the material rack. The rack was over 6 ft high, requiring an average-sized employee (male: 70 in.; female: 64 in.) to frequently reach well overhead when hanging pants or shirts. While the dynamic nature of this task was primarily limited to the upper extremity, the static posture of the lower extremity could also present problems. With the exception of scheduled work breaks, the employees stood for most of their workday. There did not appear to be quality, rubberized floor mats at the pressing stations, which could have reduced leg fatigue.
Shirt Pressing Station. The shirt pressing station included four separate workstations, which were used primarily for pressing men's shirts. Each station contained three pieces of equipment, which were operated by one worker who stood in the middle of the three machines. A description of the machines follows:
One machine, the cabinet bag sleever, was devoted to pressing shirt sleeves. Sleeves were fitted over two vertical posts and placed onto the sleever, one shirt at a time. Another machine, the collar and cuff press, was used for pressing shirt collars and cuffs. This machine was similar to the shirt collar and cuffs press described earlier.
The buck cabinet bosom, body, and yoke press was designed to press the front and back of the shirt. Each shirt was fitted over a vertical plate which moved in and out of the presser. Two separate alternating plates were used.
These three machines were located next to one another: the cabinet bag sleever machine in the center, and the other two machines on either side and perpendicular to the sleever. Within this area, a shirt was often fitted over the top of a stand. The collar was buttoned to allow passive stretching of the collar and to prevent shrinkage from cleaning.
At this particular station, the employee was able to work at all three machines simultaneously. The automatic nature of the shirt pressing operations allowed the employee to go from machine to machine, spending 10 to 15 seconds on each machine. Concern for the physical stress of the employee at this station was similar to that in the multi-press station.
Garment Bagging
Cleaned and pressed garments were wrapped in plastic bags just prior to being placed on the overhead conveyor system. The clothing on hangers were hung on an adjustable "bagging pole." Initially, the pole height was approximately 38in., but it could be extended to a height of approximately 68 in. The clothing and the pole were placed under a plastic bag dispenser, where a bag was manually pulled over the garment and hanger while avoiding the pole.
Ergonomic Results and Conclusions
Many of the ergonomic risk factors evaluated during this study involved repetitive motions and awkward postures. Such actions in combination with a high work rate and frequency may cause physical discomfort and musculoskeletal problems for workers.
The tasks required during garment transfer and pressing appeared to be highly repetitive and required excessive reaching and precision gripping. A number of measures could be taken in order to control these hazards. Redesign of the workstation would eliminate many of the awkward postures and the excessive reaching. The drycleaning industry should work closely with drycleaning equipment manufacturers to develop adjustable height workstations. Frequent breaks and worker rotation are often used to control the hazards of repetitive tasks. The following section suggests feasible options to reduce ergonomic risk factors at the workstations studied.
Recommendations
Garment Transfer
- Workers should be educated and trained to modify their work techniques by grabbing no more than 15-20 lb of clothing during the transfer operation.
- The bottom of clothing carts should be 16 in. off the ground, or clothing carts should have spring loaded bottoms no less than 16 in. off the ground to raise the clothes as the cart is unloaded. Also the cart should be rotated by the worker to reduce reach distances and stress on the back and shoulders. These modifications should reduce the amount of bending and reaching required by the operator.
Multi-Press Station
- Utility presses should permit vertical and horizontal adjustment at the point(s) of operation.
- Hand iron platforms should be located in proximity to the worker to reduce excessive reaching. Ideally the iron should be held by a suspension or counterbalancing device to reduce the amount of weight that the presser must lift.
- Two-hand controls should be replaced with proximity sensors to reduce stress on the fingers.
- Thick (3/8 in.), closed-cell silicone floor mats should be provided, having a beveled edge to reduce leg fatigue and trip hazard.
Shirt Pressing Station
- The height of cabinet bag sleever hand controls should be close to the point of operation to reduce excessive reaching.
- Dual-hand activation buttons should be replaced with proximity sensors to reduce stress on the worker's fingers.
- A "button pulling" device/tool could be developed to aid the worker in pulling the collar button through the button hole. This would reduce the repetitive pinch postures used by the worker.
Garment Bagging Area
Bagging poles should be vertically adjustable utilizing a hydraulic pedal control system. Bagging poles should be kept in good working condition by ensuring they are straight and lightly lubricated with a non-staining oil.
Control of Fire Hazards
Fire Hazard Study and Results
The drycleaning industry has traditionally had a problem with fires.25 Part of the reason for this problem has been the wide-spread use of flammable and combustible liquids as a cleaning medium. However, even drycleaning shops that use PERC, which is nonflammable, must be aware of fire hazards because of the large number of potential fuels and ignition sources kept onsite. Fire hazards for drycleaners in general were evaluated during the NIOSH study by an in-depth survey at a single, large shop that used both PERC and mineral spirits to dryclean garments. Mineral spirits is a Class II, combustible liquid with a flashpoint of 49°C (120°F). Because more than 60 gal of mineral spirits were used, the drycleaning room was considered a high hazard area based upon NFPA codes.
The shop evaluated had one main floor and a partial basement. Exterior walls of the building were constructed of concrete block. Large windows were located across the front of the building. A parapet fire wall bordered the north and south sides of the southern half of the building. Most interior walls consisted of wood stud construction with plaster facing; however, some had a wallboard facing. Most of the building was built on a concrete slab, and the floors were covered with a ceramic tile. The rear portion of the building, which was built over the partial basement, had wooden floors. The roof frame was supported by steel joists and consisted of a steel deck, asphalt, and gravel. The shop was divided into a southern and northern half, divided by a parapet fire wall. The southern half consisted of clothing storage, drycleaning presses, the break room, and tagging area. The northern half of the building contained the drycleaning room, shirt laundry, shirt pressing area, alternations, and offices.
The drycleaning room evaluated was bordered on two sides by a fire partition. The two doorways between the drycleaning room and other areas of the shop had rolling fire doors, having a 3-hour fire resistance rating. There was one exit from the drycleaning room leading out of the building and a garage door used for deliveries. A hinged, swinging, side door was located next to one drycleaning machine; however, it was blocked and unavailable for use. This door had a 1-hour fire resistance rating. One large propeller fan, providing general ventilation, was located in the rear wall of the drycleaning room and exhausted outside of the building.
Drycleaning was performed using two PERC dry-to-dry machines and a transfer unit consisting of a separate washer and reclaimer, which used mineral spirits. The dry-to-dry machines were Union® Models L80 and L116, having a capacity of 80 lb and 70 lb, respectively. The washer was a Marvel® Model "Fourteen-O," and the reclaimer was a Hoyt® Petromiser having a 62-lb capacity. The reclaimer was equipped with a refrigerated condenser to recover solvent vapors and did not have a secondary vapor recovery device. Some of the findings from this study follow.
Drycleaning Machine Design
The design of the traditional, petroleum-based, transfer unit in this shop is typical of many used throughout the U.S. The washer, which used mineral spirits, did not have an internal fire extinguishing system. The dryer or "reclaimer" was inspected and approved by Factory Mutual Research Corporation for conditions of performance, safety, and quality. All of the electrical controls on this machine were explosion proof. The reclaimer was equipped with an automatic steam-injection, fire-extinguishing system for protection against fire and a high limit temperature control to safeguard against overheating. Mineral spirits were recovered from the drying air by passing the airstream through a condenser. A liquid solvent and water mixture was condensed, and it was then piped to a separator. From the separator the water and mineral spirits were directed into two separate, open, 5-gal buckets on the floor behind the machine. When the machine door was opened, an exhaust fan pulled the ambient air through the dryer and exhausted it outside of the building. In the event of an explosion within the machine, the blast would be released upwards through vents in the top of the machine. This system did not comply with NFPA codes because the solvent, a combustible liquid, was improperly transported in an open container between the reclaimer and washer, and there was no fire protection system provided for the washer. NFPA Code 32 calls for the installation of automatic fire extinguishing systems on washer-extractors and does not permit handling of combustible liquids in open containers.
Occupancy
The shop evaluated had 56 employees and was occupied from approximately 5:00a.m. to 6:00 p.m. on Monday through Saturday. During the evaluation, the number of workers occupying the building ranged from 35 to 45 people on various days. The shop had approximately 8,500 ft2 of floor space. According to NFPA 101, industrial occupancies shall have not more than one person per 100 ft2 of floor area. Based upon the floor area, 85 employees were allowed in this building at one time, so floor area was not a problem.
Heat Load
Heat or fire load refers to the severity of a fire that would be predicted in an occupancy, based upon the heat release rate of the combustible materials that are present and divided by the fire area in square feet. Typically, ordinary combustibles have a heat of combustion of approximately 8,000 British Thermal Units (BTU) per pound. Occupancies are traditionally divided into three categories:90
Low fire load: 100,000 BTU/ft2
Moderate fire load: 100,000 BTU/ft2 to
200,000 BTU/ft2
High fire load: 200,000 BTU/ft2 to
400,000 BTU/ft2
Heat load calculations were based upon building contents, construction, and heat of combustion. Garment quantities and content mass were estimated. The heat load in this building was approximately 34,000 BTU/ft2 which according to the previously outlined criteria is classified as "low."
Egress
There were three factors involved in egress analysis: travel distance, occupancy load, and exit capacity. NFPA 101 (The Life Safety Code) calls for a maximum travel distance of 75 ft to an exit. There were nine exits from the first floor. Seven exits had a width of 2.5 ft, and the other two exits had a width of 5.0 ft. Exit capacity is determined by considering the width of the exit and the number of occupants that might pass through the exit during a fire. Calculations indicated that sufficient exiting was provided.
According to NFPA 101, two remote exits are required for each level of a building and high hazard areas. There was only one approved exit from the drycleaning room. The garage door and the two fire doors were not approved Dexits. Exit paths must also be kept free and clear of obstructions or clutter. ADt this shop, there were many items which blocked the exit path and presented problems for rapid egress.
Fire Extinguishers
An analysis was performed on the type, capacity, and locations of fire extinguishers at the same shop. Class A extinguishers are for ordinary building protection and can use water, dry chemical, or halon. Class B extinguishers are for flammable liquids and can use CO2, dry chemical, halon, or aqueous film-forming foam agents (AFFF). Class C extinguishers are for fires in charged electrical equipment and use CO2, dry chemical, or halon.
There were 15 multi-purpose fire extinguishers located throughout the shop. Two extinguishers were in the basement, and all of the other extinguishers were located on the main floor. Most of those extinguishers were rated "BC" suitable for flammable liquids and fires in charged electrical equipment. Based upon guidelines in the NFPA Handbook, the fire extinguishers present in this building were of adequate size, type, and distribution. Table 5-23C of the NFPA handbook (17thed.) calls for a maximum travel distance of 30 ft to an extinguisher rated at 30-B in a high hazard area. This distance was appropriate for all of the extinguishers in the drycleaning room, which is a high hazard area. For moderate hazard areas, extinguishers rated at 10-B and 20-B should have a maximum travel distance of between 30 and 50 ft, respectively. Travel distances for all extinguishers located throughout the building were within acceptable ranges.
Fire Detection and Suppression Systems
There was no automatic sprinkler system or fire detection system in this building. Because of the significant fuels and ignition sources in drycleaning, a fire detection system should have been installed to provide 24-hour notification to the fire department. This system would be particularly important during hours when a building is unoccupied. Depending on the proximity of the fire department, rapid notification of fire could facilitate a quicker response. Photoelectric detectors are the most effective for detecting smoldering fires and should be installed in the majority of drycleaning buildings with the exception of the drycleaning room. This room should be equipped with an ionization detector to rapidly detect a fast-flaming fire, which typically occurs when a flammable/combustible liquid is ignited. A wet-pipe automatic sprinkler system should be installed in accordance with the NFPA Code 32 for drycleaning plants.
Discussion and Conclusions
To assess fire hazards, the following factors should be evaluated:91
- Flash Point: The temperature to which a liquid must be raised such that sufficient vapor is produced for ignition.
- Lower Explosive Limit (LEL): The lowest concentration (volume percent) of vapor in air through which a flame, once initiated, will continue to burn.
- Upper Explosive Limit (UEL): The highest concentration (volume percent) of vapor in air through which a flame, once initiated, will continue to burn.
It is important to remember that fuel, oxygen, and an ignition source are all necessary in order for a fire to develop. Petroleum-based solvent vapors are fuels which can burn if they are present in concentrations between the LEL and UEL with sufficient oxygen. Air contains approximately 21% (volume percent) oxygen. Air supports flames at that concentration, but if the concentration falls below approximately 8% flames will extinguish. When there is sufficient fuel and oxygen, a fire can begin in the presence of an ignition source, such as a spark or static electricity.56, 91 Drycleaning machine designers must avoid the conditions that are essential for a fire to occur and ensure their machines operate outside of the flammable region (see Figure 28). Likewise, shop owners must take appropriate steps to prevent the conditions that are necessary in order for a fire to develop.
Figure 28. Limits of flammability for combustible liquids.
At most drycleaning shops, the primary oxidizing agent is the oxygen in the atmosphere. Potential combustible materials include portions of the building itself, furniture, garments, lint, and flammable/combustible petroleum-based drycleaning solvents. Sources of ignition include heat energy, which is produced primarily from chemical, electrical, and mechanical energy. This heat energy can come from a burning or smoldering cigarette; heat transfer from heated equipment on or near a press; or friction from moving parts, a frictional spark inside the reclaimer cage, or even static electricity that might build up within the reclaimer.
Recommendations
Fire hazards can be reduced using a two-pronged approach. First, the greatest risk of fire and explosion in drycleaning shops comes from the use of a petroleum-based solvent in drycleaning machines. Solvents and machines are currently available that are inherently safer than traditional petroleum-based solvents and machines. Second, all shops should comply with appropriate fire codes that address occupancy, egress, fire extinguishers, detectors, suppression, and many other issues that are appropriate to reduce the risk of fire not only in the drycleaning area but also throughout the entire shop.
Petroleum-based solvents with flashpoints above 55°C (131°F) have recently been developed and are available primarily through the Exxon and Shell Corporations. Solvents with higher flashpoints are less likely to ignite or explode than solvents with lower flashpoints. New petroleum-based drycleaning machines are now available that are much safer than those of the past. Several technical advances have been developed to improve machine safety and greatly reduce the risk of fire and explosion. These advances include using a vacuum technology; or using an inert gas, such as nitrogen; or controlling the operating parameters of the machine to prevent fire or explosion. These measures can be taken either in combination or separately.
Some older shops which began operation prior to the adoption of recent codes are not required to comply with the recent provisions. In spite of this fact, code compliance would reduce the risk of property damage, injury, or death from fire. Compliance with current codes may also reduce property insurance premiums. Based upon observations and review of pertinent NFPA/BOCA fire codes, OSHA regulations, insurance company standards, and research reports, the following recommendations are offered to reduce the risk of fire, particularly in drycleaning shops using Class II, combustible liquids. The following list is not all encompassing and for more detailed information, the reader should refer to appropriate fire codes.
- Each shop should have at least two remote means of escape in the event of a fire. Drycleaning rooms should also have two remote means of escape. Fire exits and exit routes should always be kept free and clear of clutter.92
- A "No Smoking" policy should be established that eliminates smoking within the building, and "No Smoking" signs should be posted as appropriate.56,93 This will eliminate one common, potential source of ignition.
- The drycleaning room should be separated from the rest of the building by a partition having a 2-hour fire resistance rating.56
- The floors and ceiling of the drycleaning room should be of fire-resistive construction.
- Drycleaning and tank storage rooms should be located on the lowest floor above grade.94
- All open containers that contain flammable or combustible petroleum-based solvents should be closed to the atmosphere. Petroleum-based solvents should not be transported in open containers, but should be pumped through rigid iron or steel pipes.56,93
- Special attention should be given to generation and accumulation of static electricity. When garments are transferred from a washer, using petroleum-based solvents, to a dryer, the equipment should be electrically bonded together and grounded.
- Drycleaning rooms with petroleum-based solvents should have an emergency drainage system that directs solvent leaks and fire protection water to a safe location.
- A regular maintenance schedule should be followed to prevent accumulation of fluff, lint, or waste that could ignite or cause a fire to spread rapidly.
- An approved wet-pipe sprinkler system should be installed in the drycleaning room of any shop using petroleum-based drycleaning solvents. Automatic sprinkler systems have proven effective in preventing loss of life and controlling the spread of fire.56
- Not less than two approved 10-BC portable fire extinguishers should be provided inside a drycleaning room using petroleum-based solvents. Suitable portable fire extinguishers should be provided throughout the shop according to appropriate codes.94
Overall Conclusions
This study examined various types of drycleaning equipment being used in the U.S., such as transfer and dry-to-dry, vented and nonvented, and modern drycleaning machines equipped with various vapor recovery devices. TWA worker exposures to PERC were relatively low, and the evaluated shops maintained TWA exposures to PERC below 25 ppm. However, most of the shops had very high instantaneous exposures during loading and unloading of the drycleaning machine, which accounted for more than half of the operator's TWA exposures and was well above the OSHA peak exposure level of 300 ppm.
Although TWA operator exposures were relatively low, most operator exposures could have been further reduced by additional control measures. All shop owners should consider eventually replacing their current machines with state-of-the-art drycleaning machines equipped with advanced vapor recovery systems, including refrigerated condensers and carbon adsorbers, or consider retrofitting. Shop owners should also strive to provide more effective use of local and general ventilation to control PERC exposures. Both of these approaches will reduce peak exposures during loading and unloading, as well as full shift TWA exposures. Larger shops' owners should consider alternative cleaning media, such as petroleum-based solvents or water. These owners should also consider isolating the drycleaning process through use of "satellite shops" or other physical separation of the process within the shop.
Although inhalation of spotting chemicals was not a significant hazard, isolation of this process would avoid unnecessary exposure to other workers. A variety of methods can be taken to reduce spotting chemical exposures further. Other risks in the drycleaning industry are ergonomic hazards, involving repetitive motions and awkward postures. These primarily occur at the pressing stations and can be controlled. Redesigned, adjustable workstations for pressing will decrease the awkward postures and excessive reaching. Frequent breaks and worker rotation will reduce worker repetition.
Fire hazards can be controlled through two methods. The use of petroleum-based solvents present the greatest risk of fire and explosion in drycleaning shops. New petroleum-based solvents and machines, which are both inherently safer than those traditionally used, should be employed more widely in the U.S. Furthermore, all shops should comply with appropriate fire codes to reduce the risk of fire, not only in the drycleaning area but also throughout the entire shop.
References
- IARC [1995]. IARC monographs on the evaluation of carcinogenic risk to humans: dry cleaning, some chlorinated solvents and other industrial chemicals. Vol. 63. Lyon, France: World Health Organization, International Agency for Research on Cancer, pp. 33–71, 159–221.
- Wentz M [1995]. The evolution of environmentally Responsible Fabricare technologies. Am Drycleaner, 62(7):52–62.
- EPA [1991]. Dry-cleaning facilities. In: Jordan BC, ed. Background information for proposed standards. Research Triangle Park, NC: U.S. Environmental Protection Agency, Office of Air Quality Planning and Standards, EPA Document 450/3–91–020a, pp. 1.1–8.12.
- Amoore J, Hautala E [1983]. Odor as an aid to chemical safety: odor thresholds compared with threshold limit values and volatilities for 214 industrial chemicals in air and water dilution. J Appl Toxicol 3(6):272–292.
- NIOSH [1980]. NIOSH technical report: engineering control technology assessment of the dry cleaning industry. Cincinnati, OH: U.S. Department of Health and Human Services, Public Health Service, Centers for Disease Control, National Institute for Occupational Safety and Health, DHHS (NIOSH) Publication No. 80–136.
- Hillenbrand B [1988]. Memorandums of March–April 1988, from State OSHA Administrators to the Director of Federal-State Operations for OSHA, concerning high risk small businesses.
- American Business Information [1994]. Business America on disk. (CD-ROM disk) Omaha, NE: ABI.
- NIOSH [1989]. National occupational exposure survey. Cincinnati, OH: U.S. Department of Health and Human Services, Public Health Service, Centers for Disease Control, National Institute for Occupational Safety and Health. Unpublished Provisional Data as of 11/27/1989.
- NIOSH [1977]. Occupational disease: a guide to their recognition. rev. ed. Cincinnati, OH: U.S. Department of Health, Education, and Welfare, Public Health Service, Center for Disease Control, National Institute for Occupational Safety and Health, DHEW (NIOSH) Publication No77–181, pp213–215, 217–219, 191–193, 144–146, 319–321.
- Code of Federal Regulations [1991]. 40 CFR part 60 and 63. Washington, DC: U.S. Government Printing Office, Office of the Federal Register.
- Duh RW, Asal NR [1984]. Mortality among laundry and dry-cleaning workers in Oklahoma. Am J Publ Health 74:1278–1280.
- Blair A, Stewart P, Tolbert PE, Grauman D, Moran FX, Vaught J, Rayner J [1990]. Cancer and other causes of death among laundry and dry-cleaning workers. British J Ind Med 47:162–168.
- Katz RM, Jowett D [1981]. Female laundry and dry-cleaning workers in Wisconsin: a mortality analysis. Am J Publ Health 71:305–307.
- Ruder AM, Ward EM, Brown DP [1994]. Cancer mortality in female and male dry cleaning workers. J Occup Med 36(8):867–874.
- Asal NR, Coleman RL, Petrone RL, Owens W, Wadsworth S [1988]. A petroleum solvent mortality study of Oklahoma dry cleaners. Vols. 1, 2. Oklahoma City, OK: Departments of Biostatistics and Epidemiology and Environmental Health, College of Public Health, University of Oklahoma at Oklahoma City. NIOSH grant no. 5R01 0H02104–02 for Final Report on Project Period 01/01/86–03/31/88.
- Lin RS, Kessler II [1981]. A multifactorial model for pancreatic cancer in man: epidemiologic evidence. J Am Med Assoc 245:147–152.
- NTP [1986]. NTP technical report on toxicology and carcinogenesis studies of tetrachloroethylene (perchloroethylene) (CAS No127–18–4) in F344/N rats and B6C3F1 mice (inhalation studies). Research Triangle Park, NC: U.S. Department of Health and Human Services, Public Health Service, National Institutes of Health, National Toxicology Program Toxicity Report Series No. 311, DHHS (NIH) Publication No. 86–2567.
- IARC [1987]. IARC monographs on the evaluation of the carcinogenic risk to humans: Tetrachloroethylene (Group 2B). Suppl 7. Lyons, France: World Health Organization, International Agency for Research on Cancer, pp. 355–357.
- Code of Federal Regulations [1995]. 29 CFR 1910.1000(f)(4) Table A-1-A, Table Z-2. Washington, DC: U.S. Government Printing Office, Office of the Federal Register.
- NIOSH [1992]. NIOSH recommendations for occupational safety and health. Cincinnati, OH: U.S. Department of Health and Human Services, Public Health Service, Centers for Disease Control, National Institute for Occupational Safety and Health, DHHS (NIOSH) Publication No. 92–100.
- Clark RA [1993]. Memorandum of March 30, 1993, from Roger A. Clark, Director of Compliance Programs, OSHA, to Office Directors, OSHA, concerning most frequently asked questions on the Air Contaminants Rule.
- NIOSH [1978]. Current Intelligence Bulletin 20: tetrachloroethylene (perchloroethylene). Cincinnati, OH: U.S. Department of Health, Education, and Welfare, Public Health Service, Center for Disease Control, National Institute for Occupational Safety and Health, DHEW (NIOSH) Publication No. 78–112.
- ACGIH [1996]. Threshold limit values for chemical substances and physical agents and biological exposure indices. Cincinnati, OH: American Conference of Governmental Industrial Hygienists, pp. 11–41.
- OSHA [1993]. Regulations, documents and technical information. Washington, DC: U.S. Department of Labor, Occupational Safety and Health Administration. Unpublished database; OSHA CD-ROM, (OSHA A93-2).
- Wentz M [1995]. What's new about petroleum cleaning technology? Am Drycleaner 62:8:76–86.
- Busler C [1987]. IFI bulletin: characteristics of dry cleaning solvents. Silver Spring, MD: International Fabricare Institute, Technical Operating Information (TOI) No. 594.
- Boewe Passat [1993]. Pocket guide to textile cleaning. Augsburg, Germany: Boewe Passat, pp. 38–43.
- ACGIH [1996]. Threshold limit values for chemical substances and physical agents and biological exposure indices. Cincinnati, OH: American Conference of Governmental Industrial Hygienists, pp. 11–41.
- IFI [1989]. Focus on drycleaning: reducing vapor exposure: OSHA compliance. Vol. 13, No. 5. Silver Spring, MD: International Fabricare Institute.
- Armstrong TJ [1986]. Ergonomics and cumulative trauma disorders. Hand Clinics 2:553–565.
- NIOSH [1987]. Hazard evaluation and technical assistance report: Harvard Industries, Inc., Bucyrus, OH. Cincinnati, OH: U.S. Department of Health and Human Services, Public Health Service, Centers for Disease Control, National Institute for Occupational Safety and Health, DHHS (NIOSH) Report No. HHE-87-428-2063.
- Kaplan PE [1983]. Carpal tunnel syndrome in typists. J Am Med Assoc 25(6): 821–822.
- Luopajarvi T, Kuorinka I, Virolainen M, Holmberg M [1979]. Prevalence of tenosynovitis and other injuries of the upper extremities in repetitive work. Scand J Work Environ Health 5(3):48–55.
- Hagberg M [1984]. Occupational musculoskeletal stress and disorders of the neck and shoulder: a review of possible pathophysiology. Int Arch Occup Environ Health 53:269–278.
- Putz-Anderson V, ed. [1988]. Cumulative trauma disorders: a manual for musculoskeletal diseases of the upper limbs. Bristol, PA: Taylor and Francis, pp. 47–73, 3–7, 21–24.
- Corlett E [1983]. Analysis and evaluation of working posture. In: T.O. Kvalseth, ed. Ergonomics of workstation design. London: Butterworths, pp. 12–15.
- NIOSH [1993]. Occupational health supplement to NHIS, 1988: estimated back pain caused by activities at work for occupational codes 771, 748, and 747 (laundry, cleaning, and garment services; laundry and dry-cleaning machine operators; and pressing machine operators). Cincinnati, OH: U.S. Department of Health and Human Services, Public Health Service, Centers for Disease Control and Prevention, National Institute for Occupational Safety and Health. Unpublished database; provisional data as of 7/1/93.
- Silverstein B, Fine L, Armstrong T [1986]. Hand wrist cumulative trauma disorders in industry. Br J Med, 43: 779–784.
- Hartzell GE [1991]. Material, products, and environments: combustion products and their effects on life safety. In: Cote AE, Linville JL, eds. Fire protection handbook. 17th ed. Quincy, MA: National Fire Prevention Association, pp. 3–3 to 3–14.
- Earnest GS, Beasley AB [1994]. Walk-through survey report: perchloroethylene exposures and ergonomic hazards in commercial dry cleaners at Widmer's Dry Cleaners. Cincinnati, OH: U.S. Department of Health and Human Services, Public Health Service, Centers for Disease Control and Prevention, National Institute for Occupational Safety and Health, DHHS (NIOSH) Report No. ECTB 201–13a, NTIS No. PB94-108149.
- Earnest GS, Beasley AB [1994]. Walk-through survey report: perchloroethylene exposures and ergonomic hazards in commercial dry cleaners at Hyde Park "One Hour" Martinizing Cleaners. Cincinnati, OH: U.S. Department of Health and Human Services, Public Health Service, Centers for Disease Control and Prevention, National Institute for Occupational Safety and Health, DHHS (NIOSH) Report No. ECTB 201-12a, NTIS No. PB94-117140.
- Earnest GS, Beasley AB, Smith SS [1994]. Walk-through survey report: perchloroethylene exposures and ergonomic hazards in commercial dry cleaners at Teasdale Fenton Cleaners, Cincinnati, OH. Cincinnati, OH: U.S. Department of Health and Human Services, Public Health Service, Centers for Disease Control and Prevention, National Institute for Occupational Safety and Health, DHHS (NIOSH) Report ECTB No. 201-11a, NTIS No. PB94-110343.
- Earnest GS [1994]. Walk-through survey report: perchloroethylene exposures in commercial dry cleaners at Springdale Cleaners, Cincinnati, Ohio. Cincinnati, OH: U.S. Department of Health and Human Services, Public Health Service, Centers for Disease Control and Prevention, National Institute for Occupational Safety and Health, DHHS (NIOSH) Report No. ECTB 201-14a, NTIS No. PB94-117918.
- Earnest GS, Moran AJ, Spencer AB, Kovein RJ, Hall RM, Gressel MG [1994]. In-depth survey report: Control of perchloroethylene exposures in commercial dry cleaners at Appearance Plus Cleaners, Cincinnati, Ohio, March 30-31, 1994. Cincinnati, OH: U.S. Department of Health and Human Services, Public Health Service, Centers for Disease Control and Prevention, National Institute for Occupational Safety and Health, DHHS (NIOSH) Report No. ECTB 201-15a, NTIS No. PB95-200564.
- Earnest GS, Moran AJ, Spencer AB [1995]. In-depth survey report: control of perchloroethylene exposures in commercial dry cleaners at Tuchman Cleaners, Fischers, Indiana, May 9-12, 1994. Cincinnati, OH: U.S. Department of Health and Human Services, Public Health Service, Centers for Disease Control and Prevention, National Institute for Occupational Safety and Health, DHHS (NIOSH) Report No. ECTB 201-17a, NTIS No. PB95-200689.
- Earnest GS, Spencer AB [1995]. In-depth survey report: control of perchloroethylene exposures in commercial dry cleaners at Brown's Cleaners, Santa Monica, California, August 15-18, 1994. Cincinnati, OH: U.S. Department of Health and Human Services, Public Health Service, Centers for Disease Control and Prevention, National Institute for Occupational Safety and Health, DHHS (NIOSH) Report No. ECTB 201-16a, NTIS No. PB95-242582.
- Spencer AB, Earnest GS, Kovein RJ [1995]. In-depth survey report: exposures during the spotting procedure in a commercial dry cleaner at Widmer's Dry Cleaning, Cincinnati, Ohio, August 29-31, 1994. Cincinnati, OH: U.S. Department of Health and Human Services, Public Health Service, Centers for Disease Control and Prevention, National Institute for Occupational Safety and Health, DHHS (NIOSH) Report No. ECTB 201-13b, NTIS No. PB95-267720.
- Earnest GS [1995]. In-depth survey report: chemical exposures and fire safety in commercial dry cleaners at A-One Cleaners, Cincinnati, Ohio. Cincinnati, OH: U.S. Department of Health and Human Services, Public Health Service, Centers for Disease Control and Prevention, National Institute for Occupational Safety and Health, DHHS (NIOSH) Report No. ECTB 201-18a, NTIS No. PB95-267720.
- Earnest GS, Spencer AB, Smith SS, McGlothlin JD [1995]. In-depth survey report: perchloroethylene exposures and ergonomic risk factors in commercial dry cleaners at Tuchman Cleaners Shop 24, Carmel, Indiana, September 6-9, 1994. Cincinnati, OH: U.S. Department of Health and Human Services, Public Health Service, Centers for Disease Control and Prevention, National Institute for Occupational Safety and Health, DHHS (NIOSH) Report No. ECTB 201-19a, NTIS No. PB96-106521.
- Mains H [1993]. Conversation on July 29, 1993, between G.S. Earnest, Division of Physical Sciences and Engineering, National Institute for Occupational Safety and Health, and Harold E. Mains, Fabritec International, Cold Spring, KY.
- International Fabricare Institute [1990]. IFI bulletin: disc filtration. Silver Spring, MD: International Fabricare Institute, Technical Operating Information (TOI) No. 620.
- Fabritec™ International [1989]. Research fellowship: a study of sanitone no-filtration. Cold Spring, KY: Fabritec International, No. F-42.
- Northey GA [1981]. Industrial drycleaning: reducing occupational exposure to perchloroethylene. Ind Launderer 32(6):82–89.
- IFI [1989]. Focus on drycleaning: IFI's equipment and plant operations survey. Vol. 13, No. 1. Silver Spring, MD: International Fabricare Institute.
- NIOSH [1996]. Hydrocarbons, halogenated: Method 1003. In: Eller PM, ed. NIOSH manual of analytical methods. 4th rev. ed. Vol. 2. Cincinnati, OH: U.S. Department of Health and Human Services, Public Health Service, Centers for Disease Control and Prevention, National Institute for Occupational Safety and Health.
- NFPA [1996]. Code 32: standard for dry cleaning plants. Quincy, MA: National Fire Protection Agency, sections 4–4.4.2; 2–5.7; 2–2.9; 2–4.3.1; 2–5.1.
- Michigan Department of Public Health [1988]. State of Michigan Administrative Rules for Class IV: dry cleaning establishments. Reprinted from Michigan Administrative Code. Lansing, MI: Michigan Department of Public Health, p. 12 (Part 4, R 325.17401).
- Lauber Jack D [1992]. Operating dry cleaning equipment to minimize exposures. In: Bergin, ed. EPA Proceedings: International Roundtable on Pollution Prevention and Control in the Dry Cleaning Industry, May 27-28, 1992, Falls Church, VA. Washington, DC: U.S. Environmental Protection agency, Office of Pollution Prevention and Toxics, EPA/774/R-92/002, pp. 22–30.
- ACGIH [1995]. Industrial ventilation. In: A manual of recommended practice. 22nd ed. Cincinnati, OH: American Conference of Governmental Industrial Hygienists, pp. 10–1 to 10–174.
- OSHA [1994]. Office of Management data systems: all OSHA standard paragraphs cited by frequency in SIC code 7216 (dry cleaning). Washington, DC: U.S. Department of Labor, Occupational Safety and Health Administration, Office of Management. Unpublished database; accession date, 9/30/94.
- CEC [1992]. Dry cleaning: an assessment of emission control options. Washington, DC: Center Emissions Control, p. 13.
- NIOSH [1983]. Control of occupational health hazards in the dry cleaning industry, instructor's guide. Cincinnati, OH: U. S. Department of Health and Human Services, Public Health Service, Centers for Disease Control, National Institute for Occupational Safety and Health, DHHS (NIOSH) Pub. No. 82-1876, pp. II-5, I-IV-11.
- FI. Focus on drycleaning: safe handling of perchloroethylene, part II. Vol. 2, No. 2. Silver Spring, MD: International F abricare Institute.
- Vasquez C [1995]. Wet cleaning equipment. Chicago, IL: Center for Neighborhood Technology, pp. 1–9.
- Hasenclever KD [1994]. Kreussler Information No. 23: basic principles and practice for the wet cleaning of textiles. Wies baden, Germany: Chemische Fabrik Kreussler & Co. GmbH.
- EPA [1993]. Multiprocess wet cleaning: cost and performance comparison of conventional dry cleaning and an alternative process. Washington, DC: U.S. Environmental Protection Agency, Office of Pollution Prevention and Toxics, EPA Document 744-R-93-004.
- Brown I, trans. [1995]. The importance of wet-cleaning for the textile care industry: options for organizational expansion and/or rationalization. Boennigheim, Germany: Hohenstein Institute, pp. 6, 21–24.
- Rice B, Weinberg J [1994]. A Greenpeace/Pollution Probe report: dressed to kill: the dangers of dry cleaning and the case for chlorine-free alternatives. Toronto, Ontario, Canada: Pollution Probe, Sunset Chemicals Project for the Great Lakes, p. 6.
- Seitz B [1996]. Is the drycleaning industry "all washed up?" Am Drycleaner 63:2:116–130.
- Hohenstein Institute [1995]. Requirements for the use of hydrocarbon solvents in the drycleaning industry (translated draft ). Stuttgart, Germany: Research Institute Hohenstein.
- Wolf K [1993]. Alternatives to PERC in dry cleaning: are they viable? Los Angelos, CA.: Institute for Research and Technical Assistance. Unpublished paper.
- EPA [1994]. New regulation controlling emissions from dry cleaners [brochure]. Washington, DC: U.S. Environmental Protection Agency, Office of Air Quality Planning and Standards (MD-10), EPA 453/F-94-025, U.S. GPO 1994-530-367.
- EPA [1991]. EPA handbook: control technologies for hazardous air pollutants. Cincinnati, OH: U.S. Environmental Protection Agency, Office of Research and Development, EPA 625/6-91/014, pp. 4–28 to 4–44.
- Meijer J [1986]. IFI bulletin: misuses of a carbon vapor adsorber. Silver Spring, MD: International Fabricare Institute, Technical Operating Information (TOI) No. 577.
- 56 Fed. Reg. 236 [1991]. U.S. Environmental Protection Agency: national emission standards for hazardous air pollutants for source categories: perchloroethylene emissions from dry cleaning facilities; proposed rule and notice of public hearing.
- den Otter W [1992]. Evaluation of "new generation" drycleaning equipment. In: Bergin, ed. EPA Proceedings: International Roundtable on Pollution Prevention and Control in the Dry Cleaning Industry, May 27-28, 1992, Falls Church, VA. Washington, DC: U.S. Environmental Protection Agency, Office of Pollution Prevention and Toxics, EPA/774/R-92/002, pp. 16–18.
- Fisher WE [1994]. Memorandum (IFI ProTek analysis) of February 16, 1994, from W.E. Fisher, Senior Vice President, International Fabricare Institute, Silver Spring, Maryland, to Gary S. Earnest, Division of Physical Sciences and Engineering, National Institute for Occupational Safety and Health, Centers for Disease Control and Prevention, Public Health Service, U.S. Department of Health and Human Services.
- CARB [1993]. Technical support document: proposed airborne toxic control measure and proposed environmental training program for perchloroethylene dry cleaning operations. Sacramento, CA: State of California, California Environmental Protection Agency, California Air Resources Board, pp. II–18 to II–25.
- ACGIH [1992]. Industrial ventilation. In: A manual of recommended practice. 21st ed. Cincinnati, OH: American Conference of Governmental Industrial Hygienists, pp.3–1 to 3–20.
- Moreland E [1986]. IFI bulletin: no-vent machines: a method of reducing vapor exposure. Silver Spring, MD: International Fabricare Institute, Technical Operating Information (TOI) No. 617.
- ASHRAE [1989]. Ventilation for acceptable indoor air quality. Atlanta, GA: American Society of Heating, Refrigeration and Air-Conditioning, Engineers. ANSI/ASHRAE Standard 62-1989, p. 8.
- Hohenstein Institute [1995]. Market overview of hydrocarbon solvents applied in textile drycleaning. (translated draft). Stuttgart, Germany: Research Institute Hohenstein.
- IFI [1991]. Focus on drycleaning: effective solvent reclamation: causes of poor solvent recovery. Vol. 15, No. 1. Silver Spring, MD: International Fabricare Institute.
- IFI [1988]. Correspondence course manual: fundamentals of dry cleaning. Silver Spring, MD: International Fabricare Institute.
- CCME [1992]. Environmental code of practice for the reduction of solvent emissions from dry cleaning facilities. Winnepeg, Manitoba: Canadian Council of Ministers of the Environment Secretariat, National Task Force on the Reduction of Solvent Emissions from Dry Cleaning Facilities, CCME-EPC/AITG-50E, p. 3, 5.
- EPA [1994]. Perchloroethylene dry cleaning facilities-general recommended operating and maintenance practices for drycleaning equipment. Research Triangle Park, NC: U.S. Environmental Protection Agency, Office of Air Quality Planning and Standards. E PA-4531R-94-073.
- Nelson G, Harder C [1976]. Respirator cartridge efficiency studies: VI. Effect of concentration. Am Ind Hyg Assoc J 37(4 ):205–216.
- The Dow Chemical Company [1992]. A basic handbook for dry cleaners. Midland, MI: The Dow Chemical Company.
- Vahdat N [1987]. Permeation of protective clothing materials by methylene chloride and perchloroethylene. Am Ind Hyg Assoc 48(7):646–651.
- Campbell JA [1991]. Confining fires: confinement of fire in buildings. In: Cote AE, Linville JL, eds. Fire Protection Handbook. 17th ed. Quincy, MA: National Fire Prevention Association, pp. 6–75 to 6–90.
- Drysdale DD [1991]. Basics of fire and fire science: chemistry and physics of fire. In: Cote AE, Linville JL, eds. Fire Protection Handbook. 17th ed. Quincy, MA: National Fire Prevention Association, pp. 1–42 to 1–55.
- OSHA [1992]. Fact Sheet No. OSHA 91-41: workplace fire safety. Washington, DC: U.S. Department of Labor, Occupational Safety and Health Administration, p. 1.
- BOCA [1994]. National Fire Prevention Code, Article 9: drycleaning plants. Country Club Hills, IL: Building Official Code Administration, sections F-901.4; F-902.2.
- Sentry [1992]. Sentry loss control standards: drycleaning plants using petroleum (Stoddard) drycleaning solvents. Sentry Insurance Company, Nashville, TN 37214, pp. 2, 3.
- Page last reviewed: June 6, 2014
- Page last updated: June 6, 2014
- Content source:
- National Institute for Occupational Safety and Health Education and Information Division