Preventing Vision Disturbances and Acute Physical Distress Due to Dimethylethylamine (DMEA) Exposure
December 1987
DHHS (NIOSH) Publication Number 88-103
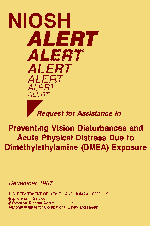
WARNING! Foundry owners, operators, and workers, manufacturers of polyamides, and other users of dimethylethylamine (DMEA) are cautioned that exposure to this chemical may cause vision disturbances and acute physical distress that may jeopardize the health and safety of workers.
Summary
This Alert describes the results of a National Institute for Occupational Safety and Health (NIOSH) investigation at an aluminum casting foundry where workers exposed to dimethylethylamine (DMEA) reported vision disturbances (blurred, foggy, and halo vision) and systemic effects (headache, nausea, and stomach pain) during coremaking operations. The vision disturbances and systemic effects occurred among workers exposed to DMEA at an 8-hour time-weighted average (TWA) concentration equal to or greater than 6 milligrams per cubic meter of air (6mg/m3, or 2 parts per million [ppm]). The adverse health effects may also have been caused by 15-minute DMEA exposures as high as 29 mg/m3 (9.7 ppm). Acute physical distress and halo vision were experienced at concentrations higher than those associated with blurred vision only.
Excessive concentrations of DMEA resulted from a failure to maintain pressure-tight seals in the corebox machine gaskets. NIOSH recommends increased maintenance on these gaskets and more periodic checks of core machine operation to prevent excessive concentrations of DMEA in the workplace. Currently, no OSHA permissible exposure limit (PEL) exists for DMEA. Thus airborne concentrations of DMEA should be reduced so that vision disturbances and systemic effects do not occur.
Aluminum and gray-iron foundry owners, operators, and workers, manufacturers of polyamides, other users of DMEA, trade associations, labor organizations, and editors of appropriate trade journals are requested to help prevent exposure to DMEA.
Background
Dimethylethylamine (N,N-dimethylethylamine, or DMEA) (CAS No. 598-56-1) is a tertiary aliphatic amine. This colorless, volatile liquid has a suffocating, ammonia-like odor and is extremely flammable, with a flashpoint of -36°C (38.8°F). Tertiary aliphatic amines such as DMEA have been shown to be local irritants that affect the eyes, mucous membranes, and skin. They are also known to cause blurred vision and to produce headache, nausea, and faintness [Stephenson and Albrecht 1986; Hartle 1982; Ashland Chemical Co. 1983].
DMEA is used in the production of mold cores in gray-iron and aluminum casting foundries and in the polymerization of polyamides. In 1977, the United States produced less that 1,000 pounds of DMEA, but it imported an estimated 1.2 to 12 million pounds. The National Institute for Occupational Safety and Health (NIOSH) has no estimate of the number of workers potentially exposed to this chemical.
DMEA is used under pressure as a gas catalyst in the coremaking operation. The cores are solid reproductions of the hollow spaces desired within the finished castings. They are made from a mixture of silica sand or other aggregates, liquid phenolic resin, and a diisocyanate in a corebox machine (Isocure® process). This mixture is cured in the corebox machine by a ½- to 3-second exposure to DMEA. Dry air is then blown through the core to purge any remaining DMEA. After the solidified cores are manually removed from the corebox, they are either placed on storage racks or they are assembled directly. Core finishers usually work adjacent to several of the core machines and perform many intricate manual tasks to finish and assemble the cores. From the coreroom, the finished cores are sent to the mold floor, where they are placed in molds before the molten metal is poured.
This Alert describes the effects of exposure to DMEA among workers in an aluminum casting foundry. It is based on the results of a NIOSH Health Hazard Evaluation (HHE) [Stephenson and Albrecht 1986]. When the HHE was conducted, core painters and some of the core machine operators wore gloves while performing their jobs. Just before the NIOSH survey, the foundry management began requiring all coreroom workers to wear chemical splash goggles instead of safety glasses to reduce exposure to DMEA. The core machines were equipped with local exhaust ventilation systems designed to help purge excess amine gas from the cores. The exhaust air was chemically treated to remove the amine before its release to the inside of the plant. Rubber compression seals were located at the periphery of the corebox cavities between the two corebox halves to prevent DMEA gas leaks, especially during the gaseous exposure phase of the core machine cycle.
Case Reports of Health Effects
The NIOSH HHE [Stephenson and Albrecht 1986] resulted from a union request prompted by workers' complaints of vision disturbances (blurred, foggy, or halo vision), headaches, and stomach pain that occurred during core production operations at an aluminum casting foundry. The investigation consisted of medical and environmental surveys and reviews of exposure records and emergency room records of workers exposed to suspected large releases of DMEA.
Medical Survey
On December 18-19, 1985, and on January 21-22, 1986, NIOSH investigators administered a medical questionnaire to 129 coreroom workers to ascertain the nature and frequency of vision disturbances and other signs and symptoms the workers had experienced during the past year. Episodes of hazy vision (described as "looking through smoke") were reported by 91% (117/129) of the coreroom workers. Other vision disturbances included blurred vision (i.e., objects out of focus) in 79% of the coreroom workers, tearing in 72%, halo perception in 64%, and eye irritation in 48%. A high proportion of the workers reported that they had difficulty doing their jobs (66%), difficulty driving after work (64%), and vision disturbances (85%) while experiencing other signs and symptoms of DMEA exposure such as headache, difficult breathing, and itchy skin. The signs and symptoms of vision disturbance were transient, lasting from 10 minutes to more than 4 hours. Reduction or abatement of the vision disturbances was achieved most effectively by time away from exposure.
Other signs and symptoms recorded in the medical survey included nausea, diarrhea, headache, dizziness or faintness, increased heart rate, flushed face, difficulty in breathing, tight feeling in the chest, itchy skin, rash, and metallic taste. These systemic effects are consistent with the effects of inhaling, ingesting, or absorbing DMEA [Stephenson and Albrecht 1986; Hartle 1982; Ashland Chemical Co. 1983]. Because of the retrospective nature of the medical questionnaire, there was no correlation of these effects with specific concentrations of DMEA. However, a review of company records for the preceding year showed that DMEA concentrations had been as high as 94 milligrams per cubic meter of air (94 mg/m3, or 3.27 parts per million [ppm]).
Emergency Room Records
Emergency room records indicated the following signs and symptoms in 16 coreroom personnel who sought treatment after suspected large releases of DMEA in November and December 1985: metallic taste (2 workers), eye, nose, or throat irritation (4 workers), dizziness or faintness (5 workers), tight feeling or pain in the chest (7 workers), abdominal cramps (8 workers), blurred vision (8 workers), increased heart rate (10 workers), headache (12 workers), and nausea (13 workers). Systemic effects such as nausea, headache, and increased heart rate appeared to be associated with DMEA concentrations higher than those associated with blurred vision only [Stephenson and Albrecht 1986]. The same investigators also concluded that halo vision occurred at higher concentrations or after longer exposures than did hazy vision. They further determined that other chemicals known to cause respiratory difficulties (specifically isocyanates) did not exceed the NIOSH recommended exposure limit (REL). Hartle [1982] and the Ashland Chemical Co. [1983] have reported similar effects among workers exposed to DMEA. Beard and Noe [1981] have reported that these effects also occurred among workers exposed to other amines.
Environmental Surveys
On January 21-22, 1986, NIOSH investigators conducted environmental surveys at the foundry to evaluate workers' exposures to chemicals used in making cores by the Isocure® process. Full-shift and 15-minute air samples were collected in the work area and in the workers' breathing zones during the manufacturing process to characterize their exposures to DMEA and other chemicals. DMEA concentrations from 56 full-shift breathing-zone samples ranged from 1.6 to 24 mg/m3 (0.5 to 8.0 ppm). Thirty-one 15-minute breathing-zone samples showed DMEA concentrations ranging from nondetectable amounts to 29 mg/m3 (9.7 ppm). The three full-shift area samples indicated DMEA concentrations ranging from 2.4 to 3.5 mg/m3 (0.8 to 1.2 ppm).
All coreroom workers whose DMEA exposures were characterized by air sample analysis were questioned after the shift about any vision disturbances. Acute episodes of halo vision were reported by three core machine operators: (1) a prototype operator with a full-shift exposure of 10 mg/m3 (3 ppm) and a 15- minute exposure of 29 mg/m3 (9.7 ppm), (2) a core machine operator with a full- shift exposure of 6 mg/m3 (1.8 ppm) and a 15-minute sample of 25 mg/m3 (8 ppm), and (3) another core machine operator with a full-shift sample of 6 mg/m3 (2 ppm). The core machine had been leaking during the collection of the 25- mg/m3 15-minute sample. All three core machine operators wore chemical splash goggles. Investigators attributed the vision disturbances to short-term exposures to peak concentrations of DMEA resulting from leaks at the corebox gaskets.
Other Incidents
NIOSH is aware of several other incidents of adverse health effects resulting from exposure to DMEA during coremaking processes. One incident occurred in an aluminum foundry [Rivera 1976] and four occurred in gray-iron foundries [Hartle 1982; Stephenson 1984; Ruhe 1984; Schmitter 1977]. DMEA concentrations measured in full-shift breathing-zone samples ranged from 1.1 to 45 mg/m3 (0.4 to 15 ppm).
Core workers experienced eye irritation or vision disturbances and systemic effects in all cases. Vision disturbances were associated with 15-minute DMEA exposures reported to be in the range of 75 to 299 mg/m3 (25 to 100 ppm) [Schmitter 1977]. However, NIOSH investigators reported that DMEA concentrations around 29 mg/m3 (9.7 ppm) were intolerable [Stephenson and Albrecht 1986]. Since Schmitter did not report his sampling and analytical methods, it is difficult to verify the accuracy of his reported exposures.
Regulatory Status
There is no OSHA permissible exposure limit (PEL), NIOSH REL, or American Conference of Governmental Industrial Hygienists (ACGIH) threshold limit value (TLV®) for DMEA. The foundry's supplier of DMEA has recommended that exposure be limited to a time-weighted average (TWA) of 29.9 mg/m3 (10 ppm) over an 8-hour work shift. However, no published documentation has been found to support this limit, and as noted earlier, NIOSH investigators found that concentrations around 29 mg/m3 (9.7 ppm) were intolerable. Trimethylamine, an aliphatic amine similar to DMEA, has an ACGIH recommended TLV of 24 mg/m3 (10 ppm) as an 8-hour TWA.
Conclusions
The NIOSH investigators concluded the following:
- Excessive concentrations of DMEA resulted from a failure to maintain pressure-tight seals in the corebox machine gaskets.
- The vision disturbances and systemic effects (e.g., faintness, chest and abdominal pain, headache, nausea, and increased heart rate) described in this report occurred among workers exposed to DMEA at an 8-hour TWA concentration of 6 mg/m3 (2 ppm) or greater.
- Short-term (15-minute) DMEA exposures as high as 29 mg/m3 (9.7 ppm) may also have caused vision disturbances and systemic effects.
Recommendations
NIOSH recommends that all owners and managers of gray-iron and aluminum casting foundries, manufacturers of polyamides, and other users of DMEA implement or reinforce the following steps to reduce worker exposure so that vision disturbances and systemic effects do not occur:
- Increase the maintenance on corebox machine gaskets and the number of periodic checks of core machine operation.
- Modify work practices by (a) reducing the pressure that delivers DMEA to coreboxes to avoid excess gaseous DMEA in the corebox machine, (b) cleaning the joints of the coreboxes to remove excess core sand, and (c) adjusting the system that converts liquid DMEA to a gas so that less liquid DMEA remains in finished cores.
- Improve engineering control of DMEA by (a) performing regular, thorough evaluations of the local exhaust ventilation systems for the core machines to assure that the capture velocities are adequate and that there are no leaks in the system, (b) substituting less hazardous or less volatile amines, and (c) automating the process.
- Train workers to (a) handle DMEA safely with the use of personal protective equipment such as gloves, goggles, and respirators, and (b) recognize the signs and symptoms of DMEA exposure.
- When engineering controls are insufficient to prevent the signs and symptoms of DMEA exposures, workers must wear full-facepiece respirators with organic vapor cartridges.
- Reduce dermal absorption by wearing protective gloves. A search of the literature indicates that gloves made from butyl rubber or Silver Shield® gloves appear to provide the best protection. Gloves made from nitrile rubber are a second choice. Regardless of the material selected, the gloves should be tested under actual work conditions.
- Develop and implement procedures to increase worker reporting of all vision disturbances and systemic effects to plant nurses or physicians. Health care personnel should monitor and evaluate the health of all persons who report signs and symptoms of DMEA exposure.
- Develop evacuation plans to be used in the event of leaks, spills, or accidents that may cause high concentrations of DMEA in the workplace.
Editors of appropriate trade and union newsletters and journals, and those responsible for health and safety (managers, industrial hygienists, occupational health physicians, and nurses) are requested to bring these recommendations to the attention of gray-iron and aluminum foundry workers, managers, and owners, polyamide manufacturers, and other users of DMEA.
Requests for additional information on control practices should be directed to Mr. Jay Bainbridge, Acting Director, Division of Surveillance, Hazard Evaluations, and Field Studies (DSHEFS), National Institute for Occupational Safety and Health, 5555 Ridge Avenue,
Cincinnati, Ohio 45213, telephone 513-841-4428. Other questions related to this announcement should be directed to Mr. Richard A. Lemen, Director, Division of Standards Development and Technology Transfer (DSDTT), National Institute for Occupational Safety and Health, 4676 Columbia Parkway, Cincinnati, Ohio 45226, telephone 513-533-8302.
We greatly appreciate your assistance.
[signature]
J. Donald Millar, M.D., D.T.P.H. (Lond.)
Assistant Surgeon General
Director, National Institute for Occupational Safety and Health
Centers for Disease Control
References
Ashland Chemical Company [1983]. Material safety data sheet: dimethylethylamine, No. 3609-002. Columbus, OH: Division of Ashland Oil, Inc.
Beard RR, Noe JT [1981]. Aliphatic and alicyclic amines. In: Clayton GD and Clayton FE (eds.) [1981]. Patty's industrial hygiene and toxicology. 3d rev. ed., Vol. 2B. New York, NY: John Wiley and Sons, p. 1349.
Hartle R. [1982]. Hazard evaluation report: Keokuk Steel Castings, Inc., Keokuk, IA. Cincinnati, OH: U.S. Department of Health and Human Services, Public Health Service, Centers for Disease Control, National Institute for Occupational Safety and Health, NIOSH Report No. HETA 80-081-1173.
Rivera RO [1976]. Hazard evaluation and technical assistance report: Morris Bean and Company, Yellow Springs, OH. Cincinnati, OH: U.S. Department of Health, Education, and Welfare, Center for Disease Control, National Institute for Occupational Safety and Health, NIOSH Report No. 74-110-306.
Ruhe R [1984]. Hazard evaluation and technical assistance report: Midwest Foundry, Coldwater, MI. Cincinnati, OH: U.S. Department of Health and Human Services, Public Health Service, Centers for Disease Control, National Institute for Occupational Safety and Health, NIOSH Report No. HETA 83-131-1412.
Schmitter H [1977]. Investigation of the cold-box and shell mold casting methods from the standpoint of occupational medicine and occupational hygiene. Giesserei 71:895-902.
Stephenson RL [1984]. Hazard evaluation and technical assistance report: The Dotson Company, Mankato, MN. Cincinnati, OH: U.S. Department of Health and Human Services, Public Health Service, Centers for Disease Control, National Institute for Occupational Safety and Health, NIOSH Report No. HETA 82-348-1442.
Stephenson RL, Albrecht WN [1986]. Hazard evaluation and technical assistance report: Winters Industry Foundry, Canton, OH. Cincinnati, OH: U.S. Department of Health and Human Services, Public Health Service, Centers for Disease Control, National Institute for Occupational Safety and Health, NIOSH Report No. HETA 85-482-1730 and 86-116- 1730.
- Page last reviewed: June 6, 2014
- Page last updated: June 6, 2014
- Content source:
- National Institute for Occupational Safety and Health Education and Information Division